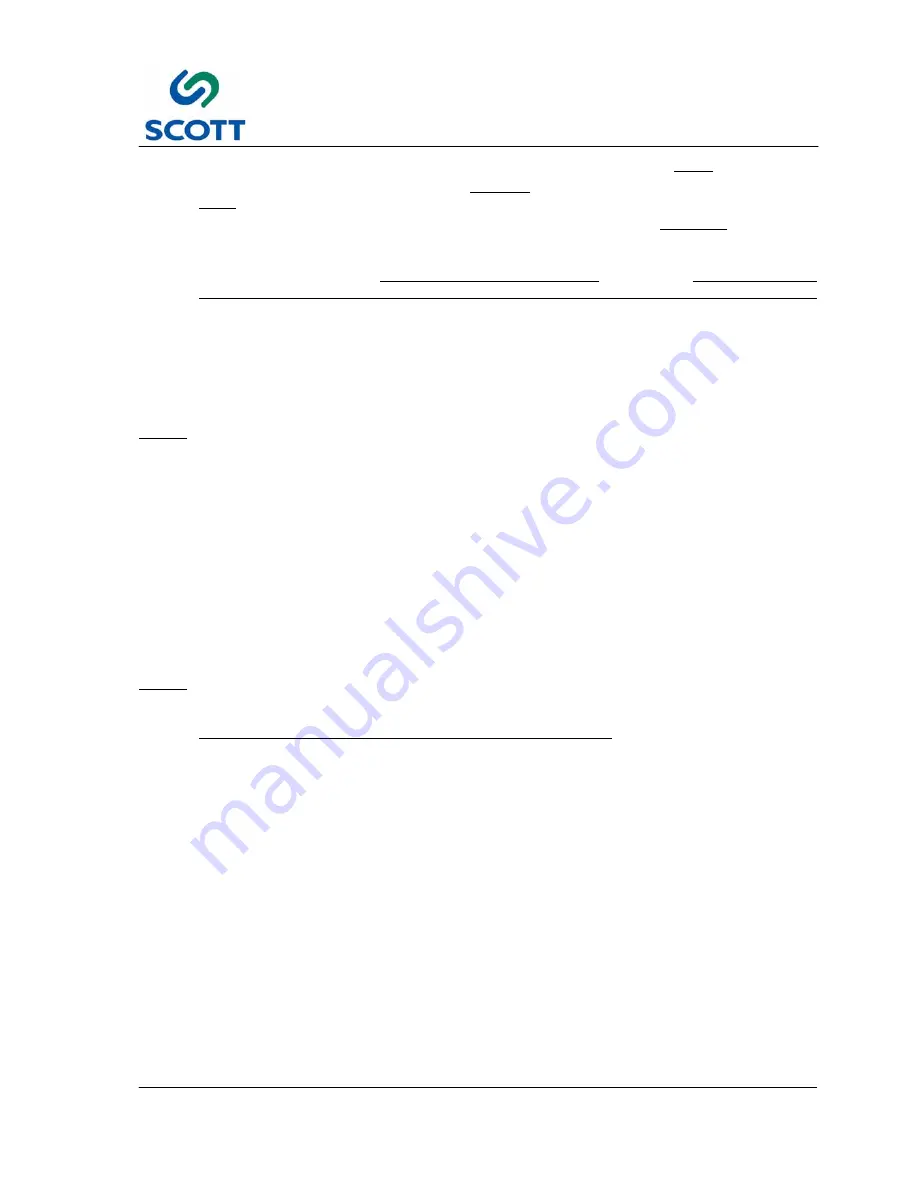
4 Maintenance
4--29
F--9999--8 Build 8 Issue 1
Step: 4.
Set the lower knife in position against the upper knife. Install the screws but do not tighten them.
Step: 5.
Move the wrench into a position so that the full length of the cutting edge of the upper knife is just
below the cutting edge of the lower knife.
Step: 6.
Slide the lower knife into position against the upper knife so that you have full contact of the two
blades----at the contour and the entire length of the blades.
Step: 7.
In this step, you will “clear” the knives so that although set closely they will not bump or rub. To do
this, remove the wrench and very carefully rotate the upper knife once or twice. NOTE: LEAVE THE
LOWER KNIFE FREE WHEN DOING THIS. DO NOT PUSH THE LOWER AGAINST THE UPPER.
This “clearing action” will move the lower blade away from the upper. After the “clearing action” the
knives are still very close to each other but if they were too close the procedure automatically puts
the lower in the proper position since the screws on the lower knife have not yet been tightened.
Step: 8.
Then....(1) tighten the center screw, (2) tighten the screw at the contour end and (3) tighten screw
at the off--contour end. You may tighten the screws in any order if this helps to keep the blade from
moving.
Note !
The “clearing action” may be used each time a screw is tightened to insure that you have
not twisted the lower knife or pushed it against the upper. You do not want the knives to
bump or rub.
Step: 9.
After the three screws have been tightened, again “clear” the blades to make sure no bumps or
rubs. A very slight “brushing” of the blades is acceptable.
Step: 10.
Then .... take a piece of .002 (.05mm) Mylar index tab film and check the cutting ability of the
knives. It is necessary that they cut this thin film at the contour and at least one inch away from the
contour. It is not necessary that they cut the thin film the entire length of the blade (all that is
necessary is that this part cut thin 20 lb. paper)
Step: 11.
Tighten all the other screws and then recheck with the “clearing action” and the .002” (.05mm)
Mylar.
Step: 12.
If the blades do not cut the Mylar, repeat the above steps until the cutting is satisfactory.
Note !
IF YOU HAVE A “PERFECT SETTING” AND AFTER RUNNING THE MACHINE AWHILE YOU
NOTICE THAT THEY “SQUEAK”, GO THROUGH THE ENTIRE PROCEDURE AGAIN. IF YOU
HAVE TO DO THIS ONCE, WE HAVE FOUND THAT THE “SQUEAK” WILL NOT RE- OCCUR.
DO NOT PUT OIL ON THE KNIVES TO ELIMINATE THE NOISE. YOU MUST RESET THE
KNIVES.
If you cannot get the proper setting by doing the above procedure, send your knives to Scott for sharpening.
DO NOT JAM THE KNIVES INTO EACH OTHER TO MAKE THEM CUT.
The above procedure is important for several reasons:
1.
If the above is not done, your knives will require much more sharpening than they should. This alone is
expensive.
2.
If the above is not done, you will need new knives much more often. The knives are made to very close
tolerances and are extremely expensive.
3.
If the machine is run with dull knives or the lower knives are jammed against the uppers, you can ruin
the tab cutting packages and operating cylinders of your machine. Replacement of the packages is an
expensive job with machine down time of weeks, depending on the availability of the new replacement
packages.
IMPORTANT:
MAKE SURE YOUR OPERATORS FOLLOW THE ABOVE PROCEDURE. THERE ARE NO
ALTERNATE PROCEDURES THAT WILL WORK SATISFACTORILY IN THE LONG RUN.
Summary of Contents for Scotty 5000
Page 2: ...ISSUE NOTE This is Issue 1 Date of Issue August 2006 Copyright 2006...
Page 7: ...V F 9999 8 Issue 1 6 ELECTRICAL AND PNEUMATICS 6 1...
Page 8: ...1 Introduction and Safety 1 1 F 9999 8 Build 8 Issue 1 1 INTRODUCTION AND SAFETY...
Page 21: ...2 Installation 2 1 F 9999 8 Build 8 Issue 1 2 INSTALLATION...
Page 22: ...2 Installation 2 2 F 9999 8 Build 8 Issue 1...
Page 31: ...3 Operation 3 1 F 9999 8 Build 8 Issue 1 3 OPERATION...
Page 32: ...3 Operation 3 2 F 9999 8 Build 8 Issue 1...
Page 62: ...3 Operation 3 32 F 9999 8 Build 8 Issue 1...
Page 63: ...3 33 F 9999 8 Issue 1 3 4 Handwheel and Tab Set Up...
Page 65: ...3 35 F 9999 8 Issue 1 Note Page intentionally left blank...
Page 94: ...4 Maintenance 4 1 F 9999 8 Build 8 Issue 1 4 MAINTENANCE...
Page 95: ...4 Maintenance 4 2 F 9999 8 Build 8 Issue 1...
Page 136: ...5 SCOTTY 5000 PARTS 5 1 F 9999 8 08 2006 Issue 1 5 SCOTTY 5000 PARTS...
Page 143: ...5 8 5 SCOTTY 5000 PARTS F 9999 8 08 2006 Issue 1 5 3 PILE FEED DRIVE ROLLER ASSEMBLY...
Page 151: ...5 16 5 SCOTTY 5000 PARTS F 9999 8 08 2006 Issue 1 5 7 PILE FEED VACUUM BAR...
Page 173: ...3 3 5 38 5 SCOTTY 5000 PARTS F 9999 8 08 2006 Issue 1 5 18 PILE FEED OPTIC MOUNTING...
Page 181: ...5 46 5 SCOTTY 5000 PARTS F 9999 8 08 2006 Issue 1 5 22 PLATEN UNIT...
Page 183: ...5 48 5 SCOTTY 5000 PARTS F 9999 8 08 2006 Issue 1 5 23 REGISTER BOARD HOLD DOWN PLATE...
Page 187: ...5 52 5 SCOTTY 5000 PARTS F 9999 8 08 2006 Issue 1 5 25 MIDDLE REGISTER HOLD DOWN PLATE...
Page 193: ...5 58 5 SCOTTY 5000 PARTS F 9999 8 08 2006 Issue 1 5 28 MIDDLE REGISTER BOARD DRIVE A...
Page 197: ...5 62 5 SCOTTY 5000 PARTS F 9999 8 08 2006 Issue 1 5 30 TAB CUTTER KNIFE CARRIER L H...
Page 199: ...5 64 5 SCOTTY 5000 PARTS F 9999 8 08 2006 Issue 1 5 31 TAB CUTTER KNIFE CARRIER R H...
Page 201: ...5 66 5 SCOTTY 5000 PARTS F 9999 8 08 2006 Issue 1 5 32 TAB CUTTER A...
Page 207: ...5 72 5 SCOTTY 5000 PARTS F 9999 8 08 2006 Issue 1 5 35 TIP DIE UNIT...
Page 211: ...5 76 5 SCOTTY 5000 PARTS F 9999 8 08 2006 Issue 1 5 37 HANDWHEEL UNIT PLASTIC SIZE...
Page 213: ...5 78 5 SCOTTY 5000 PARTS F 9999 8 08 2006 Issue 1 5 38 HANDWHEEL UNIT TAB SIZE...
Page 235: ...5 100 5 SCOTTY 5000 PARTS F 9999 8 08 2006 Issue 1 5 49 PLASTIC REEL HOLDER...
Page 243: ...REF BASE DRIVE ASSY 5 108 5 SCOTTY 5000 PARTS F 9999 8 08 2006 Issue 1 5 53 GUARDS COVERS...
Page 247: ...5 112 5 SCOTTY 5000 PARTS F 9999 8 08 2006 Issue 1 5 55 MAIN MOTOR VACUUM PUMP...
Page 249: ...5 114 5 SCOTTY 5000 PARTS F 9999 8 08 2006 Issue 1 5 56 HOLD DOWN BAR...
Page 253: ...5 118 5 SCOTTY 5000 PARTS F 9999 8 08 2006 Issue 1 5 58 CHIP REMOVAL VACUUM...