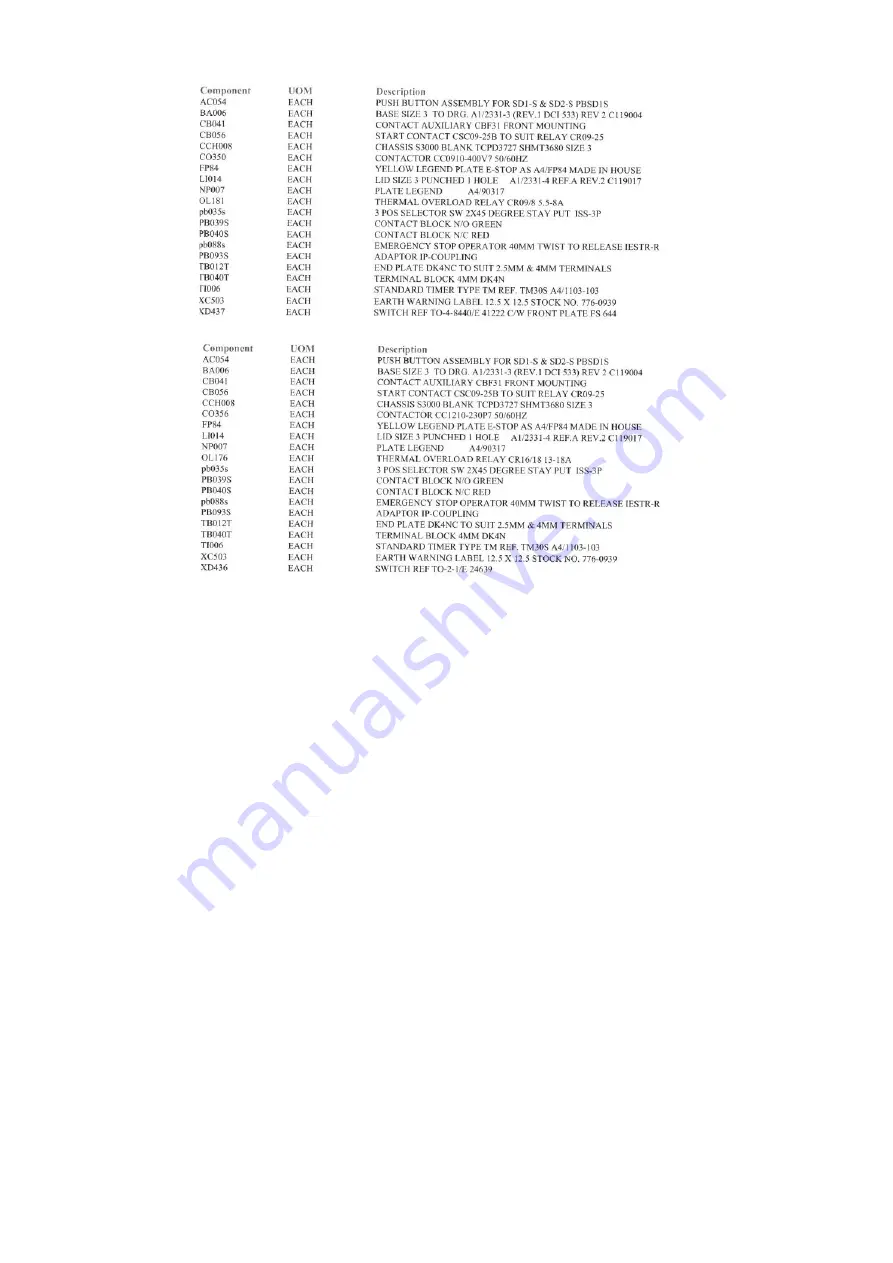
36
3SE0020A
MB/CP-1 STARTER 14/16A C/W BRAKE RELEASE
SCL027
'SEDGWICK' LOGO
SAFETY NOTICE
RUBBER WASHERS 55X18X3MM
BASE ASSEMBLY
7010
COLUMN HOUSING
7011
RISE & FALL SHAFT GEAR HOUSING
7012
THICKNESS TABLE SUPPORT HOUSING
702/18
RISE & FALL COLUMN
703/18
RISE & FALL NUT
704-3
RISE & FALL SCREW
51104 THRUST BEARING
021
GEAR WHEEL
024
GEAR PINION
708/18
HANDWHEEL SHAFT
DIA 200MM SINGLE SPOKE HANDWHEEL
THICKNESS TABLE ASSEMBLY
MB720
THICKNESS TABLE
MB721
THICKNESS TABLE SUPPORT
M12X50 LOCKING LEVER
MB723
GUIDE BARS
AM121612 OILITE BEARING
MB726
EXTENSION ROLLERS
0-230MM S/A RULE
MB727/2
DEPTH POINTER