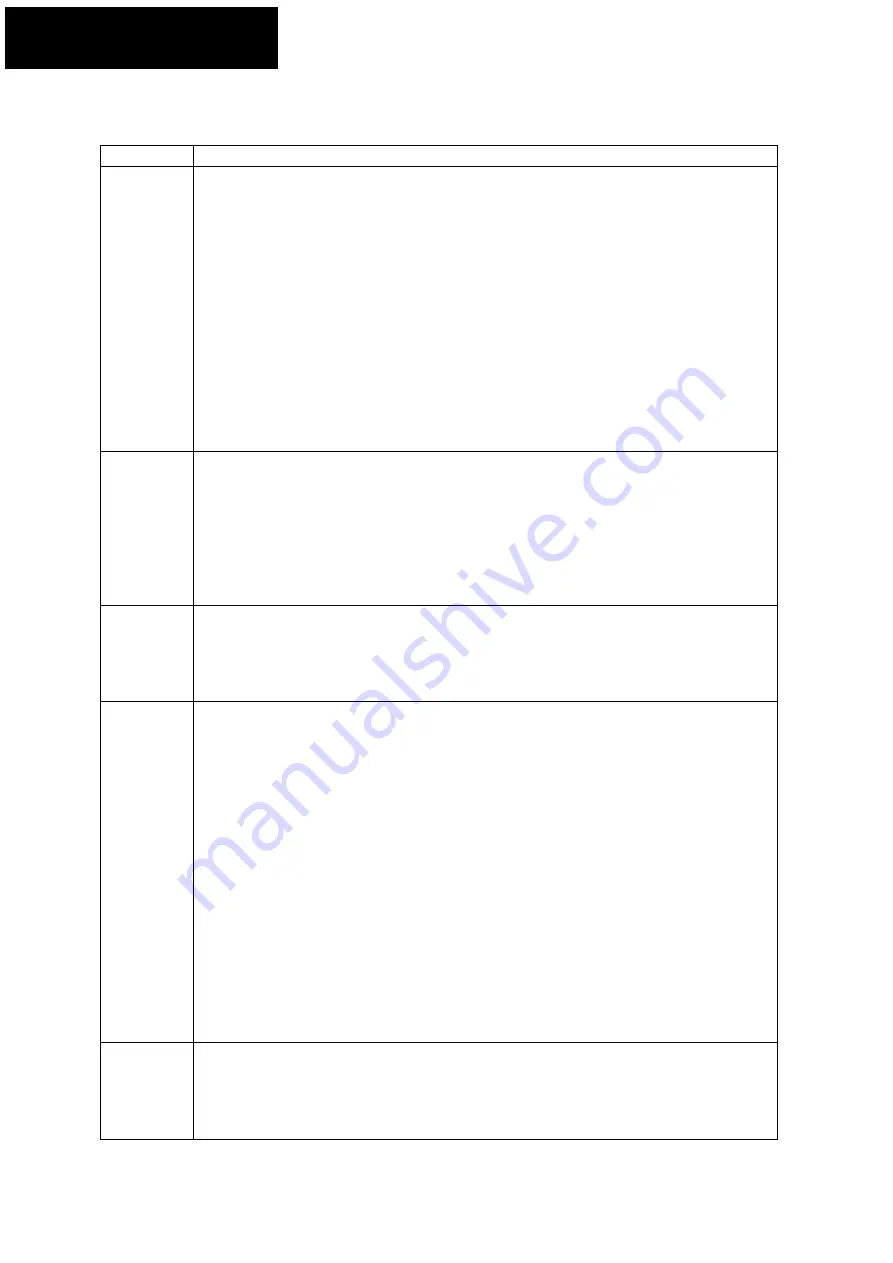
P a g e
|
56
Optidrive E3 Set-up Guide
19
Trip Codes & Fault Finding
Fault Finding
Fault Code
Possible cause and corrective actions
O
OO
O-
--
-1
11
1
Drive software instantaneous over current trip.
•
Usually caused by accelerating or decelerating the motor/load too quickly or by shock
loads on the motor/load.
•
Check motor star/delta connection correct for drive output voltage.
•
Check motor not seized and motor brake is releasing (if used).
•
Make sure motor brake is not connected to drives output.
•
Incorrect drive set up.
Check motor nameplate parameters P-07, P-08 & P-09 are
correct for the motor.
•
Check torque boost setting in P-11 and reduce if necessary.
•
If an autotune has been carried out and then the motor and/or motor cable has been
changed, re-autotune the drive to the motor.
•
Check correct setting of Motor Control Mode P-51.
•
If multi-motor application or motor choke fitted, make sure P-51 = 1 (V/f mode).
•
Check connections between inverter output and motor for loose connections etc.
•
Disconnect motor to check that drive runs without motor connected.
h
hh
hO
OO
O-
--
-1
11
1
Drive hardware instantaneous over current trip.
•
Usually caused by a phase to phase or phase to earth fault on the drive output.
•
Check motor cable and motor for faults.
•
Disconnect motor to check that drive runs without motor connected.
•
Make sure motor brake is not connected to drives output.
•
Check connections between inverter output and motor for loose connections etc.
•
See information for
O
OO
O-
--
-1
11
1
trip.
NOTE:
O-I and hO-I trips cannot be reset for at least 4s after a trip occurs
O
OO
OV
VV
VT
TT
T-
--
-F
FF
F
Drive output fault.
•
Can indicate a possible phase to earth fault on motor/motor cable.
•
Can indicate an output power stage internal fault within the drive.
•
Remove motor cables from drive, power down and back up to see if fault clears. If fault
remains, contact the supplier of your drive.
1
11
1
.
T
TT
T-
--
-T
TT
TR
RR
RP
PP
P
Motor thermal overload trip.
•
The drive has tripped after delivering >100% of the value in P-08 for a period of time to
prevent damage to the motor.
•
Load to large for motor/drive rating. Check actual motor current and compare to setting
of P-08.
•
Check motor star/delta connection is correct for drive output voltage.
•
Check motor not seized and motor brake releasing (if used).
•
Incorrect drive set up.
Check motor nameplate parameters P-07, P-08 & P-09 are
correct for the motor. (Check P-09 is correct if high frequency/speed motor)
•
Increase acceleration and deceleration ramps in P-03 and P-04.
•
Check torque boost setting in P-11 and reduce if necessary.
•
If an autotune has been carried out and then the motor and/or motor cable has been
changed, re-autotune the drive to the motor.
•
Check correct setting of Motor Control Mode P-51.
•
Check setting of P-54 – Current limit.
•
If multi-motor application or motor choke fitted, make sure P-51 = 1 (V/f mode).
•
If P-13 has been set to fan or pump mode, is application a variable torque load? Check
application characteristics. Possibly set P-13=0, constant torque load.
0
00
0-
--
-U
UU
Uo
oo
o1
11
1T
TT
T
Over voltage on drives DC bus.
•
Check mains supply voltage is within tolerance.
•
If trip occurs during deceleration, increase deceleration ramp time in P-04.
•
Install a suitably rated braking resistor to dissipate regenerated energy.
•
Makes sure braking resistor function is enabled in P-34.