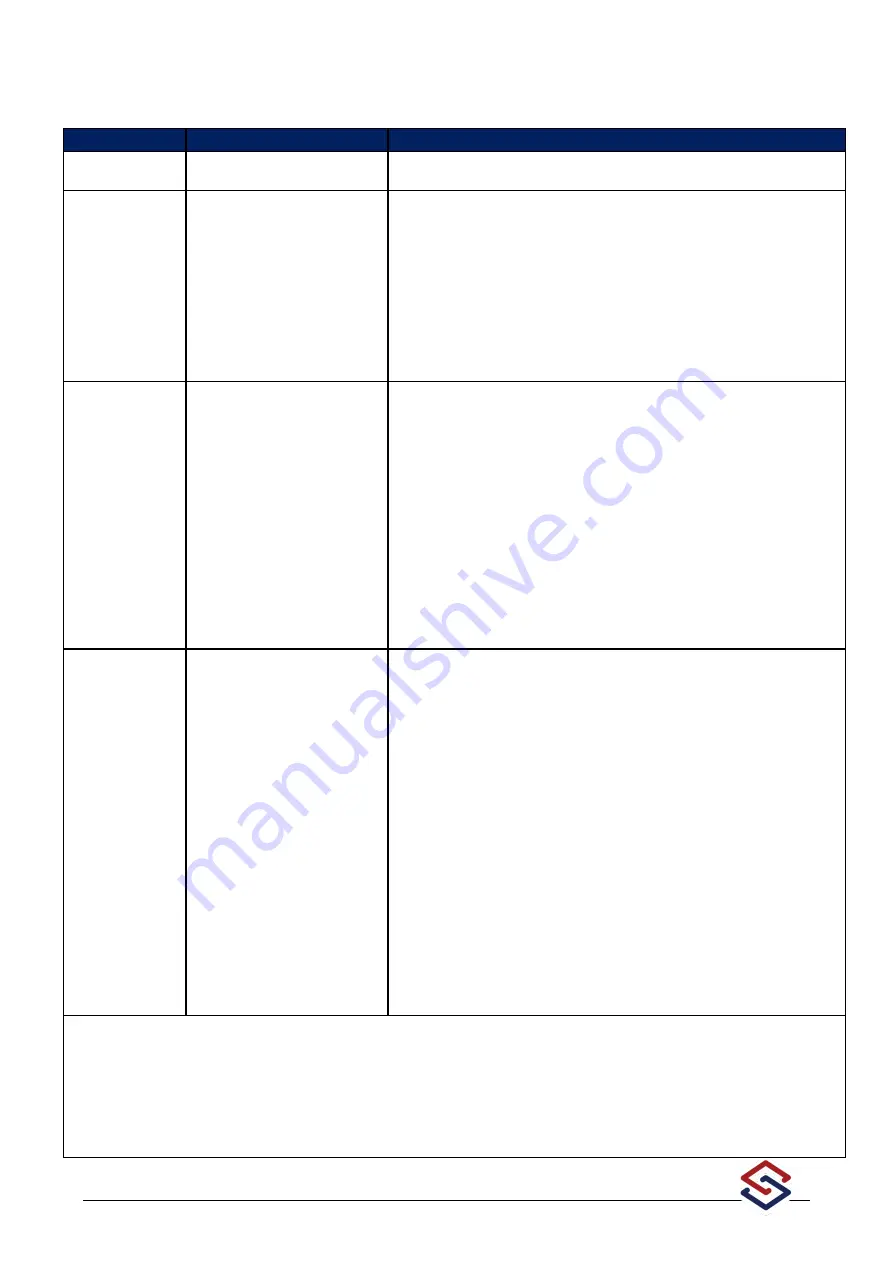
17
Model ASx-900|
Owner’s Manual
| Version no: 1
Problem
Possible Causes
Remedy
4) Flow controller may be
fully closed.
Open flow controller as described in section 4.11.
5) Thermal overload on
motor contactor may
have tripped. (Three
phase lift table only)
This condition will
invariably have
occurred during raise
and will also have
disabled the raise
function.
Reset the overload by opening the contactor box and
pressing the red reset button on the overload. Investigate
and rectify the source of the overload before lowering the lift
table in case access beneath the platform is required.
6) Down solenoid fuse on
the control board may
have blown
Check the down solenoid fuse mounted on the control board.
Open the enclosure housing the control board and check the
fuse with a multi-meter. The fuse is 1 amp 1" long x 1/4"
diam ceramic type. When replacing the board, carefully
bunch cores beneath the board. Ensure that board stand-
offs sit in the bottom of the box without fouling cables.
SmartLift diagnosis as follows:
(1) Check that the orange "Power on" LED is on and that the
red "Safety bar tripped" is off.
(2) Press the down control. If the green "Down control
made" is on and the orange "Power to down solenoid" is not,
the down solenoid fuse on the board is blown.
Lift table will
not lower.
Cont.
7) If none of the above, a
mechanical, electrical
or hydraulic fault may
exist.
Contact your Safetech agent.
SmartLift diagnosis:
(1) Fault in controller
i. Check that the orange "Power on" LED is on.
ii. Press the down control. The green "Down control made"
LED should illuminate, regardless of the status of the safety
bar. If not, there is an electrical fault in the controller.
(2) Burnt out solenoid
i. Check that the orange "Power on" LED is on.
ii. Remove the solenoid from the valve spindle and insert a
screwdriver through the bore as described below.
iii. Press the down control. If the green "Down control made"
and the orange "Power to down solenoid" illuminate but
magnetic pull cannot be felt on the screwdriver, the solenoid
is burnt out.
With causes 1,3, 5, & 6 the solenoid will not be energised when the down control is pressed.
With causes 2 & 4, the solenoid will be energised.
The energising of the solenoid can be verified be removing the solenoid from the down valve spindle,
inserting a screwdriver through the solenoid bore and pressing the down control. If the solenoid
energises, the magnetic pull can be clearly felt on the screwdriver. This is a useful test to help isolate
problems.