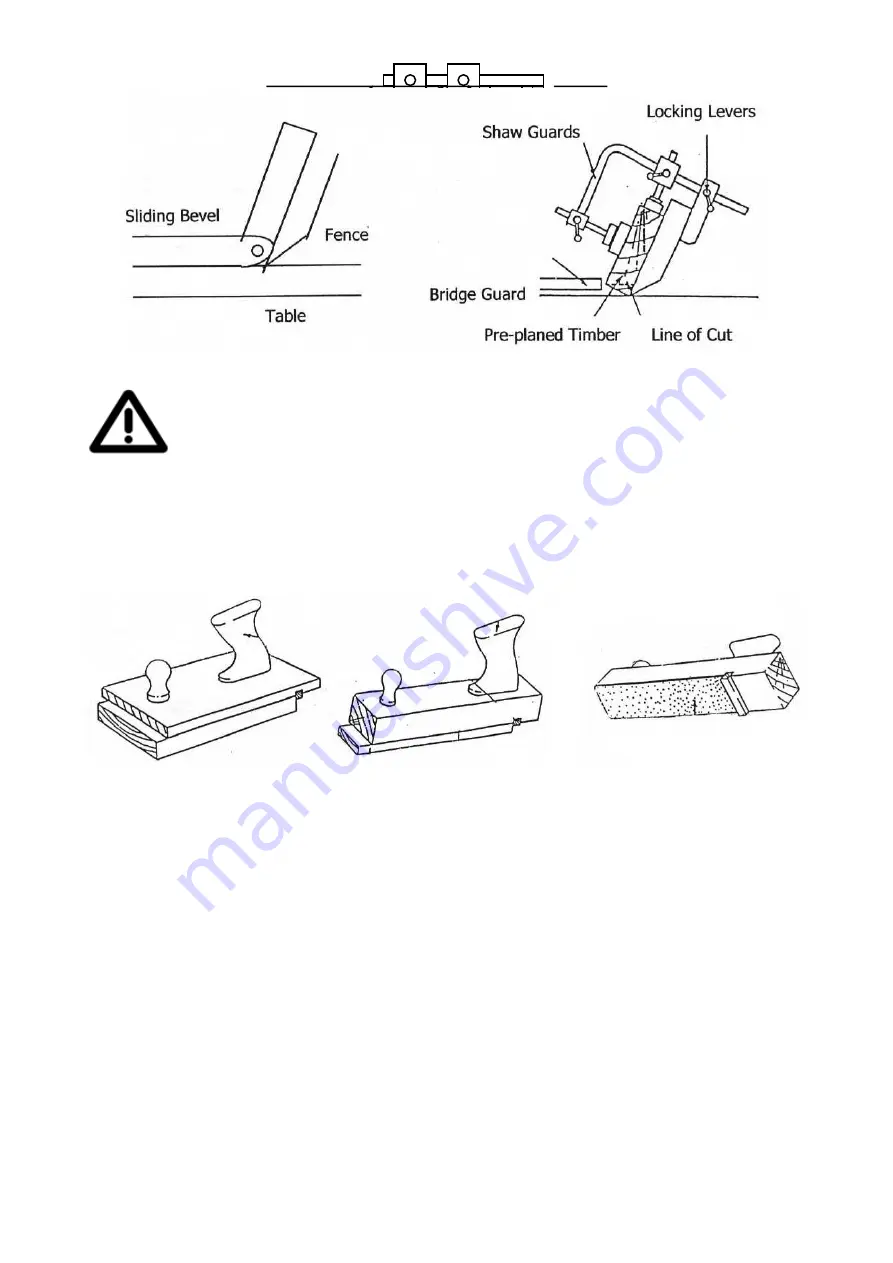
22
9.7 Push Blocks and Push Sticks
When planing smaller workpieces always use a push stick or push block.
In some operations push blocks should be used, especially when planing short pieces of timber
where it is necessary to pass the workpiece between the edge of the bridge guard and fence.
They should be constructed so as to give the machinist a firm grip and so reduce the risk of his
hands coming into contact with the cutters. A push block will reduce the risk of a short
workpiece dipping as it passes the lip of the feed table, thus making such abrupt contact with
the cutters that a throwback will be almost inevitable.
Handle doweled and glued to
pushstick therefore no metal
contact possible with the
cutters.
Hardwood
strip
housed and glued to body of
pushblock
Narrow pushblock for short
narrow thin material
Abrasive paper glued to base
to give better frictional grip
and prevent the workpiece
moving sideways
10.0 Thicknessing
Raising or lowering the thicknessing bed alters the depth of cut. Use the Thicknessing Table Rise
and Fall Handwheel and read off the thicknessing depth scale. Remember to lock the table in
position once the depth is set. Never try to remove too much at one pass.
3mm should be the
maximum.
Feed rollers at the front and rear of the cutterblock push and pull the wood through the rotating
cutter knives. The infeed roller is located at the front of the block and is made of serrated steel.
In order for it to operate effectively it must be kept free of resin. Clean off any build up of resin