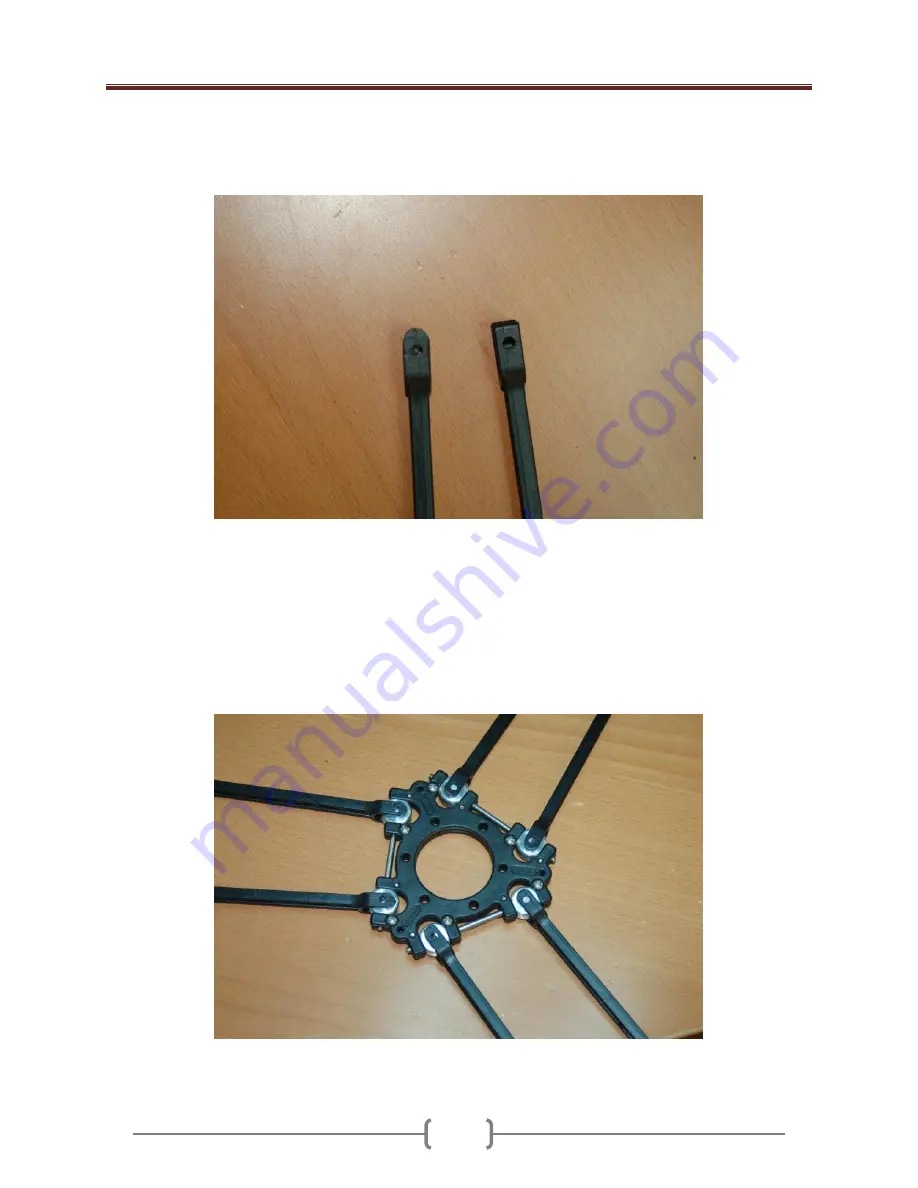
Rostock Max Assembly Guide
36
15.10 - The arms have square corners, but they should have a radius to them. To do this, grab
a sheet of 100 grit sandpaper or a good file and sand the corners so they look like the photo below.
(sanded arm on the left, un-sanded on the right)
Figure 51 - Radius Sanded in Arm End.
15.11 - After sanding the radius, you'll want to remove the flashing on the ends of the arms
so that they'll grip the U-Joints about the same as you did on the platform. The idea is to just
reduce the friction, not make them loose in the joint.
15.12 - Now fit the delta arms to the U-Joints. Snap them on to the U-Joints that are attached to
the platform. Use a twisting motion to get them on there. They're tight, but they will fit.
Figure 52 - Arms Installed on the U-Joints