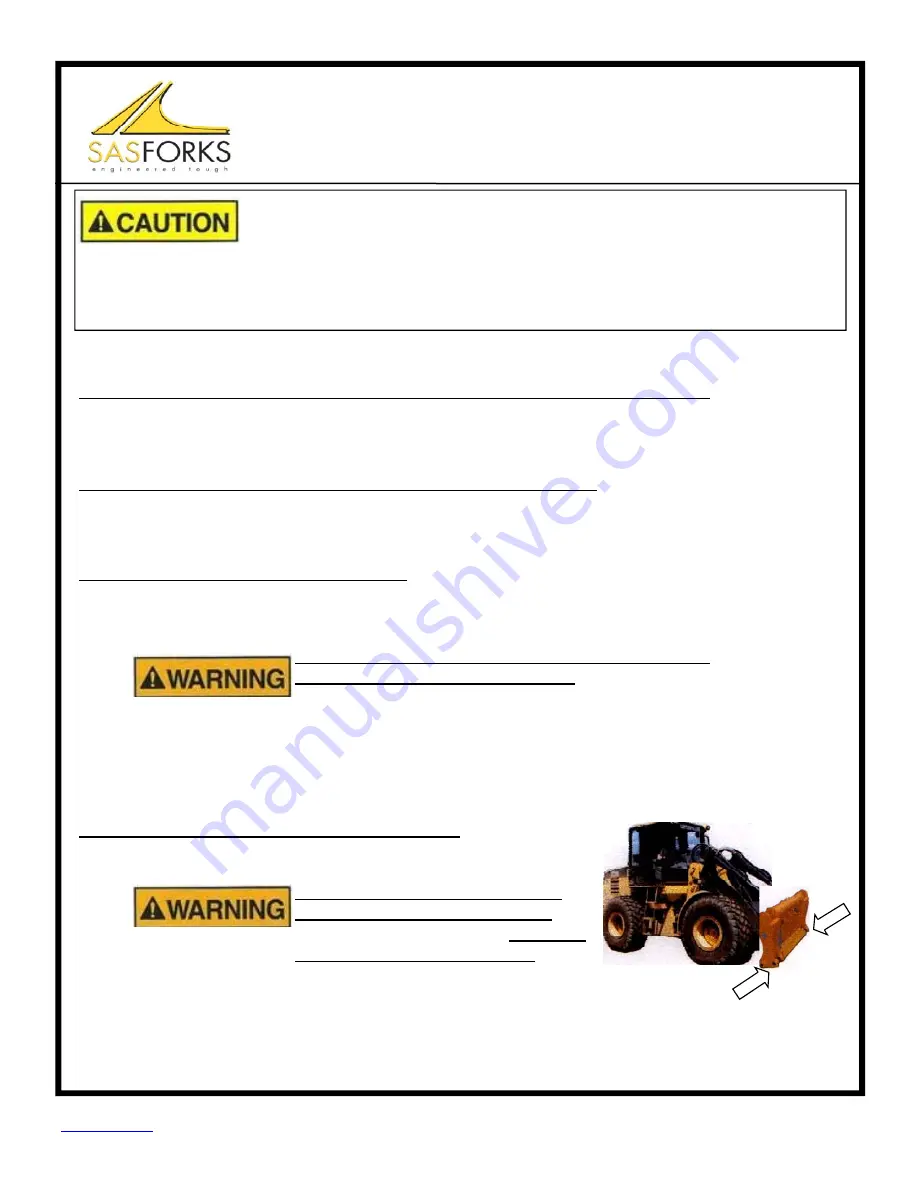
Opera ons/Procedures/Forks/CAR BODY SAS FORKS Manual v2.pub 2/13/13 2/16/2013 2:50 PM
Page 5
www.sasforks.com
© 1995
‐
2013 S.A.S. of Luxemburg, Ltd. 1
‐
877
‐
SAS
‐
FORK
WHEEL LOADER RECOMMENDATIONS:
REMOVE YOUR “AUTOMATIC DUMP” FEATURE ON YOUR BUCKET LEVER.
The automatic dump feature was originally intended for loaders moving gravel in buckets and sub-
sequently dumping it into trucks. This is not a desired feature when moving vehicles with SAS
FORKS™. Have this automatic dump mechanism removed if your machine has one.
REMOVE YOUR “LOCK POSITION” AND “DETENT’ CONTROLS
Remove the lock position and detent controls on the up and down levers. These controls, if left
operable on your machine, could cause accidents by raising or lowering the load without the
operator being aware that the lever is engaged.
DIRECT
PIN MOUNT
TYPE SAS FORKS:
• Park wheel loader on firm level ground, • Set parking brake • Set attachment flat on ground
• Turn off wheel loader engine • Depressurize the wheel loader’s hydraulic system to release any
residual pressure and resulting tension on the wheel loader arms.
Failure to properly release residual hydraulic system
pressure may result in stored energy
and undesired or unexpected
movement
of
wheel
loader arms when pins are removed.
Grease holes using a brush. Do not insert finger into pin hole opening, as there is a risk of a
pinch point and finger being severed.• Align holes on SAS Fork carriage with wheel loader
arm holes. • Grease pins • Insert pins & secure properly.• Start wheel loader and slowly move
attachment, while carefully watching for interference points. If any are found, “stops” may
need to be installed. Contact SAS Forks to discuss.
QUICK COUPLER MOUNT
TYPE SAS FORKS:
• Align SAS Forks squarely to coupler & engage locking pins.
Locking pins must be fully engaged and secure prior to use.
Failure to properly secure coupler
locking pins will result in damage
to
the forks and the coupler and
forks may
fall off the coupler & drop load
, risking
damage to the load and injury or death
to
anyone
in
the
area.
INSTALLATION GUIDELINES (Page 5)
SAS™ FORKS
S.A.S. of Luxemburg,Ltd. 133 Center Drive Hwy 54, PO Box 260, Luxemburg, WI 54217 USA
Phone: 920-845-2198
1-877-SAS-FORK
Fax: 920-845-2309
Web: www.sasforks.com
Installation of SAS FORKS™ should be completed by a professional knowledge-
able on your machine. The SAS FORKS™ were made specifically to fit the at-
tachment of your machine. Contact your wheel loader or forklift manufacturer, as
you deem necessary, depending on applicable rules or regulations, to obtain guidance or approval as may
be required prior to installation of this attachment. Avoid pinch points during installation as you may be
injured. Improper installation may cause damage to the loader.