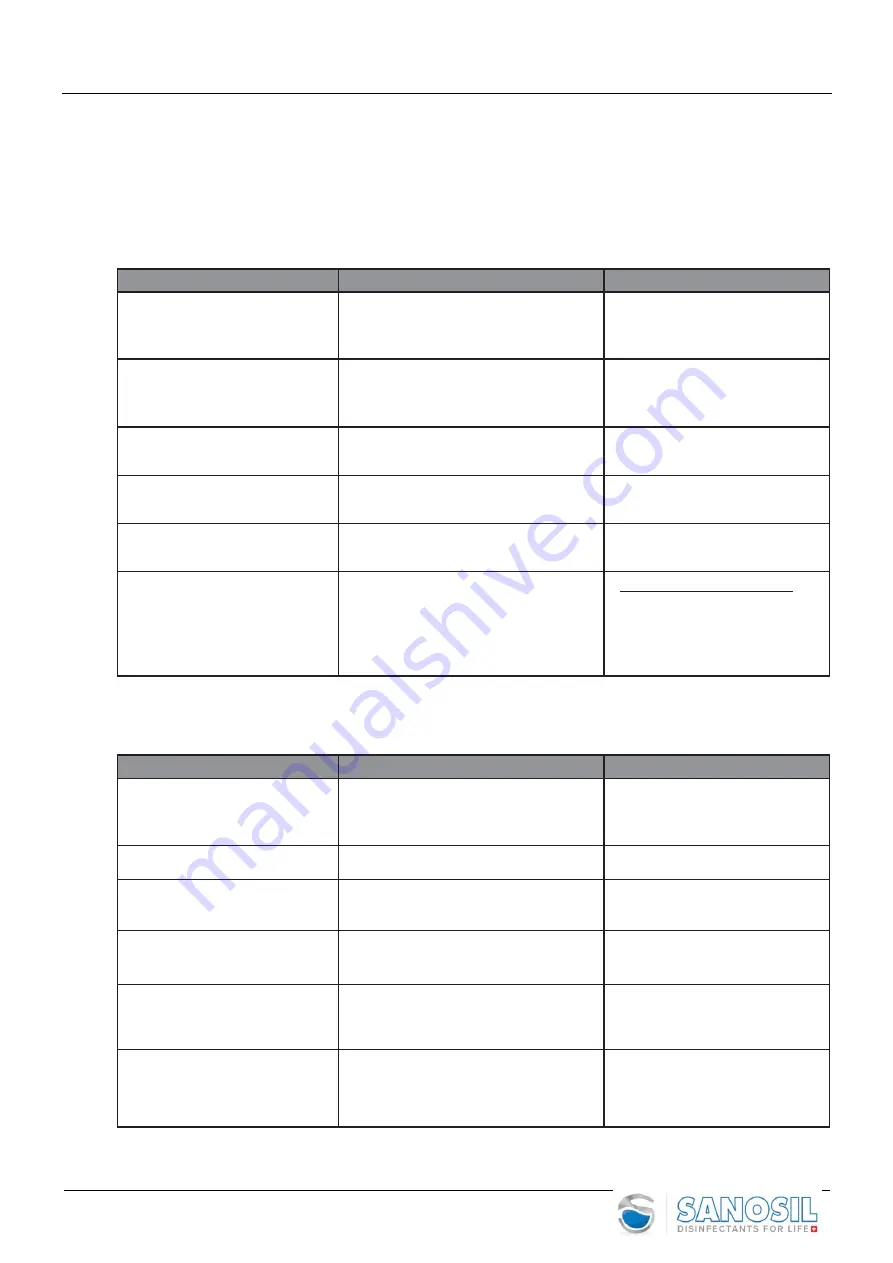
Sanosil Q-Jet Advanced
25
7. Troubleshooting
To determine and search for anomalies it is essential to have this Operation and Maintenance Manual at hand.
7.1 Table
Anomaly
Possible Cause
Remedy
Device does not work / does not
respond
•
Check power supply
•
Check fuses
•
Check correct insertion of cable
•
Ensure power supply to device
Fan does not work
•
Thermal motor sensor stops engine
(too high engine temperature)
•
Air-intake filter too dirty
•
Check engine, switch off and on
•
Set-up device once more
•
Clean or change filter
Liquid is not sprayed
•
Tank is empty
•
Nozzle is clogged
•
Fill liquid
•
Remove obstruction
Device does not start or stops
before finishing program
•
Cycle has been terminated abnormally
(e.g. power cuts)
•
Switch off and on again
•
Set-up device once more
Device emits loud noises
•
Possible internal damages
•
Presence of foreign bodies in the fan
•
Switch off and unplug device, call
service technician
Device leaks liquid
•
Possible internal damages
•
Internal piping rupture or connections
leaking
•
Device was tipped on its side without
completely empty.
•
Switch off and unplug device,
open device and remove water.
Let device completely dry. If
device still leaks call service
technician
7.2 Warning on Display
Warning
Possible Cause
Remedy
LIQUID LEVEL
•
Liquid level monitor determines
too low liquid level. Device stops
(LED flashes).
•
Fill liquid
•
Set-up device once more and start
again
FUSE DEFECT
•
Fuse blown / defect
•
Check / change fuse on print plate
CYCLE INTERRUPTED
•
Automatic cycle has been
interrupted early
•
Switch off and on again
•
Set-up device once more
!!! SERVICE !!!
•
Maximal running time since last
Service has been reached or exceeded
•
Switch off and unplug device, call
service technician
TIMER NOT OK
•
System is in automatic mode but
Timer is not set or activated
•
Check Timer’s
settings
MAX. TIME EXCEEDED
•
Inputted volume (m
3
) and/or
concentration (ml) are too high,
hence calculated time exceeds
device’s
capacities.
•
Check and adapt settings