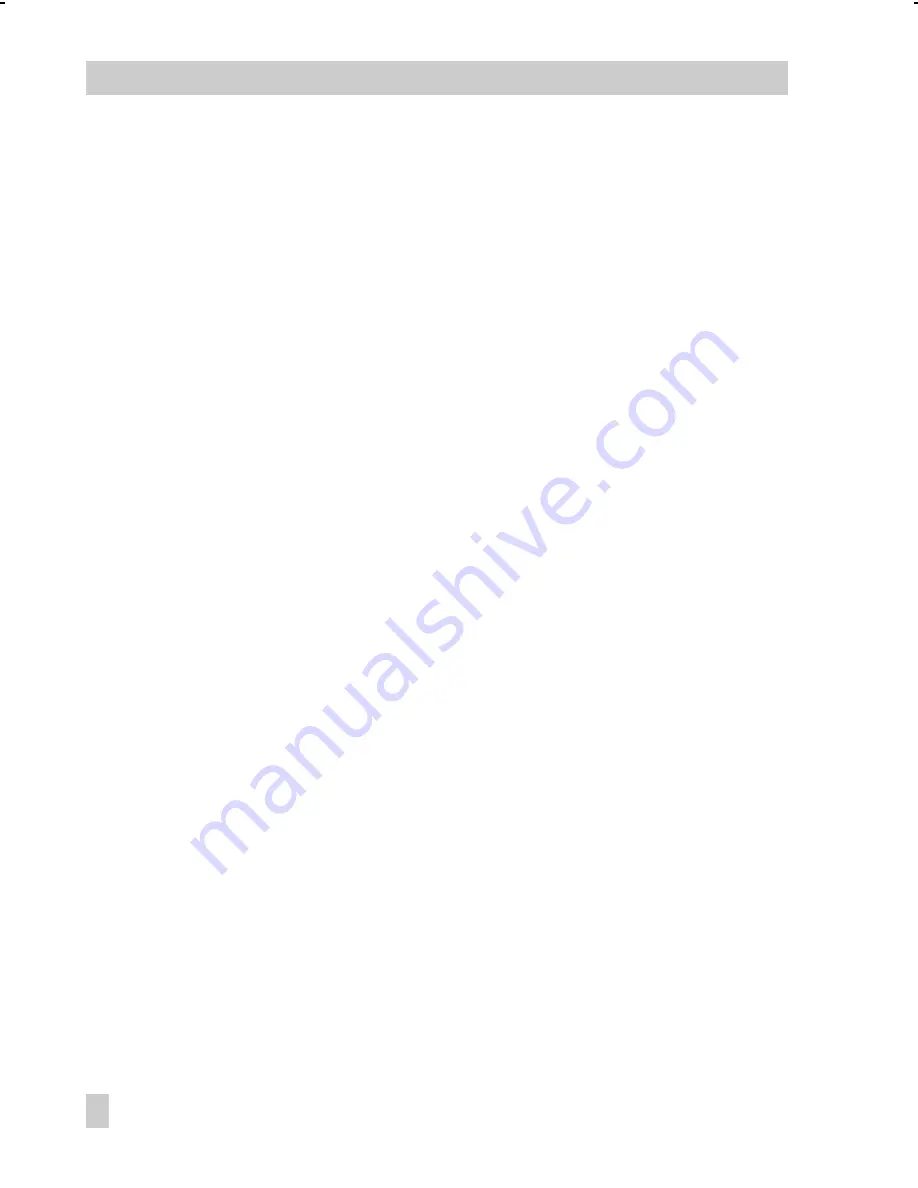
1 Design and principle of operation
The digital positioner compares the refer-
ence variable, which is cyclically trans-
mitted over the FOUNDATION
TM
Fieldbus,
with the travel or opening angle of the con-
trol valve. It then delivers a corresponding
signal pressure. It is suitable for attachment
to linear and rotary actuators.
The Type 3787 Positioner communicates as
per FOUNDATION
TM
Fieldbus specification
with field devices, programmable logic con-
trollers and process management systems.
An integrated PID Function Block allows the
control of required process variables di-
rectly in the field.
The travel of the control valve is picked up
by the inductive displacement sensor (1)
and supplied to the microcontroller (2) via a
converter.
The microcontroller compares the travel
with the reference variable and controls the
two pneumatic 2/2-way on-off valves (3, 4)
when a system deviation occurs. The on-off
valves fill (3) or vent (4) the pneumatic actu-
ator via corresponding amplifiers corre-
sponding to the system deviation.
Two LEDs on the inside of the cover indicate
the operating status of the positioner.
The positioner is equipped with a standard
binary input over which any process infor-
mation can be signaled via the FOUNDA-
TION
TM
Fieldbus.
The write protection switch (6) located on
the inside of the cover prevents stored con-
figuration data from being overwritten.
Forced venting:
The positioner is controlled over a 6 to 24 V
signal which causes the corresponding sig-
nal pressure to be applied to the actuator. If
the voltage signal drops, the signal pressure
is shut off and the actuator is vented. The
control valve moves to its fail-safe position
regardless of the output variable issued by
the microcontroller.
1.1 Optional limit switches
Limit switches can be retrofitted to the stand-
ard positioner.
Two proximity switches can be used for fail-
safe circuits to indicate the valve’s end posi-
tions.
1.2 Communication
The positioner is completely controlled via
digital signal transmission according to the
FOUNDATION
TM
Fieldbus specification
based on the E EN 50170/A1 draft. Data
is transmitted as bit synchronous current
modulation at a transmission rate of
31.25 kbit/s over twisted pairs according
to EN 61158-2.
Configuration with TROVIS-VIEW
The positioner can be configured using the
SAMSON Configuration and Operator In-
terface, TROVIS-VIEW.
To configure the positioner, connect its addi-
tional
SERIAL INTERFACE
to the RS-232 in-
terface of a PC using an adapter cable.
After adapting the positioner to the process
requirements, TROVIS-VIEW enables the
process to be controlled online.
8
EB 8383-1 EN
Design and principle of operation
Summary of Contents for foundation 3787
Page 83: ...EB 8383 1 EN 83...
Page 84: ...84 EB 8383 1 EN...
Page 85: ...EB 8383 1 EN 85...
Page 86: ...86 EB 8383 1 EN...
Page 87: ...EB 8383 1 EN 87...
Page 88: ...88 EB 8383 1 EN...
Page 89: ...EB 8383 1 EN 89...
Page 90: ...90 EB 8383 1 EN...
Page 91: ...EB 8383 1 EN 91...
Page 92: ...92 EB 8383 1 EN...
Page 93: ...EB 8383 1 EN 93...
Page 94: ...94 EB 8383 1 EN...
Page 95: ...EB 8383 1 EN 95...