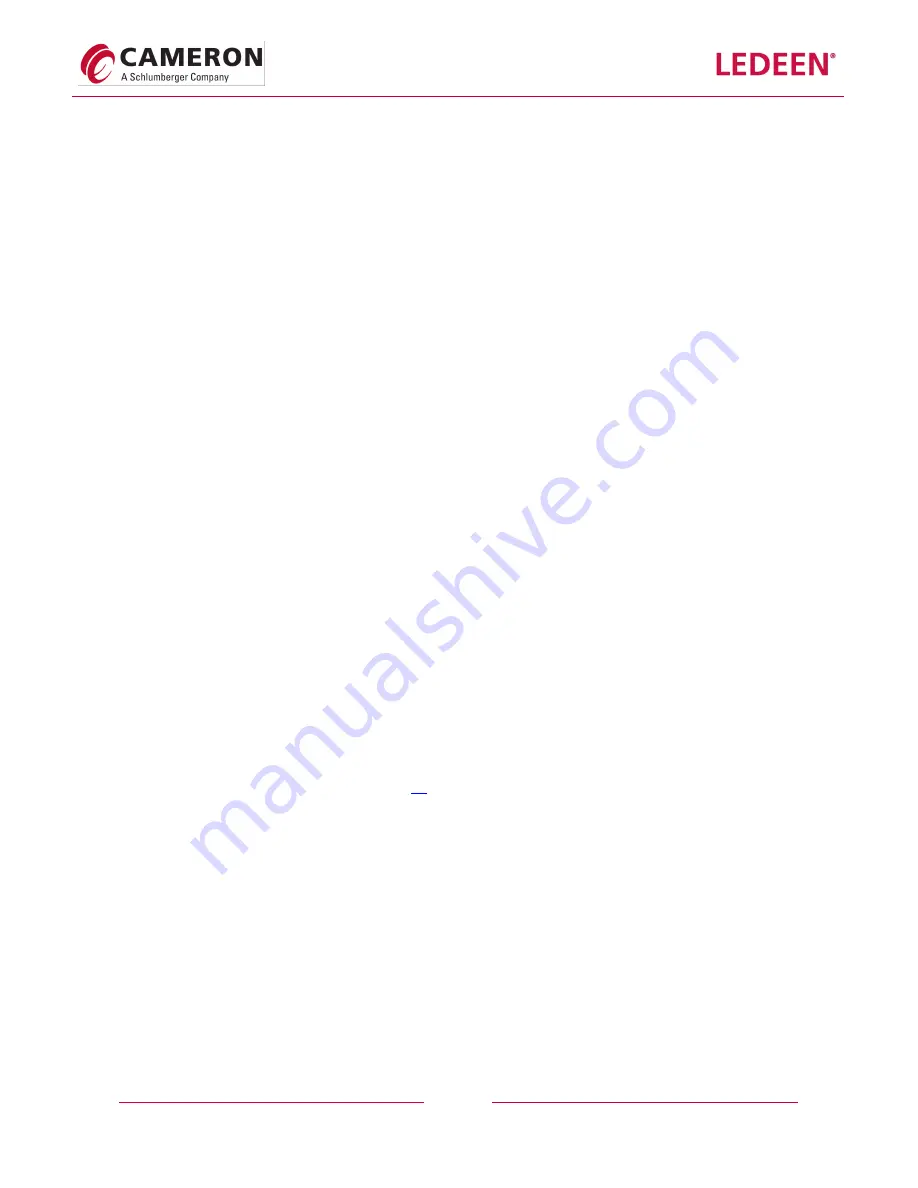
37
1.
Remove the Circlip (item 54) from the integrated head flange on frame
( If VA0 models )
2.
Remove the bushing (item 11) from the integrated head flange on frame
( If VA0 models )
3.
If desired, remove the external seal (item 39) and internal seal (item 26) from the integrated head
flange
(If VA0 models )
4.
Pull the piston rod (item 5) through the frame bore until the pin (item 13) is accessible.
5.
Rotate the piston rod in order to remove the two circlip’s (item 14) from the pin by using a proper circlip
tool..
6.
Remove the sliding blocks (item 12) mounted on the piston rod.
7.
Remove the pin from the piston rod and place the parts of table away from the frame.
8.
Remove the piston rod (item 5) from frame by pulling it away through the bore of the frame.
9.
If desired remove the screw (item 4) from the piston rod by unthreading it.
10.
If desired remove the seal (item 29) from the piston rod.
11.
Unthread the socket head cap screw (item 6) and remove the cover (item 3).
12.
If desired remove the stopper screw (item 1) and nut (item 2) from cover and place the parts on table
away from frame.
13.
Remove plug (item 49) and position the scotch yoke to access the pin (item 18). Then remove it from
scotch yoke using a punch through hole in the frame where plug (item 49) was removed. It can be easy
by hitting it with a hammer.
14.
Remove the Circlip’s (item 15) and careful removal of seals (item 48) from both sides of the shaft (item
9) then remove the shaft from frame.
15.
Remove the scotch yoke (item 17) from the frame.
16.
Remove the bronze bushing (item 16) and careful removal of seals (item 47)
17.
Disassembly of the actuator is now complete.
B.
Reassembly:
a.
Frame sub assembly
(Refer the page
36
for frame exploded view)
Note
: With the actuator fully disassembled into its component parts, each part should be thoroughly cleaned
and inspected. Any parts damaged or worn out should be replaced. It is recommended as a minimum
to replace all sealing components, and to replace the internal components if any damage or erosion
is present.
Note
: Ensure that all parts and all necessary tools are available and are clean. Ensure the
cleanliness of the work bench.
Note
: During seal assembling, remove dust from the groove and apply grease.
Note
: If the actuator is VA0 model, the cylinder head flange (item 25) is integrated with frame.
1.
Place the actuator frame (item 10) on a suitable work bench in horizontal orientation resting on its base.
2.
Locate the two seals (item 47). Place the seals careful into the top and bottom bushings (item 16) and
insert into frame.
Summary of Contents for CAMERON LEDEEN VA Series
Page 4: ...3 NOTES ...
Page 14: ...13 LIFTING DEVICES MAXIMUM WORKLOAD Chains ...
Page 15: ...14 LIFTING DEVICES MAXIMUM WORKLOAD Slings ...
Page 16: ...15 ...
Page 17: ...16 ...
Page 27: ...26 Figure 1 VA0 MODEL HEAD FLANGE INTEGRATED WITH FRAME Figure 2 ...