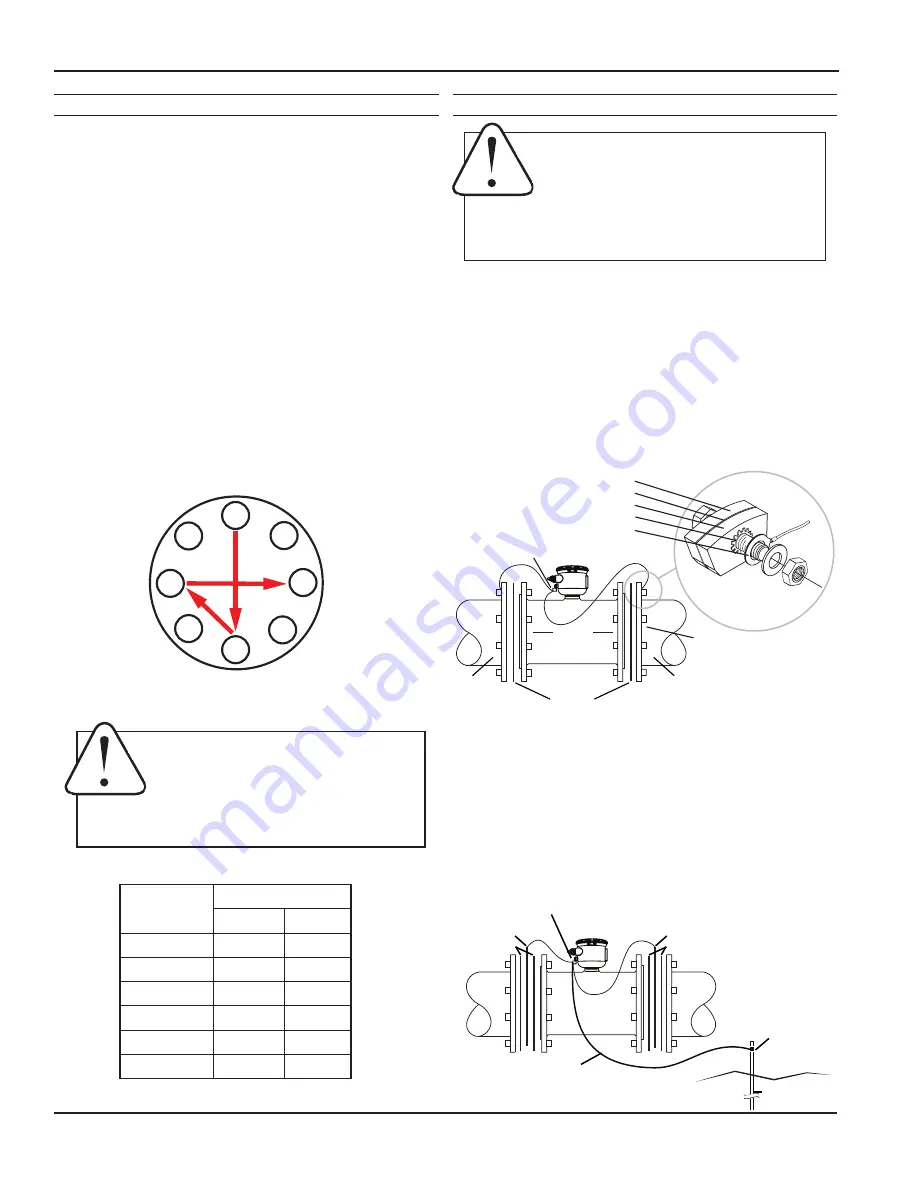
AG3000 INSTRUCTIONS
Seametrics • 253.872.0284
Page 10 seametrics.com
Equalization and Grounding
Metal Pipe Installations.
To equalize the electrical
potential of the fluid, the AG3000 meter, and the
surrounding pipe, secure the flange plates (factory-installed
on the equalization wire) to both pipe flanges at one of the
bolt holes, as shown below. Be sure the lock washer fits
between the pipe flange and the flange plate. For the best
electrical bonding, remove rust and paint to expose clean,
bare metal where the equalization flange plate lock washer
contacts the pipe flange. Connection must be inspected
periodically for corrosion to maintain the necessary low
resistance connection.
Plastic Pipe and Electronically Noisy Installations.
When the
AG3000 is installed in plastic pipe or in an electrically noisy
system (near a VFD etc.), grounding rings are recommended.
As shown in the diagram below, the equalization wires should
be solidly connected to the grounding ring tabs instead of the
flange bolts as in metal piping installations. Where lightning
is a threat, or in severe electrical environments, an optional
connection to a nearby equipment ground or ground rod may
be advisable.
WARNING: ELECTRICAL SHOCK HAZARD
When the AG3000 is installed in a plastic
piping system, or when externally powered,
the piping system must be grounded to
meet national and local electrical safety
codes. Failure to do so can result in
electrocution.
Equalization Lug
Meter
Flange
Pipe
Flange
Gasket
Pipe Flange
Flange Plate
Lockwasher
Metal Pipe
Metal Pipe
Meter Flange
Gaskets
Equalization Lug
Ground Clamp
(Exothermically weld when
corrosion is a concern)
8’ Ground Rod
Earth
Grounding Ring
Gaskets
Grounding Ring
Gaskets
#6, #8, or #12 AWG Stranded
Copper Ground Wire < 5’
Plastic
Pipe
Plastic
Pipe
Grounding Ring Part Numbers:
3” = 102157 8” = 100878
4” = 100876 10” = 100879
6” = 100877 12” = 103288
INSTALLATION
Tightening Flange Bolts
NOTE: Mating pipe flanges must be ANSI 150# full face (FF)
and/or raised face (RT).
1.
Tighten flange bolts in an alternating pattern.
•
Tighten left flange bolt-1 to 20% recommended
torque.
•
Tighten right flange bolt-1 to 20% of
recommended torque.
• Repeat steps a and b for each bolt in an
alternating order, such as shown at right,
tightening to 40%, then 60%, then 80%, and
then 100%.
2. Test for leaks.
3. If needed, tighten further in 10% increments
until leaking stops.
DO NOT over-tighten. Over-
tightening can cause serious damage to the flow
meter.
4. Recheck after 24 hours, adjusting if needed.
Suggested Tightening Sequence
Caution:
Improper tightening sequence
can cause serious damage to the flow
meter.
•
Do not tighten one side at a time.
•
Do not tighten each bolt completely
at one time.
Liner
Pipe Size
ft-lb
Nm
3”
25
34
4”
20
27
6”
42
57
8”
65
88
10”
73
99
12”
97
132
SUGGESTED FLANGE BOLT TORQUE
1
2
3
4
5
6
7
8