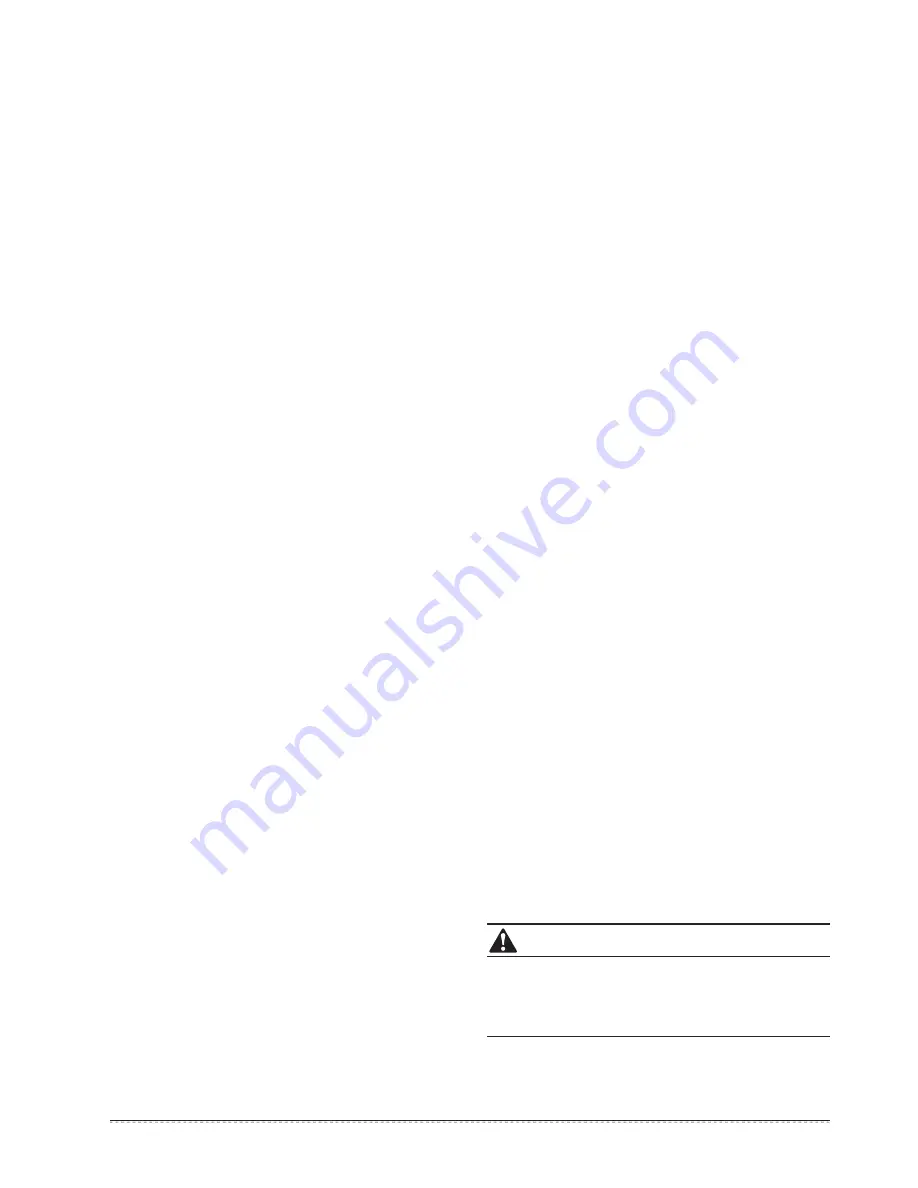
25
I&O manual
8.7 Winter shutdown
For shutdown in winter, the surface of the unit outside and inside
should be cleaned and dried. Cover the unit to prevent dust. Open
discharge water valve to discharge the stored water in the clean
water system to prevent freezing accident (it is preferable to inject
antifreezer in the pipe).
8.8 Replacing parts
Parts to be replaced should be the ones provided by our company.
Never replace any part with different part.
8.9 First startup after shutdown
The following preparations should be made for re-startup of unit
after long-time shutdown:
1) Thoroughly check and clean the unit.
2) Clean water pipe system.
3) Check pump, control valve and other equipments of water pipe
system.
4) Fix connections of all wires.
5) It is a must to electrify the machine 12 hours before startup.
8.10 Refrigeration system
Determine whether refrigerant is needed by checking the value of
suction and discharge pressure and check whether there is a
leakage. Air tight test must be made if there is a leakage or parts
of refrigerating system is to be replaced. Take different measures
in the following two different conditions from refrigerant injection.
1) Total leakage of refrigerant. In case of such situation, leakage
detection must be made on the pressurized nitrogen used for the
system. If repair welding is needed, welding cannot be made until
all the gas in the system is discharged. Before injecting
refrigerant, the whole refrigeration system must be completely dry
and of vacuum pumping.
●
Connect vacuum pumping pipe at the fluoride nozzle at
low-pressure side.
●
Remove air from the system pipe with vacuum pump. The
vacuum pumping lasts for above 3 hours. Confirm that the
indication pressure in dial gauge is within the specified scope.
●
When the degree of vacuum is reached, inject refrigerant into
the refrigeration system with refrigerant bottle. Appropriate amount
of refrigerant for injection has been indicated on the nameplate
and the table of main technical parameters. Refrigerant must be
injected from the low pressure side of system.
●
The injection amount of refrigerant will be affected by the
ambient temperature. If the required amount has not been
reached but no more injection can be done, make the chilled
water circulate and start up the unit for injection. Make the low
pressure switch temporarily short circuit if necessary.
2) Refrigerant supplement. Connect refrigerant injection bottle on
the fluoride nozzle at low-pressure side and connect pressure
gauge at low pressure side.
●
Make chilled water circulate and start up unit, and make the low
pressure control switch short circuit if necessary.
●
Slowly inject refrigerant into the system and check suction and
discharge pressure.
Maintenance of main parts
●
Close attention should be paid to the discharge and suction
pressure during the running process. Find out reasons and
eliminate the failure if abnormality is found.
●
Control and protect the equipment. See to it that no random
adjustment be made on the set points on site.
●
Regularly check whether the electric connection is loose, and
whether there is bad contact at the contact point caused by
oxidation and debris etc., and take timely measures if necessary.
Frequently check the work voltage, current and phase balance.
●
Check the reliability of the electric elements in time. Ineffective
and unreliable elements should be replaced in time.
8.6 Removing scale
After long-time operation, calcium oxide or other minerals will be
settled in the heat transfer surface of the water-side heat
exchanger. These substances will affect the heat transfer
performance when there is too much scale in the heat transfer
surface and sequentially cause that electricity consumption
increases and the discharge pressure is too high (or suction
pressure too low). Organic acids such as formic acid, citric acid
and acetic acid may be used to clean the scale. But in no way
should cleaning agent containing fluoroacetic acid or fluoride
should be used as the water-side heat exchange is made from
stainless steel and is easy to be eroded to cause refrigerant
leakage. Pay attention to the following aspects during the cleaning
and scale-removing process:
●
Water-side heat exchanger should be done be professionals.
Please contact the local air-conditioner customer service center.
●
Clean the pipe and heat exchanger with clean water after
cleaning agent is used. Conduct water treatment to prevent water
system from being eroded or re-absorption of scale.
●
In case of using cleaning agent, adjust the density of the agent,
cleaning time and temperature according to the scale settlement
condition.
●
After pickling is completed, neutralization treatment needs to be
done on the waste liquid. Contact relevant company for treating
the treated waste liquid.
●
Protection equipments (such as goggles, gloves, mask and
shoes) must be used during the cleaning process to avoid
breathing in or contacting the agent as the cleaning agent and
neutralization agent is corrosive to eyes, skins and nasal mucosa.
8.5 Care and maintenance
Maintenance period
It's recommended that before cooling in summer and heating in
winter every year, consult local air conditioner customer service
center to check and maintain the unit, to prevent air conditioner
errors which bring inconvenience to your life and work.
●
Connection must be renewed after injection is completed.
●
Never inject oxygen, acetylene or other flammable or poisonous
gas to the refrigeration system at leakage detection and air tight
test. Only pressurized nitrogen or refrigerant can be used.
CAUTION