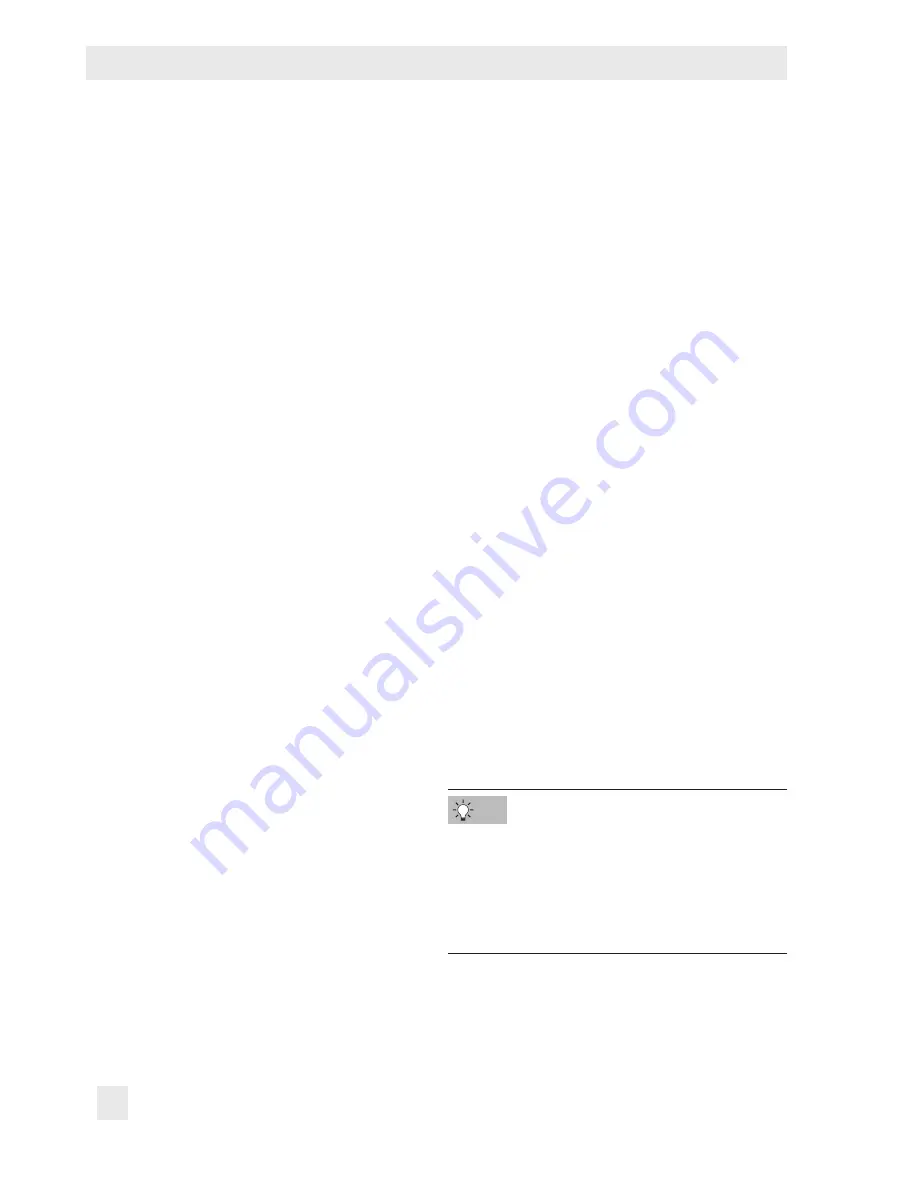
12
EB 8091-1 EN
Design and principle of operation
3 Design and principle of oper-
ation
The Type 3510 Micro-flow Valve is available
as either a globe or angle valve and is pref-
erably combined with a SAMSON
Type 3271 or Type 3277 Pneumatic Actuator
with 120 cm² actuator area. It can also be
combined with other actuators.
The seat (2.2) and plug (2.1) are installed in
the body (1). The plug stem is connected to
the actuator stem (A7) by the stem connector
and is sealed by an adjustable packing with
PTFE seal rings (34).
The anti-rotation fixture (2.4) prevents a
loosening of the screw connection between
the valve body and intermediate piece (4).
Two anti-rotation fixtures are used for ver-
sions with an insulating section or bellows
seal: one anti-rotation fixture between the
body and insulating section/bellows seal as
well as one anti-rotation fixture between the
insulating section/bellows seal and interme-
diate piece.
The springs in the pneumatic actuator are lo-
cated either above or below the diaphragm
depending on the selected fail-safe action
(see section 3.1). A change in the signal
pressure acting on the diaphragm causes the
plug to move. The actuator size is deter-
mined by the diaphragm area.
The medium flows through the valve in the
direction indicated by the arrow. A rise in
signal pressure causes the force acting on
the diaphragm in the actuator to increase.
The springs are compressed. Depending on
the selected direction of action, the actuator
stem retracts or extends. As a result, the plug
position in the seat changes and determines
the flow rate through the valve.
3.1 Fail-safe positions
The fail-safe position depends on the actua-
tor used.
Depending on how the compression springs
are arranged in the pneumatic actuator, the
valve has two different fail-safe positions:
Actuator stem extends (FA)
When the signal pressure is reduced or the
air supply fails, the springs move the actua-
tor stem downward and close the valve. The
valve opens when the signal pressure is in-
creased enough to overcome the force exert-
ed by the springs.
Actuator stem retracts (FE)
When the signal pressure is reduced or the
air supply fails, the springs move the actua-
tor stem upwards and open the valve. The
valve closes when the signal pressure is in-
creased enough to overcome the force exert-
ed by the springs.
The actuator's direction of action can be re-
versed, if required. Refer to the operating
and mounting instructions of the pneumatic
actuator, e.g.
u
EB 8310-1 for Type 3271
and
Type 3277 with 120 cm² actuator area.
Tip
Summary of Contents for 3510
Page 29: ...EB 8091 1 EN 29...