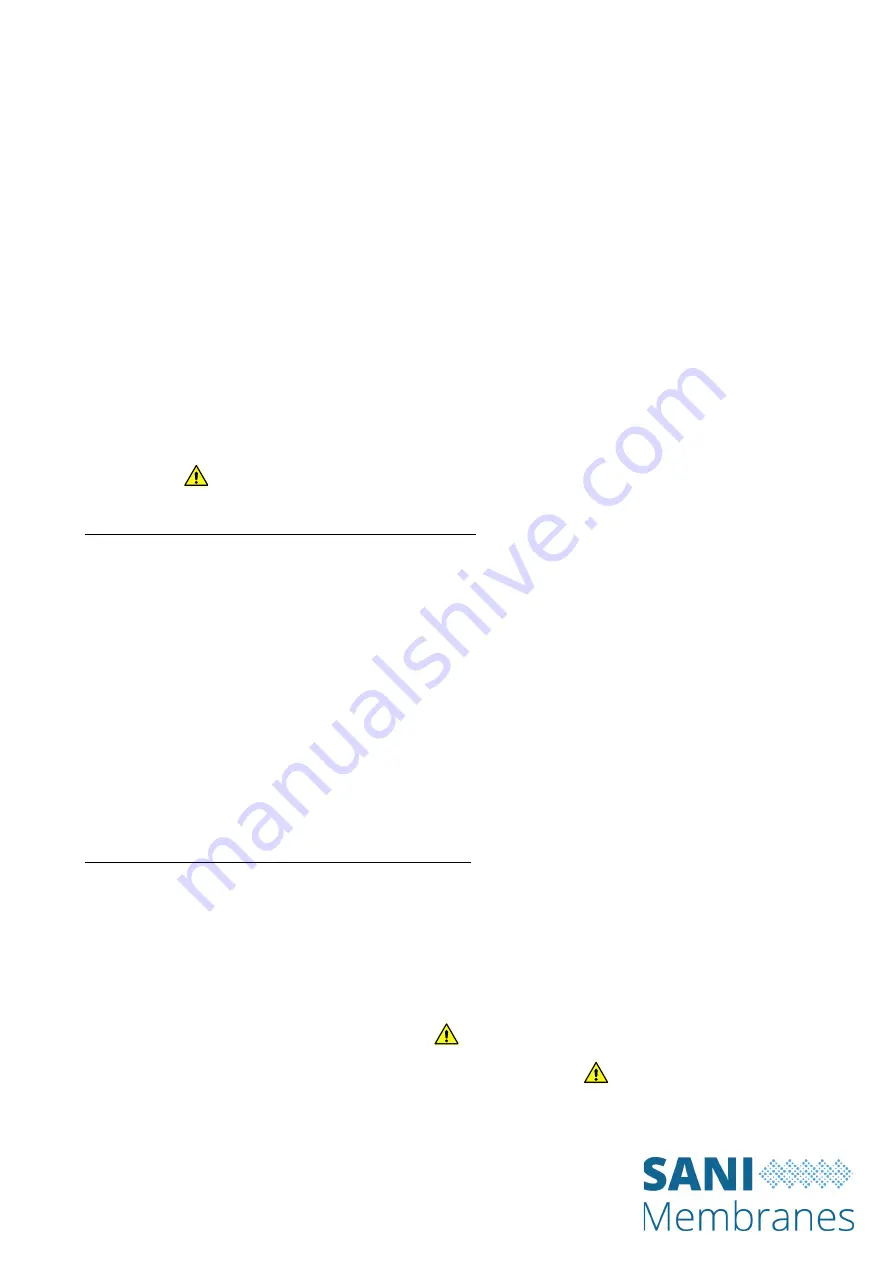
22
Version: 20221219
•
Maintain a minimum retentate flow out of each cartridge to avoid dead-end type
filtration. A suitable retentate flow is normally 800
–
1200 L/h per cartridge (so that
means 3.2
–
4.8 m³/h for a 40 or 80 m² plant). This is application dependent and if the
media is highly concentrated or very viscous the flow rates may need to be higher.
•
If a lower retentate flow is required or desired a mix flow within each unit can be
established to ensure the above mentioned retentate flows. This is relevant if running
the unit as a continuous single pass concentration step.
•
When performing microfiltration of media with high solids load, the mix flow and
vibration must be initiated as soon as the unit is filled to avoid severe fouling
•
Operating Pressure: 0-4 bar(g) at 5-35 °C, 0-3 bar(g) at 5-55 °C and 0-1 bar(g) at up to
80 °C
WARNING
Microfiltration (transmembrane pressure 0
–
1 bar)
•
Keeping a very low trans membrane pressure between 0.05 to 0.25 bar often gives the
best long-time results. The optimum is membrane and product dependent.
•
The initial flux can be very high and easily result in severely fouled areas in the Vibro-I
unit. Reduce the flux by lowering the trans membrane pressure and let more retentate
out to avoid severe fouling.
•
Consider to use a positive displacement pump to control the permeate rate instead of
controlling pressure. It can be very difficult to control at the very low pressures
required for some microfiltration processes.
Ultrafiltration (transmembrane pressure 1
–
4 bar)
•
Ultrafiltration is less sensitive to pressure variation. Optimum transmembrane
pressure is often lower than often seen in traditional cross flow systems. Typically, the
ideal transmembrane pressure is between 1
–
2 bar.
•
Make sure that the system pressure does not exceed 4 bar(g)
–
with a 4 bar(g) safety
valve or a 4 bar(g) software hard stop.
WARNING
Operating Pressure: 0-4 bar(g) at
5-35 °C, 0-3 bar(g) at 5-55 °C and 0-1 bar(g) at up to 80 °C.
WARNING