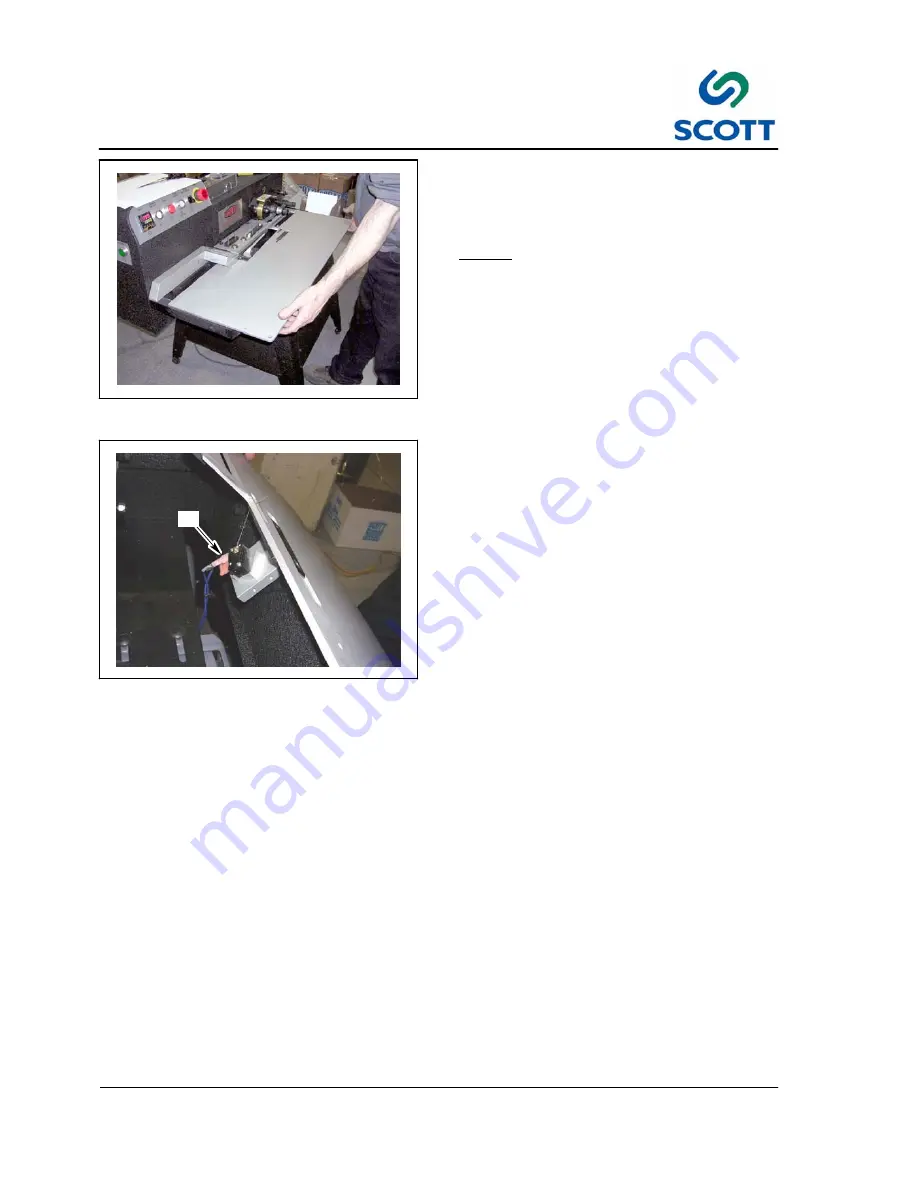
3 Operation
3--18
Edge Reinforcer Issue 1
Fig. 3-34. Lift Table Off Locating Pins
Step: 10.
Lift the outside of the table until it is off
the two locating pins and slide the table
slightly away from the machine by pulling
it towards you.
NOTE!
Do Not Pull Table Free of Machine.
The Trip Switch is still connected.
B
Fig. 3-35. Disconnect the Trip Switch
Step: 11.
Disconnect the wires to the trip switch (B)
which is located inside the table.
Step: 12.
Put table in safe place.
(See “Caution” paragraph above).
Step: 13.
Clean machine as necessary.
Step: 14.
Reinstall table in reverse order of
disassembly.
Summary of Contents for Edge Reinforcer
Page 2: ...ISSUE NOTE This is Issue 1 Date of Issue July 2006 Copyright 2006...
Page 7: ...1 Introduction Safety 1 2 Edge Reinforcer Issue 1...
Page 16: ...2 Installation 2 1 Edge Reinforcer Issue 1 2 INSTALLATION Edge Reinforcer Issue 1...
Page 17: ...2 Installation 2 2 Edge Reinforcer Issue 1...
Page 21: ...3 Operation 3 1 Edge Reinforcer Issue 1 3 OPERATION Edge Reinforcer Issue 1...
Page 22: ...3 Operation 3 2 Edge Reinforcer Issue 1...
Page 24: ...3 Operation 3 4 Edge Reinforcer Issue 1...
Page 50: ...4 Maintenance 4 1 Edge Reinforcer Issue 1 4 MAINTENANCE Edge Reinforcer Issue 1...
Page 51: ...4 Maintenance 4 2 Edge Reinforcer Issue 1...
Page 68: ...Page 5 4 5 Parts Scott Edge Reinforcer Issue 1 07 2006 5 1 Base Assembly...
Page 70: ...Page 5 6 5 Parts Scott Edge Reinforcer Issue 1 07 2006 5 2 Base Assembly...
Page 82: ...Page 5 18 5 Parts Scott Edge Reinforcer Issue 1 07 2006 5 8 Cover Assembly...
Page 102: ...Page 5 38 5 Parts Scott Edge Reinforcer Issue 1 07 2006 5 18 Housing Assembly...
Page 104: ...Page 5 40 5 Parts Scott Edge Reinforcer Issue 1 07 2006 5 19 Sprocket Mounting Assembly...
Page 112: ...Page 5 48 5 Parts Scott Edge Reinforcer Issue 1 07 2006 5 23 Leg Extension Assembly...