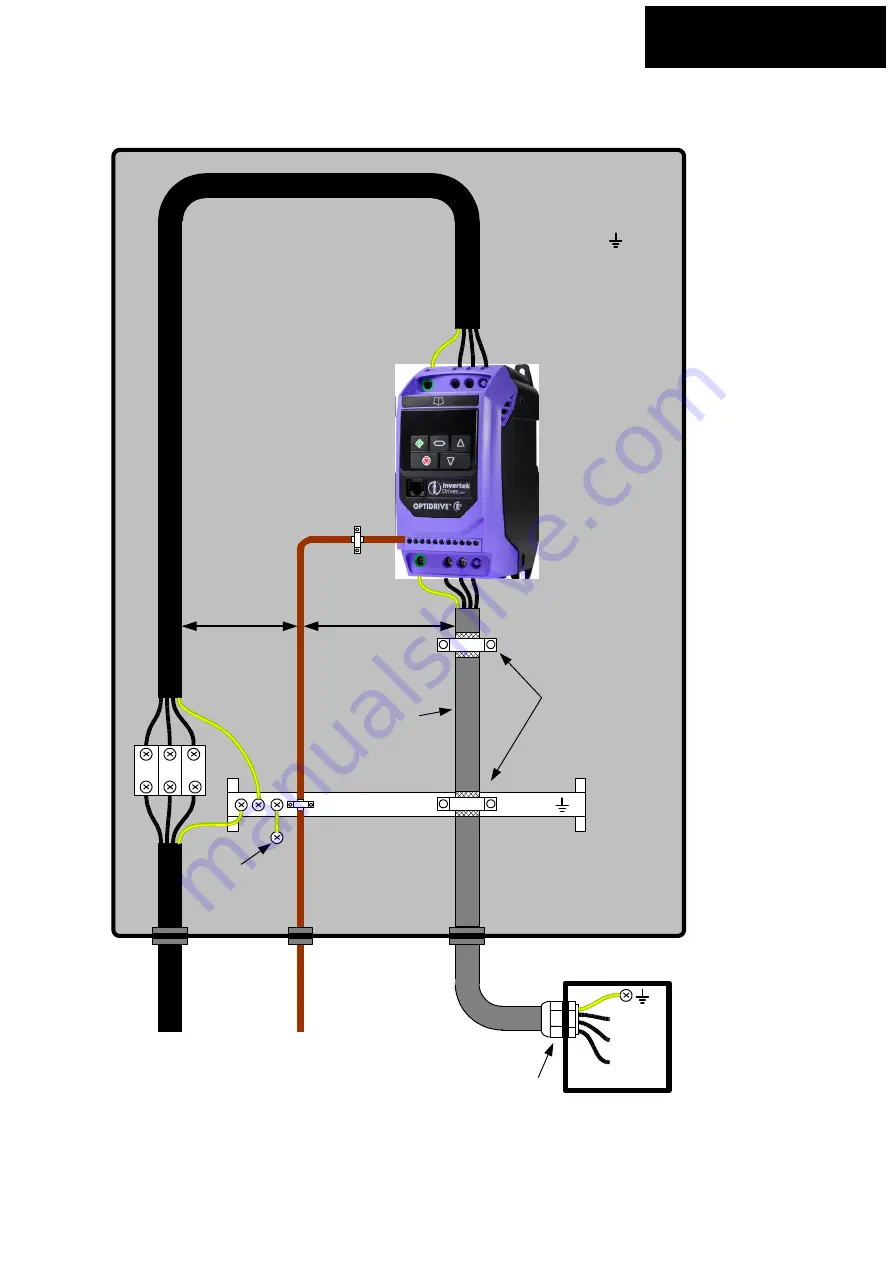
Optidrive E3 Set-up Guide
P a g e
|
17
6
Basic EMC Information
General requirements for good EMC practice
L
1
L
2
L
3
Metal 'EMC' Gland
with cable shield/
screen connected to
gland as per
manufacturers
instructions
U
V
W
Mains Supply
Motor
terminal
box
Main earth busbar
Cable shield
exposed and
360
o
clamp
bonded to
metal backplate
or earth busbar
(Same for
control cables)
Motor Cable
3-phase and earth
shielded/screened
cable. Maintain
shield as far as
possible along cable
Control Cables
Twisted pair
shielded cables for
analogue signals
>100mm
>100mm
Panel mounting
backplate with
conductive
surface
Metal backplate
bonded to main
earth busbar