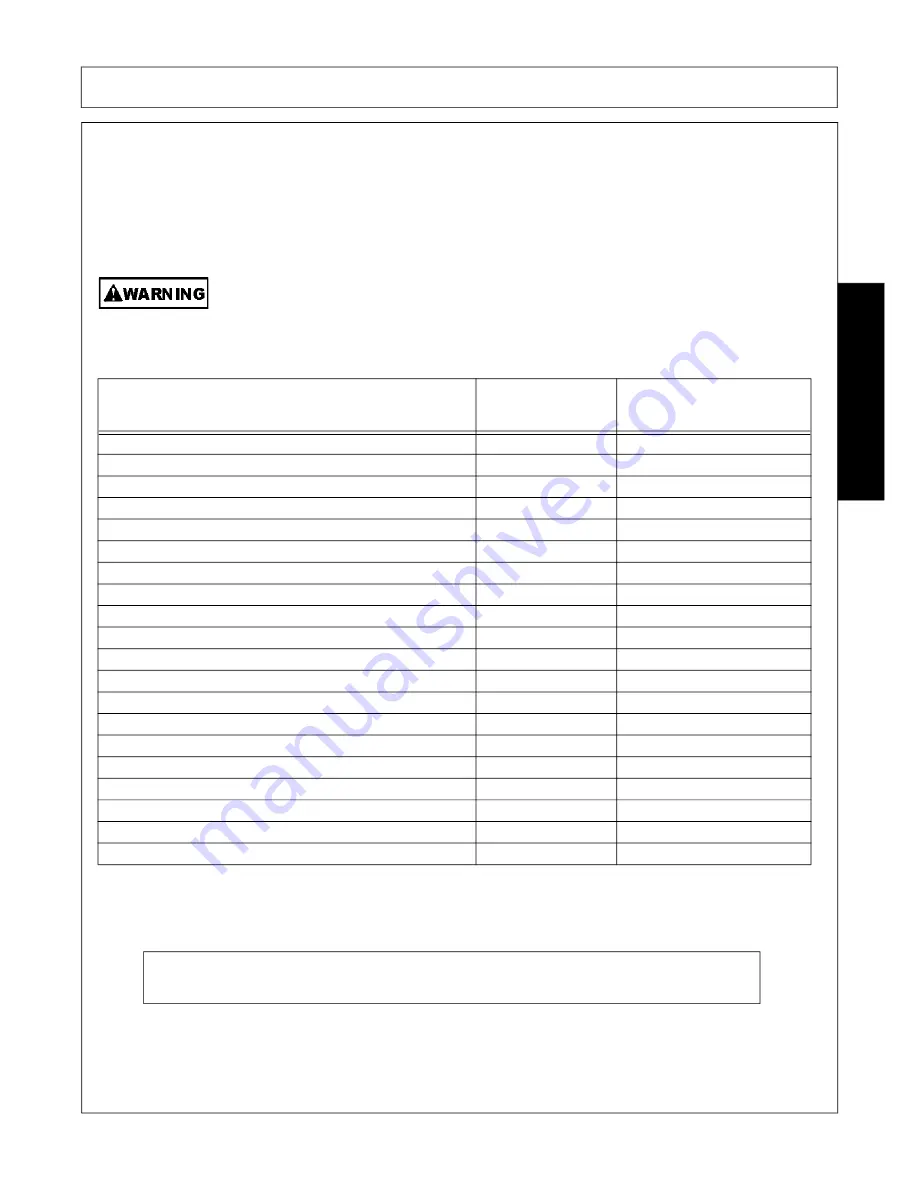
OPERATION
DHX-360/DHX-600 03/21
Operation Section 4-23
O
PE
R
AT
IO
N
© 2021 Alamo Group Inc.
Tractor PRE-OPERATION Inspection
Implement ID#______________________________________ Make______________________________
Date:______________________________________________ Shift______________________________
Before conducting the inspection, make sure the tractor engine is off, all rotation
has stopped and the tractor is in park with the parking brake engaged. Make sure
the implement is resting on the ground or securely blocked up and all hydraulic
pressure has been relieved.
Operator’s Signature:_________________________________________________________________
Item
Condition at Start
of Shift
Specific Comments if
not O.K.
The flashing lights function properly
The SMV Sign is clean and visible
The tires are in good condition with proper pressure
The wheel lug bolts are tight
The tractor brakes are in good condition
The steering linkage is in good condition
There are no visible oil leaks
The hydraulic controls function properly
The ROPS or ROPS Cab is in good condition
The seatbelt is in place and in good condition
The 3-point hitch is in good condition
The drawbar pins are securely in place
The PTO master shield is in place
The engine oil level is full
The brake fluid level is full
The power steering fluid level is full
The fuel level is adequate
The engine coolant fluid level is full
The radiator is free of debris
The air filter is in good condition
DO NOT OPERATE THE TRACTOR OR IMPLEMENT UNLESS
ALL CONDITIONS SHOWN ABOVE ARE OKAY
Summary of Contents for DHX-360
Page 3: ......
Page 6: ......
Page 9: ...Safety Section 1 1 SAFETY SECTION ...
Page 21: ...SAFETY DHX 360 DHX 600 03 21 Safety Section 1 13 SAFETY 2021 Alamo Group Inc ...
Page 25: ...SAFETY DHX 360 DHX 600 03 21 Safety Section 1 17 SAFETY 2021 Alamo Group Inc ...
Page 27: ...SAFETY DHX 360 DHX 600 03 21 Safety Section 1 19 SAFETY 2021 Alamo Group Inc ...
Page 29: ...SAFETY DHX 360 DHX 600 03 21 Safety Section 1 21 SAFETY 2021 Alamo Group Inc ...
Page 31: ...SAFETY DHX 360 DHX 600 03 21 Safety Section 1 23 SAFETY 2021 Alamo Group Inc ...
Page 33: ...Introduction Section 2 1 2021 Alamo Group Inc INTRODUCTION SECTION ...
Page 39: ...Assembly Section 3 1 2019 Alamo Group Inc ASSEMBLY SECTION ...
Page 42: ......
Page 43: ...Operation Section 4 1 OPERATION SECTION ...
Page 74: ......
Page 75: ...Maintenance Section 5 1 2021 Alamo Group Inc MAINTENANCE SECTION ...
Page 79: ...MAINTENANCE DHX 360 DHX 600 03 21 Maintenance Section 5 5 2021 Alamo Group Inc MAINTENANCE ...
Page 80: ......
Page 81: ......
Page 82: ...DHX 360 DHX 600 03 21 DH60 010C Printed Canada ...