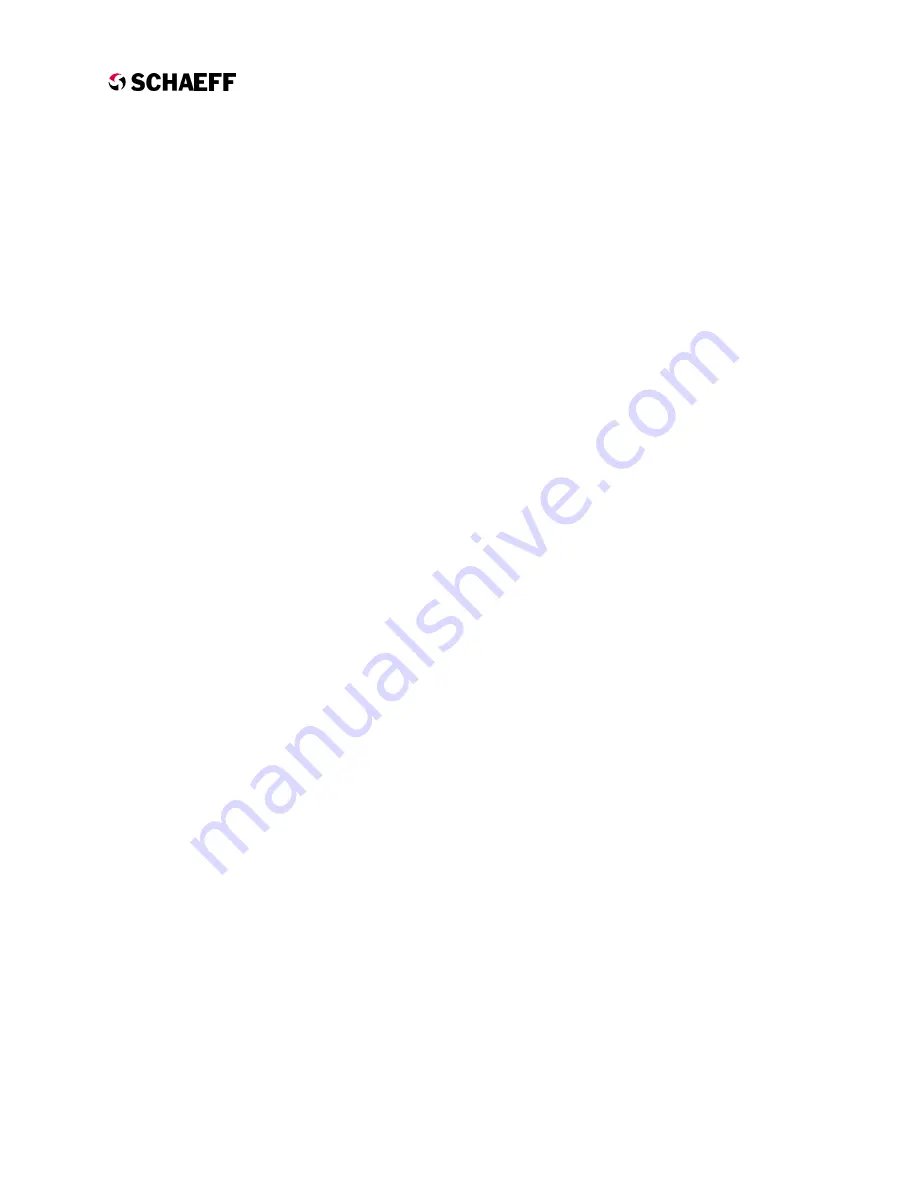
3.
Install the hydraulic hoses in the correct
locations.
4.
Install the steering tiller.
5.
Connect the battery.
6.
Check the operation of the steering system.
7.
Check all hydraulic connections for leaks.
8.
Disconnect the battery and remove the
steering tiller.
9.
Install the left hip pad in the operator
compartment.
10. Install the control cover and the top cover.
11. Connect the battery.
Hydraulic Motor
Removal
1.
Disconnect the battery and discharge the
capacitors.
2.
Remove the top cover.
3.
Remove the steer position potentiometer
(refer to STEER POSITION
POTENTIOMETER Removal procedure in
this section).
NOTE
The hydraulic lines must be removed before
removing the mounting screws from the
hydraulic motor. Hoses should be labeled to
help install them correctly.
4.
Remove the hex screws securing the
mounting bracket.
5.
Remove the hydraulic motor mounting plate
by threading two 3/8" x 3" screws through the
threaded holes (Item 1 in Fig. 4.1).
Alternately tighten the screws until the
mounting plate is free.
6.
Loosen the lock nut from the hydraulic motor
shaft. Use tool P/N 9650029 to hold the
pinion gear.
7.
Remove the screws securing the hydraulic
motor to the mounting bracket.
8.
The motor shaft is tapered. Use a suitable
puller to remove the pinion gear from the
shaft utilizing the mounting bracket as part of
the puller.
Replacement
1.
Install the hydraulic motor onto the mounting
bracket, making sure to use the correct length
screws. Longer screws may crack the motor
case.
2.
Install the steer pinion gear onto the hydraulic
motor shaft. Use tool P/N 9650029 to hold
the pinion gear and torque the nut to 115 lb-ft.
Install a cotter pin.
3.
Lower the hydraulic motor and bracket into
position and align the mounting holes with the
studs.
4.
Install the mounting screws until finger tight.
Gradually tighten the mounting screws in an
alternating pattern. Torque to 23 lb-ft.
5.
Install the steer position potentiometer (refer
to STEER POSITION POTENTIOMETER
Replacement procedure in this section).
6.
Install the hydraulic hoses in the correct
locations.
7.
Connect the battery and test the steering
system for proper operation. Inspect all of the
hydraulic hoses and fittings for leaks.
8.
Install the top cover.
Steer Gear
Removal
1.
Disconnect the battery and discharge the
capacitors.
2.
Remove the top cover and the control cover
(it is not necessary to remove the tiller for this
procedure).
3.
Remove the steer control valve bracket
screws and move it aside. Remove the
hydraulic motor and steer position
potentiometer. It is not necessary to remove
the hydraulic hoses.
4.
Remove the lock nut securing the steering
gear to the steer fork assembly.
5.
Lift the steering gear off the steer fork shaft
and out of the truck.
Replacement
1.
Before installing the steering gear, make sure
the steer fork is properly positioned with the
stop pin toward the forks.
E
lectric
C
ounterbalance
H
igh
O
utput
Steering
REV W1 11/02/99
4.3