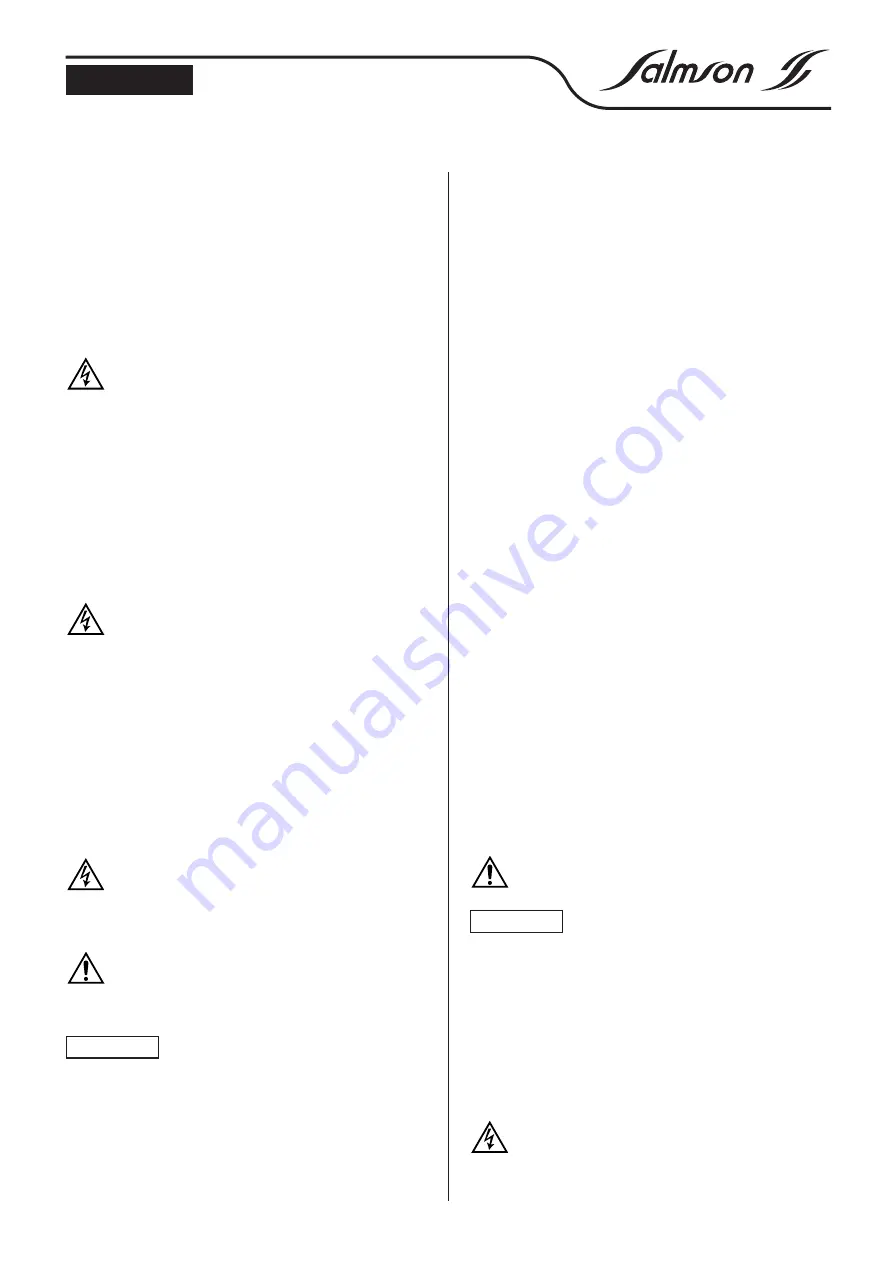
8
By hose with spiral reinforcement or by rigid pipe.
The diameter of the suction piping must never be less than that of
the pump.
Limit the length of the suction pipe and avoid all features that cause
losses of head (tapers, bends, valves,...).
No air entrance is allowed on the suction pipe which is showing a
mounting declivity (2%) (
see FIG. 1
).
If a rigid pipe is used, provide supports or collars so that the pump
does not bear its weight (
see FIG. 1
).
Carefully seal the pipes with suitable product.
5.3. Electrical connections
The electrical connections and checks must be made by a
qualified electrician and comply with applicable local
standards
.
Refer to the motor data plate for its electrical characteristics
(frequency, voltage, nominal current). Check if the motor it
complies with the mains supply used.
The three-phase motor must be protected by a circuit-breaker set to
the current marked on the motor data plate.
The single-phase motor has built-in thermal protection.
Provide a fuse disconnecting switch (type
aM
) to protect the power
supply.
Line power
Use a cable meeting standard board.
•
THREE-PHASE
: 4 conductors (3 earth)
•
TWO-PHASE
:
3 conductors (2 earth)
A connection error would damage the motor. The power
cable must never touch the pipe or the pump; make sure
that it is away from any moisture.
The electric connections should be made as shown by the
diagrams inside the cover of the motor terminal box (or see
FIG. 3).
The electric motors used with pumps can be connected to a
frequency converter.
Strictly follow the directions given by the manufacturer’s data sheet
.
The converter must not generate voltage peaks at the motor
terminals higher than 850 V and dU/dt (Voltage/Time variation)
higher than 2500 V/µs. If the value of the voltage signal are higher
than those, risk of damage the motor are to forecast.
If it does, place an LC (inductance-capacitance) filter between the
converter and the motor.
It must be connected to the motor with a minimum length cable,
armoured if necessary.
DO NOT FORGET TO CONNECT THE EARTH.
6. STARTING UP
6.1. Prior cleaning
An hydraulic test is carried out on each pump in our factory.
Some water stays inside them. It is recommended for hygien
reasons to clean the pump before using it on the potable
water supply.
6.2. Filling, degassing
Never operate the pump dry, even briefly.
Pump under pressure (see Fig. 2)
- Close the discharge valve (
3
).
- Unscrew the filling plug (
5
).
- Open the suction valve progressively (
2
) and completely fill the
pump. Screw the filling plug back in only after water flows out and
all air has been eliminated.
Pump in suction
. Two cases are possible:
FIRST CASE (see FIG. 4-1):
- Close the discharge valve (
3
).
- Open the suction valve (
2
).
- Unscrew the filling plug (
5
) on the main body of the pump.
- Put a funnel into the port and slowly and completely fill the pump
and the suction pipe.
- When water flows out and all air has been eliminated, filling is
complete.
- Screw the plug back in.
SECOND CASE (see FIG. 5-2)
Filling can be made easier by fitting, on the pump suction pipe, a
vertical pipe with a stopcock and a funnel.
- Close the discharge valve (
3
).
- Open the suction valve (
2
).
- Unscrew plug (
5
).
- Fill the pump and the suction pipe completely, until water flows out
of the bleed device and all air bubbles have disappeared.
- Close the stopcock (which can be left in place), remove the pipe,
and screw the filling plug back in.
- Start the motor by pressing briefly, wait for 20’ to let air going up
inside pump housing.
- Unscrew once again the plug (
5
) and, if a water flow doesn’t
appear, remove plug and complete the water level inside the
pump. Close the plug and start again.
- If necessary, repeat this operation.
NOTE :
At a maximum suction height of 7 metres, the pump is primed
in about 30 seconds.
NOTE :
We recommend to protect the pump against dry-running
with an adequate device (automatic control, float switch, pressure
switch).
6.3. Check dislocking and the motor sense of rotation
Whith an open-end screwdriver placed in the slot of the shaft on fan
side, make sure that the pump turns freely without sticking.
Switch on the motor by short pressing on the motor-overload release
and check that it turns in the direction indicated by the arrow
located on the indentification label of the pump.
If not, interchange two phase wires on the motor terminal block or
circuit-breaker.
NOTE
: The single-phase motors are designed to turn in the right
direction in all cases.
6.4. Starting up
Depending on conveyed fluid and running of pump, surface
temperature can exceed 68°C. Take necessary means to
avoid injuries.
The pump must not be operated in a no-flow
condition (discharge valve closed) for more than
10 minutes.
We recommend establishing a minimum flow of about 10 % of the
rated capacity of the pump, to avoid the formation of a gas pocket
at the top of the pump.
Open the discharge valve to start the pump.
Use a pressure gauge to check the stability of the discharge
pressure; if it is unstable, bleed the pump again or perform the filling
operation.
Check that the current draw does not exceed the value marked on
the motor data plate.
7. SERVICING
Before any operation, switch off the pump(s).
No special servicing in operation. Always keep the pump perfectly
clean.
CAUTION !
CAUTION !
ENGLISH