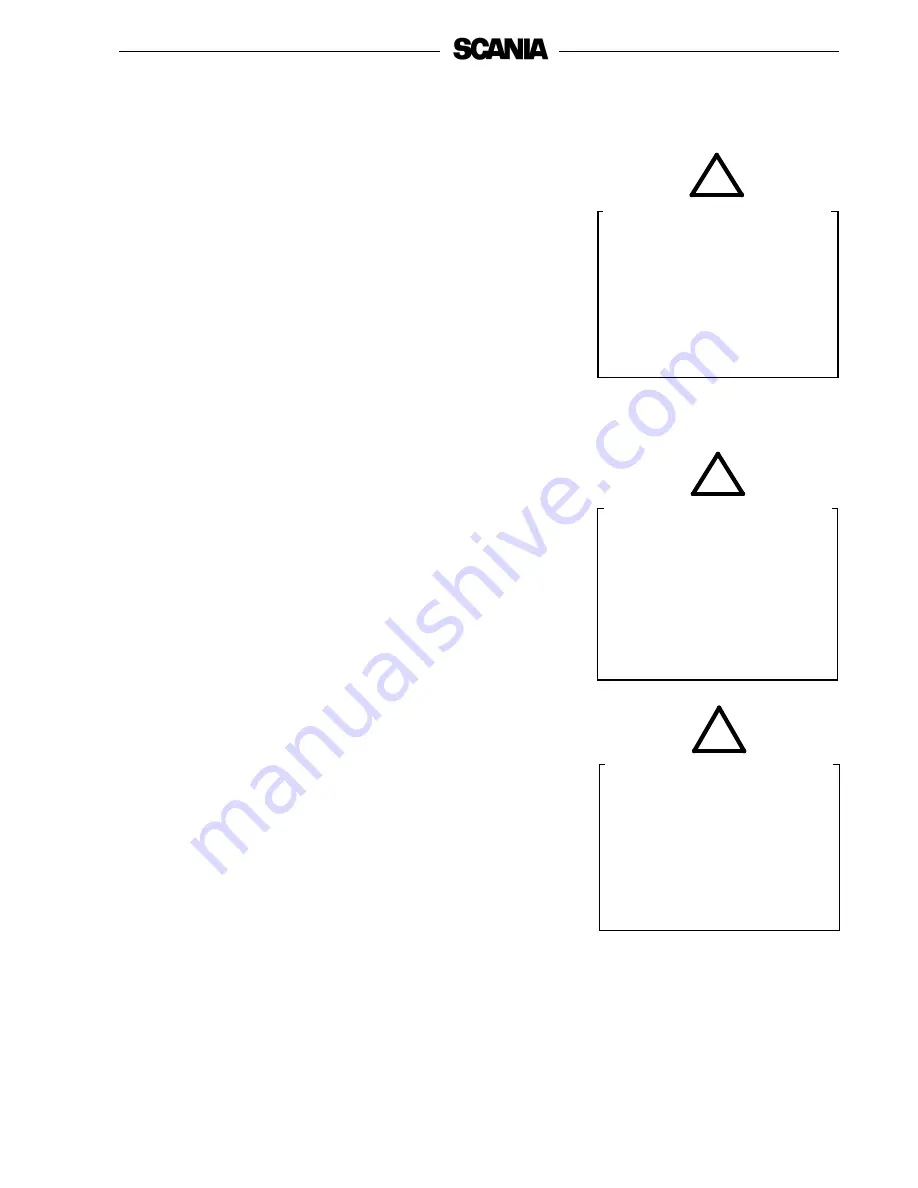
© Scania CV 2011
19
12. Checking the fuel level, see page 42.
14. Checking the electrolyte level in batteries, see page 44.
15. Checking the state of charge in batteries, see page 44.
18. Checking the drive belt tension, see page 46.
Checks before running
Before running, "Daily maintenance" as described in the inspection schedule
should be carried out, see page 25.
Starting the engine
If the fuel tank has been run dry or if the engine has not been used for a long
time, bleed the fuel system.
Out of consideration for our common environment, your Scania engine has
been designed to use less fuel when starting. Using unnecessarily large
amounts of fuel when starting the engine always results in emissions of
unburnt fuel.
- Open the inlet valve for the sea water system (if fitted).
- Open the fuel cock if fitted.
- Disengage the engine.
- Engines with battery master switch: Switch on the power by means of
the battery master switch.
- Start the engine with the key in the control panel (SCP) or the start
button (only from RCB).
-
S6
: The diagnostics lamp should go out after approximately 2 seconds
when starting.
Block the starting device when
working on the engine.
If the engine starts
unexpectedly, there is a
SERIOUS RISK OF INJURY.
Only start the engine in a well
ventilated area.
If it is run in an enclosed space,
there should be an effective
device to draw off exhaust gases
and crankcase gases.
Never use starter spray or
similar agents to help start the
engine.
An explosion may occur in the
intake manifold with a risk of
personal injury.
WARNING
!
WARNING
!
WARNING
!