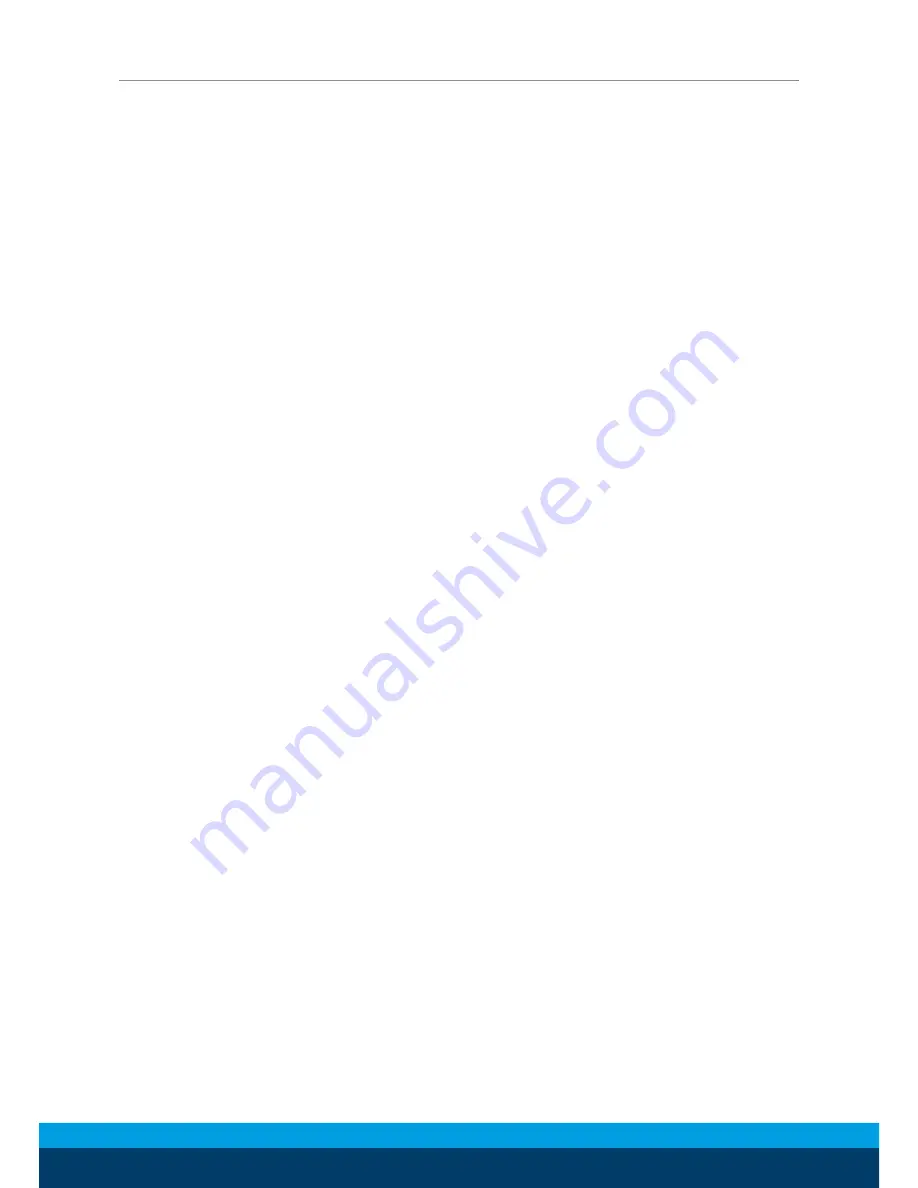
Operation
24
04.00 | Clamping device SVP-2D | Assembly and Operating Manual | en | 0289025
Setting after start:
Normal operation
.
Software version 1.3
• Locking manual operation via DataMatrix code
• P+- option for fine-tuning pressure once target pressure is
reached
Software version 1.4
• Locking manual operation via DataMatrix code
• P+- option for fine-tuning pressure once target pressure is
reached
• Device switched on via OK button (On) and P button (press and
hold 3 seconds, Off)
Software version 1.6
• Switch between the operating states scan operation and
manual operation.
To do this, hold down the OK button for 3 seconds.
6.4 Notes on clamping and unclamping
• Due to manufacturing and material tolerances, it is possible to
insert or loosen tools or workpieces even at a pressure below
the one indicated on the TRIBOS toolholder.
•
This lower pressure value may be significantly below the one
specified on the toolholder.
However, this has no influence on the indicated and
tranferable torque of the toolholder (see operating manual
TRIBOS polygonal toolholder)
• The tool/workpiece can already be clamped into the toolholder,
if the clamping device's actual unclamping pressure is slightly
exceeded. It is also possible that the tool can no longer be
inserted into the toolholder at the indicated pressure, but
instead at a value a few bars below.
• Continually check at which of the clamping device's pressure
levels the tool/workpiece can be inserted or loosened.
• If it proves impossible to loosen or insert the tool or workpiece
from or into the toolholder until the indicated pressure is
achieved, stop the clamping procedure. At first release the
pressure of the clamping device and afterwards check if
clearance between the flattened area of the toolholder and the
reduction insert is eliminated by turning the toolholder to the
right (clockwise). Repeat the clamping procedure.
• If it proves impossible to loosen or insert the tool/workpiece
despite correct positioning of the toolholder in the reduction
insert, unclamp the device and remove the reduction insert
together with the toolholder. Turn the reduction insert on the
toolholder by 120°, push it back into the clamping device and
repeat the clamping procedure. Now it should be possible to
loosen the tool/workpiece.