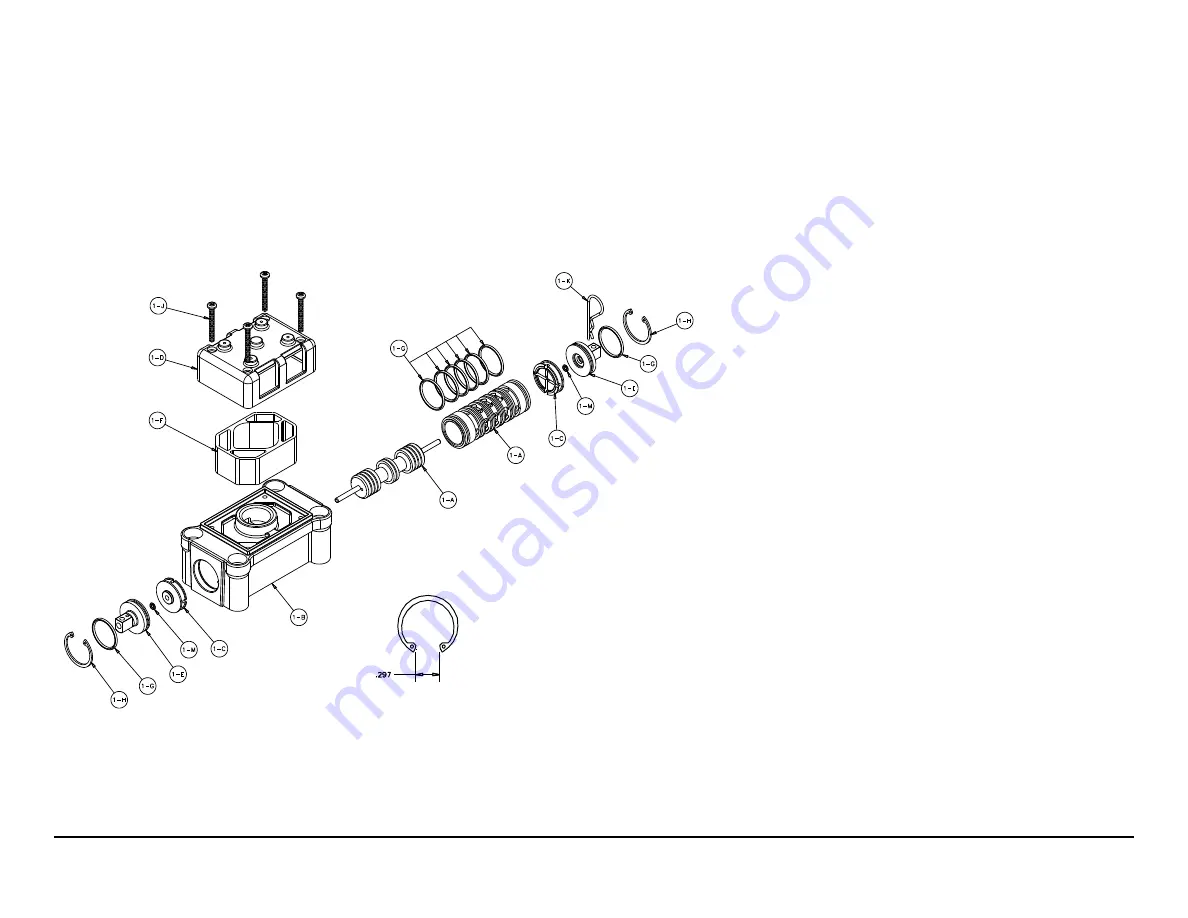
s30nmdl2sm-rev0614
Model S30 Non-Metallic Page 21
Air Valve Assembly Drawing with Stroke Indicator Option
S30 Design Level 2
PILOT VALVE ASSEMBLY PARTS LIST
ITEM PART NUMBER
DESCRIPTION
QTY
1
031-146-000
Air Valve Assembly
1
1-A
031-143-000
Sleeve and Spool Set w/Pins 1
1-B
095-094-551
Body, Air Valve
1
1-C 132-029-552
Bumper
2
1-D
165-096-551
Cap, Muffler
1
1-E
165-098-147
Cap, End
2
1-F
530-028-550
Muffler
1
1-G 560-020-360
O-Ring
8
1-H
675-044-115
Ring, Retaining
2
1-J
710-015-115
Screw, Self-Tapping
4
1-K
210-008-330
Clip, Safety
1
1-M 560-029-360
O-Ring
2
For Pumps with PTFE Coated Hardware:
1
031-146-002
Air Valve Assembly
1
1-J
710-015-308
Screw, Self Tapping
4
1-H
675-044-308
Ring, Retaining
2
(includes all other items on 031-146-000 above.)
For Pumps with Alternate Mesh, Sound Dampening Mufflers
or Piped Exhaust:
1
031-147-000
Air Valve Assembly
1
(includes all items on 031-146-000 minus 1-D, 1-F, &1-J)
Note: Stroke Indicator is standard on Spill Containment models
NOTE: CHECK GAP AFTER ASSEMBLY
TO INSURE COMPLETE
INSTALLATION OF RETAINING RING
Summary of Contents for S30
Page 2: ......