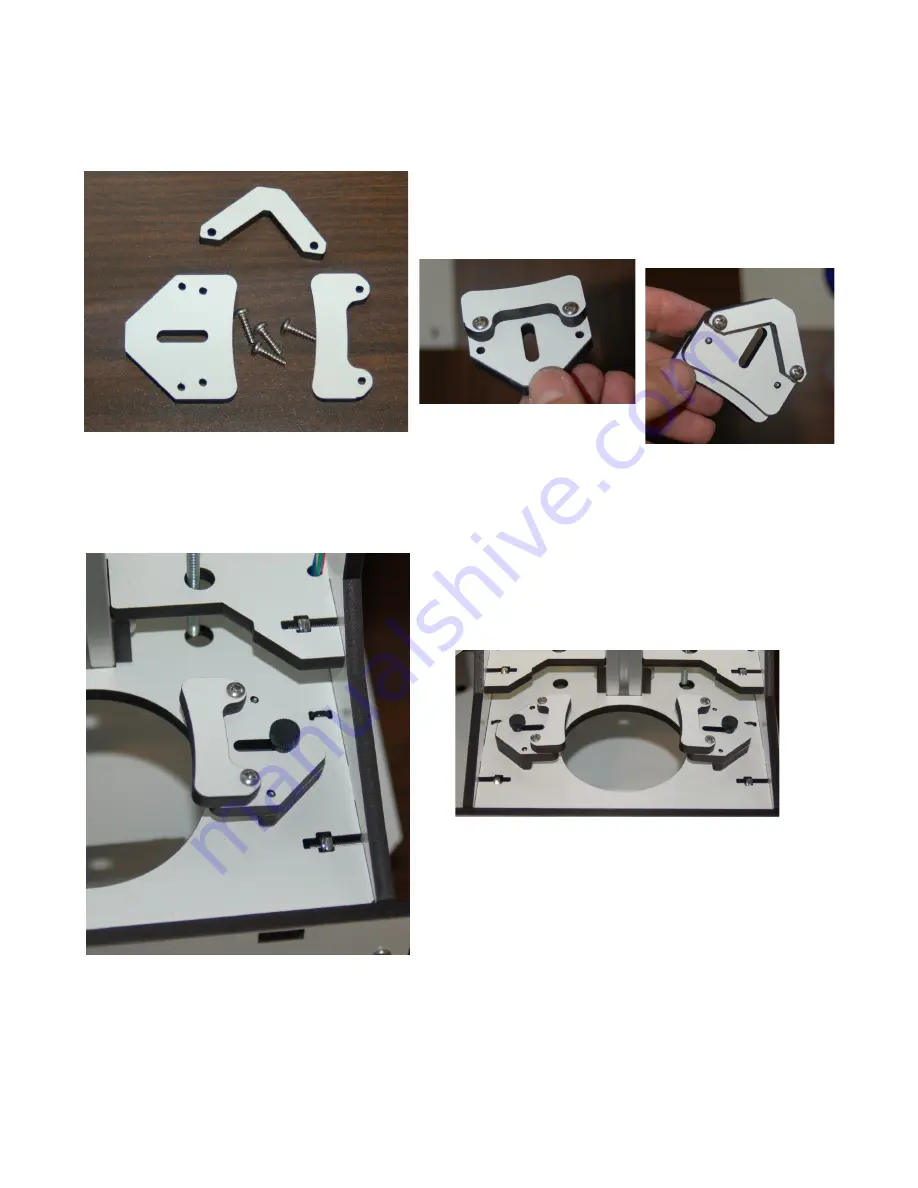
DropLit Assembly Guide
Now let's get the vat clamps assembled! You'll need the following parts for each one:
The vat clamp is really simple to assemble. First,
attach a Tall Vat Holddown using two of the #6, 1/2” Pan
Head Machine screws to the Vat Holddown Top part.
Next, flip that assembly over and install a Vat Holddown Bottom
using another pair of the #6 screws. When you've assembled both of the vat clamps, you can install
them on the Dish Plate using two of the knurled thumbscrews as shown below.
71
Fig. 7-19: Vat clamp parts.
Fig. 7-20: Step 1
Fig. 7-21: Step 2.
Fig. 7-22: Vat clamp installed.
Fig. 7-23: Both clamps in place.