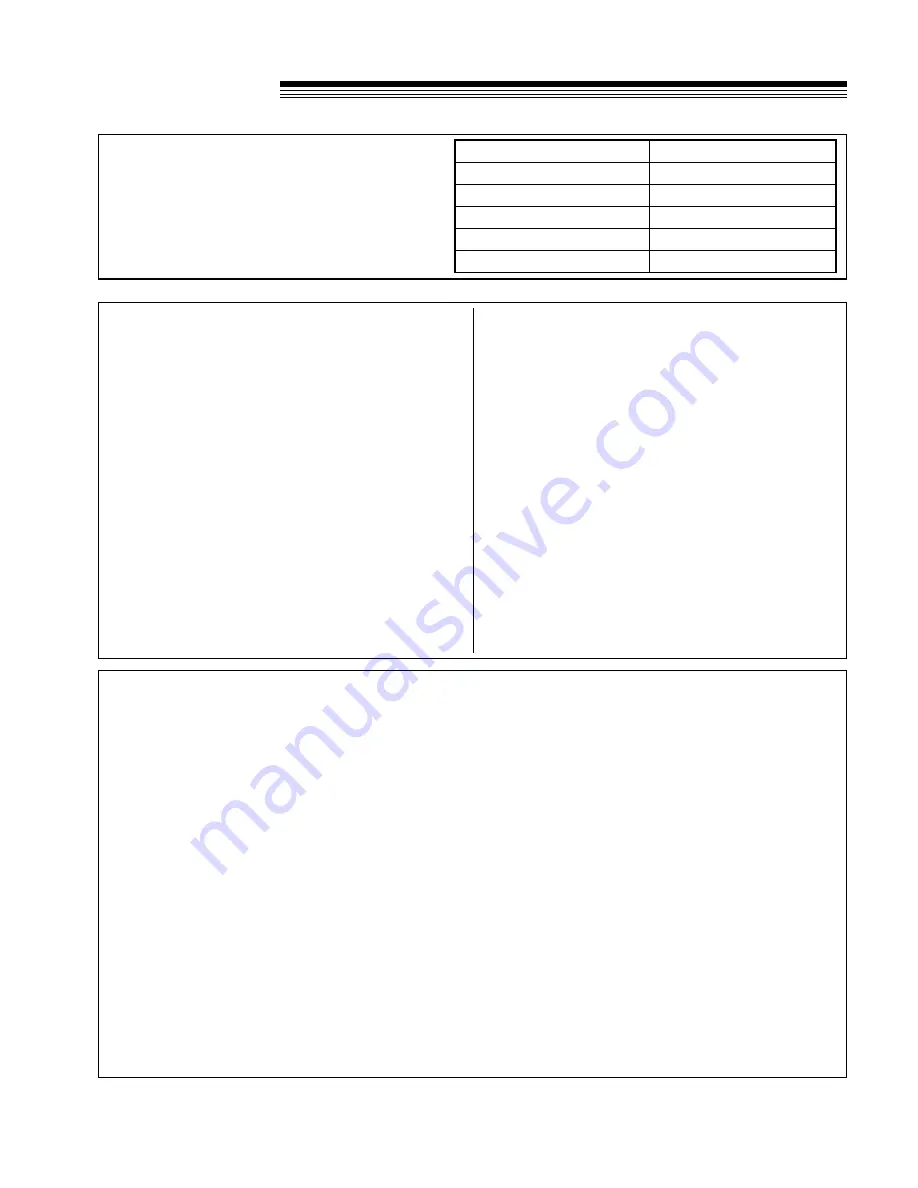
29
XRZ PRO RS
SPECIFIC TORQUES
E
D
A
L
m
N
95
(
S
B
L
-
T
F
70
S
T
U
N
B
U
H
L
E
E
H
m
N
3
0
2
(
S
B
L
-
T
F
0
5
1
T
L
O
B
T
F
A
H
S
K
N
A
R
C
E
N
I
G
N
m
N
8
6
(
S
B
L
-
T
F
0
5
T
U
N
Y
E
L
L
U
P
E
L
X
A
S
N
A
R
T
)
m
N
6
5
-
8
3
(
S
B
L
-
T
F
6
.
1
4
-
3
.
8
2
G
U
L
P
N
I
A
R
D
E
L
X
A
S
N
A
TR
m
N
7
2
-
0
2
(
S
B
L
-
T
F
0
2
-
5
1
R
E
T
L
I
F
E
L
X
A
S
N
A
R
T
)
m
N
9
.
6
1
-
6
.
4
1
(
s
b
l-
n
i
0
5
1
-
0
3
1
)
E
)
)
)
W
B
S
T
U
N
MAINTENANCE
PURGING TRANSAXLES
Due to the effects air has on efficiency in hydrostatic
drive applications, it is critical that it be purged from
the system.
These purge procedures should be implemented any
time a hydrostatic system has been opened to fa-
cilitate maintenance or any additional fluid has been
added to the system.
Purging may be required if the unit shows any of the
following symptoms:
- Noisy operation.
- Lack of power or drive after short term use.
- High operation temperature, excessive oil
expansion.
1. Check the transaxle fluid, fill to proper level, if
required.
2. Raise the drive wheels off the ground. Support
unit with jackstands or other suitable means.
3. With the bypass valves open, and the engine
running, slowly move the control levers in both
forward and reverse directions 5 to 6 times. As
air is purged from the unit, the oil level will drop.
4. With the bypass valve closed, and the engine
running, slowly move the control levers in both
forward and reverse directions 5 to 6 times.
5. Stop engine. Check the transaxle fluid level, add
fluid as required.
6. It may be necessary to repeat steps 3-5 until all
the air is completely purged from the system.
When the transaxle moves forward and reverse
at normal speed, purging is complete.
CLEANING MACHINE
Clean the machine after use. The machine will run
cooler and last longer if kept free of clippings and
other debris. A clean machine also reduces the risk
of fire due to accumulation of combustible debris and
chaff
Brush or blow clippings and debris off the cutterdeck
and engine deck.
WASHING MACHINE
CAUTION: Improperly washing a machine can cause
water to enter bearings and other components. This
can greatly reduce component life.
– Do not use a pressure washer. Do not direct
water at bearings or seals. High pressure water
can blow past seals and enter seal bearings.
– Allow the machine to cool down before washing.
Water on a warm machine can be sucked into
sealed bearings as they cool.
– Avoid getting electrical connections wet. Water
can cause electrical faults and corrosion of elec-
trical components.