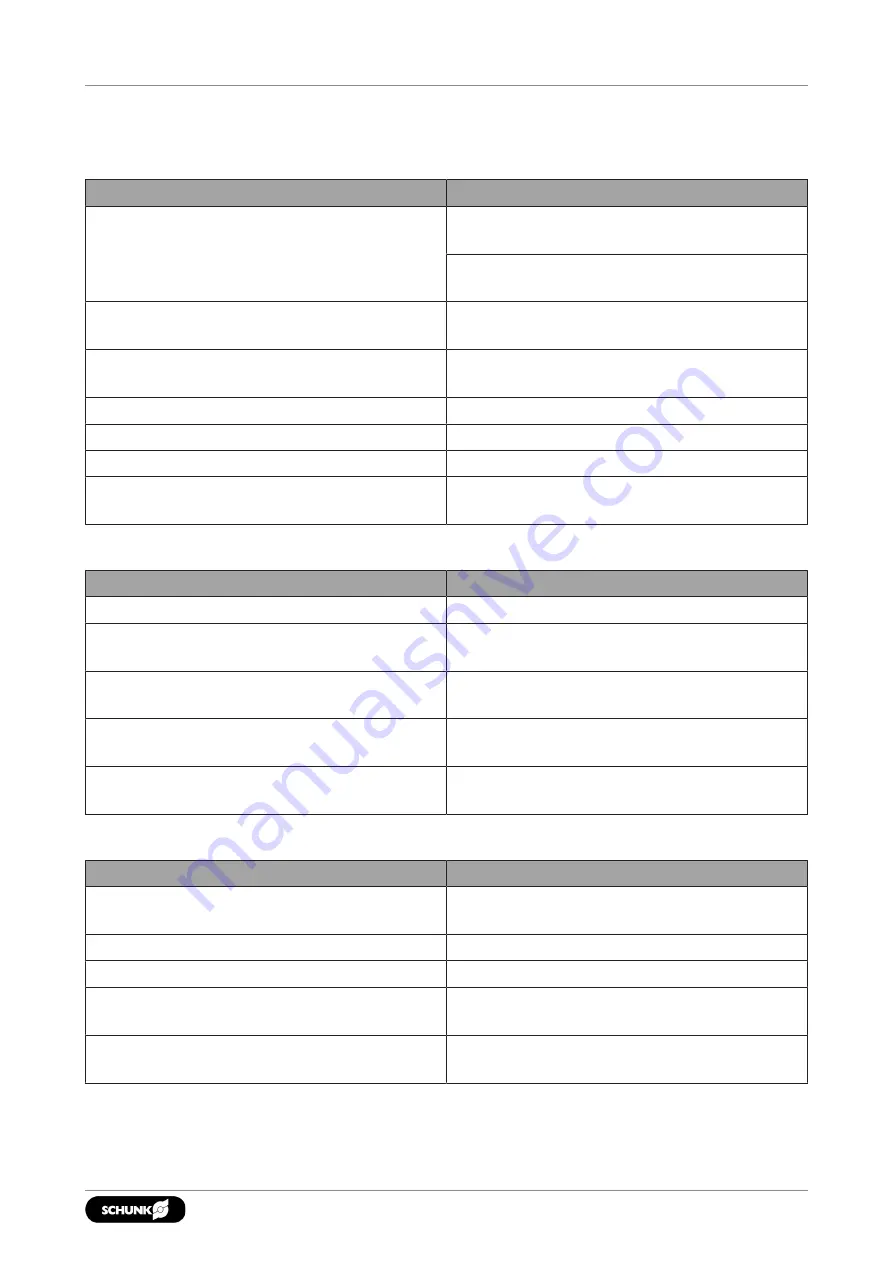
Troubleshooting
6 Troubleshooting
6.1 Product is not moving
Possible cause
Corrective action
Base jaws jam in housing, e.g. mounting
surface is not sufficiently even.
Check the evenness of the mounting surface.
Loosen the mounting screws of the product
and actuate the product again.
Pressure drops below minimum.
Check air supply.
Compressed air lines switched.
Check compressed air lines.
Proximity switch defective or set incorrect.
Readjust or change sensor.
Unused air connections open.
Close unused air connections.
Flow control valve closed.
Open the flow control valve.
Component part defective.
Replace component or send it to SCHUNK
for repair.
6.2 Product is not executing the complete stroke
Possible cause
Corrective action
Dirt deposits between cover and piston.
Clean and if necessary re-lubricate.
Dirt deposits between basic jaws and
guidance.
Disassemble and clean the product.
Pressure drops below minimum.
Check air supply.
Mounting surface is not sufficiently flat.
Check the evenness of the mounting surface.
Component part defective.
Replace component or send it to SCHUNK
for repair.
6.3 Product opens or closes abruptly
Possible cause
Corrective action
Too little grease in the mechanical guiding
areas.
Clean and lubricate product.
Compressed air lines blocked.
Check compressed air lines of damage.
Mounting surface is not sufficiently flat.
Check the evenness of the mounting surface.
One-way flow control valve is missing or
adjustet incorrectly.
Install and adjust one-way flow control
valve.
Loading too large.
Check permissible weight and length of the
gripper fingers.
35
09.00 | MPZ | Assembly- and Operating Manual | en | 389218