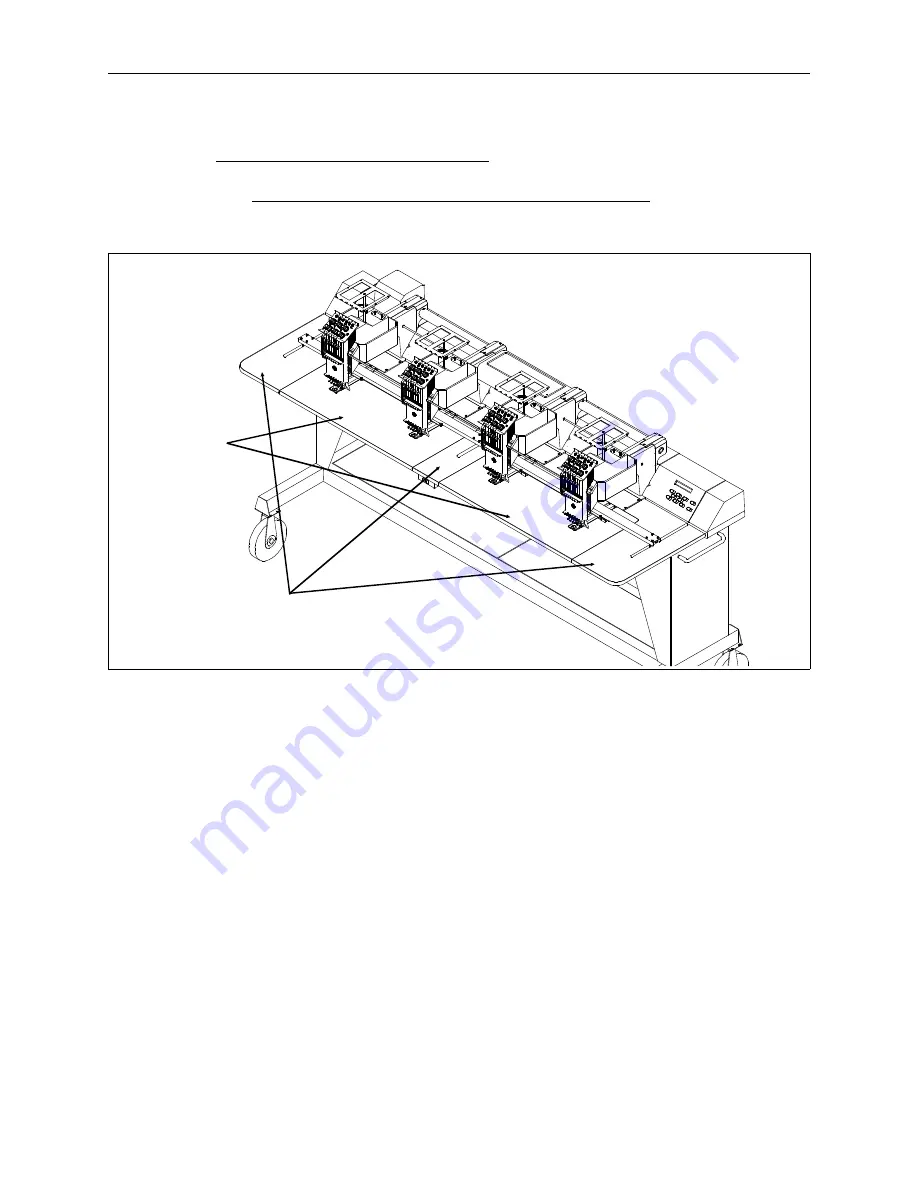
Removing the Table Tops
EMC 6/4, 6/4M, 6/4MT, EMC 10/4, EMC 10/4T:
Remove the table top inserts in the order shown in Figure 1-4.
Use a small brush or can of compressed air to clean any dust or accumulated
lint from underneath the table tops themselves. Look for any foreign objects
(scissors, pens, needles, etc.) that may have fallen inside the channels.
Remove these
sections first
Remove these
sections second
Figure 1-4
1-6
Exterior Surfaces
Basic Maintenance
Melco Embroidery Systems