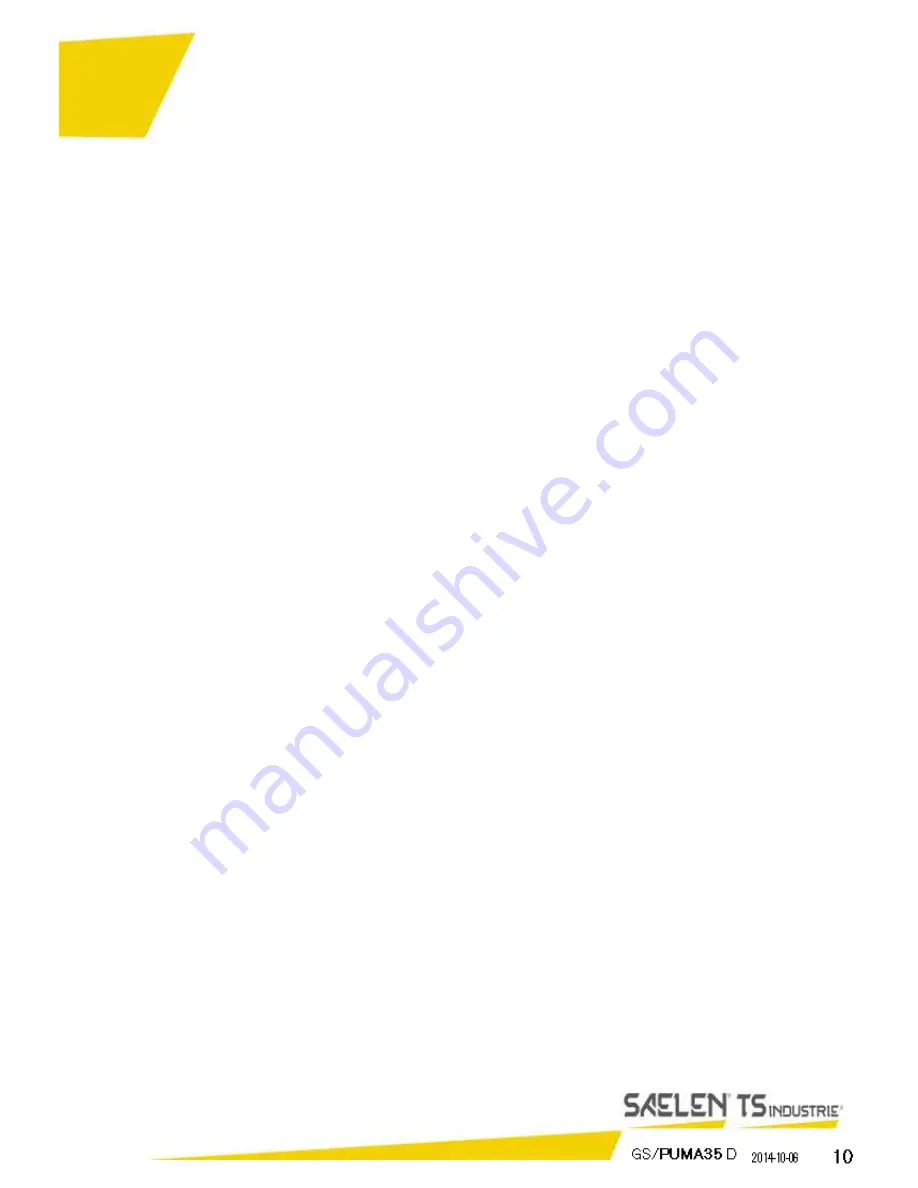
Safety instructions
1.
The machine is only allowed to be used according to the operating manual!
2.
In case of machines with engine also the operating instructions of the engine are to be observed.
3.
Folding the intake extension up (as far as present) is only allowed after standstill of the rotor.
4.
Maintenance, cleaning and setting works as well as the removal of protective devices are only
allowed after the engine is shut down, the ignition switched off, the drive decoupled and the tools
immobile. Remove the ignition key such that unintended start is impossible.
5.
Prior to operation it is required to remove foreign matters, e.g. ferrous parts, stones etc.
6.
After maintenance or repair it is to be checked if all protective devices are mounted.
7.
The wood chipper is not allowed to be operated in closed spaces because of the risk of
intoxication.
8.
The rotor must not be uncovered before it has reached standstill. That is to say, the propulsion
engine (tractor) is parked and the ignition is in 0-position.
9.
The machine operator is responsible that no third persons are staying in the working and danger
area.
10.
For repairs it is to be observed to use approved original spare parts only.
11.
Only persons of over 18 years are allowed to operate the wood chipper.
12.
Safety shoes and tight fitting clothes, work gloves with tight gauntlets as well as ear protection
and goggles are to be used.
Summary of Contents for GS/PUMA 35D
Page 1: ......
Page 2: ......
Page 3: ......
Page 28: ...nuts...
Page 29: ......
Page 30: ......
Page 36: ......
Page 37: ...slightly tensioned Correctly retighten locknut...
Page 38: ......
Page 50: ......
Page 52: ......
Page 54: ...1...
Page 57: ...Specifications...
Page 58: ......
Page 59: ...PUMA 120 bar Hydraulic Circuit Diagram Infeed roller Con veyor Backwards Forwards...
Page 64: ......