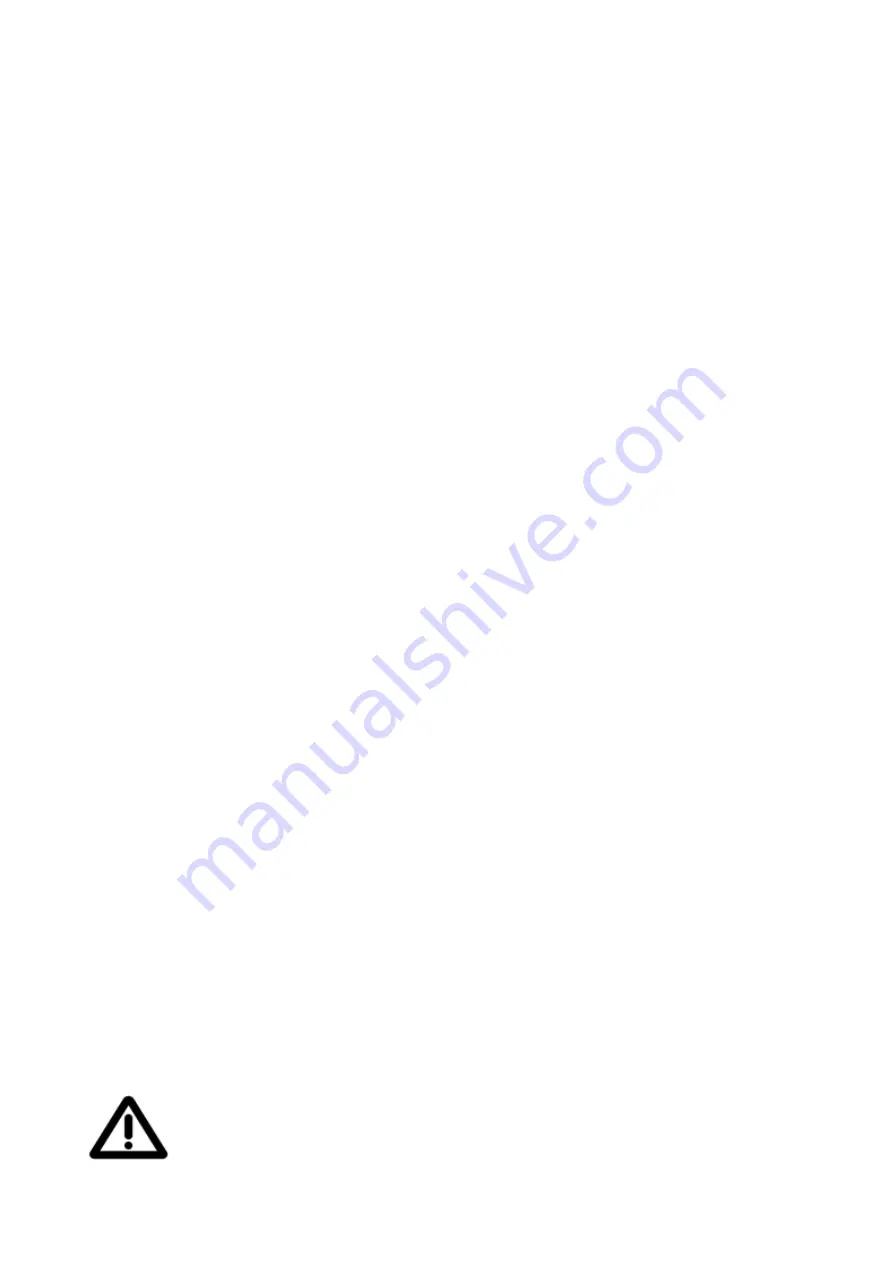
30
13.1 Lubrication
Since your planer thicknesser is constructed of cast iron, which is a porous metal, care should be
taken when cleaning. Use mineral spirits and steel wool on all metal parts. Avoid contact with
anything moist. Don’t set drinks on the table top, or leave green wood on it. These will leave
permanent marks.
Waxing the table surface will help resist moisture, as well as reducing friction on the
workpiece. Avoid products that contain silicone, anti-slip additives, or abrasives.
Clean the interior of the machine frequently to prevent the accumulation of chips and
sawdust around the motor and rise and fall mechanisms.
Once clean, lubricate moving parts using a lubricant that does not pick up a lot of sawdust.
Pay particular attention to the following: the drive chain, thickness table rise and fall
barrel, thickness table rise and fall screw, thickness table rise and fall gears, surface table
screw and slide assembly, fence table bar, fence swivel screw, and the front cutterblock
guard vertical support bar.
Powdered graphite, hard wax or white lithium spray is ideal. Do
not use an oil-based product. These will collect sawdust and congeal into a gummy
substance, making working parts hard to operate. Drive belts will also deteriorate if they
come into contact with oil.
13.2 Cutterblock and Bearings
The cutterblock needs very little maintenance, but it should be checked for wear, burrs and any
play in the bearings that the arbor rides in.
First check the cutterblock, the chipbreakers, and the cutterblock screws for dirt, burrs or
raised nicks. Slight imperfections can be removed carefully with a fine-cut file.
The cutterblock bearings are sealed for life and require no lubrication. To check their condition,
turn the block by hand while feeling for any roughness. Grasp the arbor on the drive side of the
block and gently pull up and down to check for any play. Roughness or slack in the bearings
means that they need to be replaced.
13.3 Vee Belts and Pulleys
The cutterblock is driven via two A64 vee belts and the feed by a chain mechanism. To prevent
loss of power, excess stopping times and/or belt slip these belts should be correctly tensioned
and regularly checked for wear.
When the belts begin to show signs of wear replace them. Frayed belts will cause vibration,
putting unnecessary strain on the arbor bearings. Instructions on changing/re-tensioning the
drive belts are as follows:
You will need two A64 vee belts, a rule, a 13mm spanner and a 19mm spanner.
Electrically isolate the machine and remove the back-guard. Loosen the two bolts at either end
of the motor mounting bar and use the adjusting stud to bring the two pulleys closer together.
Replace the worn belts and re-tension (effectively taking the motor farther from the cutterblock
arbor). The motor mounting bar can then be re-tightened and the rear machine guard replaced.
Finally, ensure that the cutterblock comes to rest within ten seconds of pressing the stop
button.
Do not over-tension the drive belts. Adjust the tensioner only until the drive
belt is sufficiently tensioned to transmit power effectively.