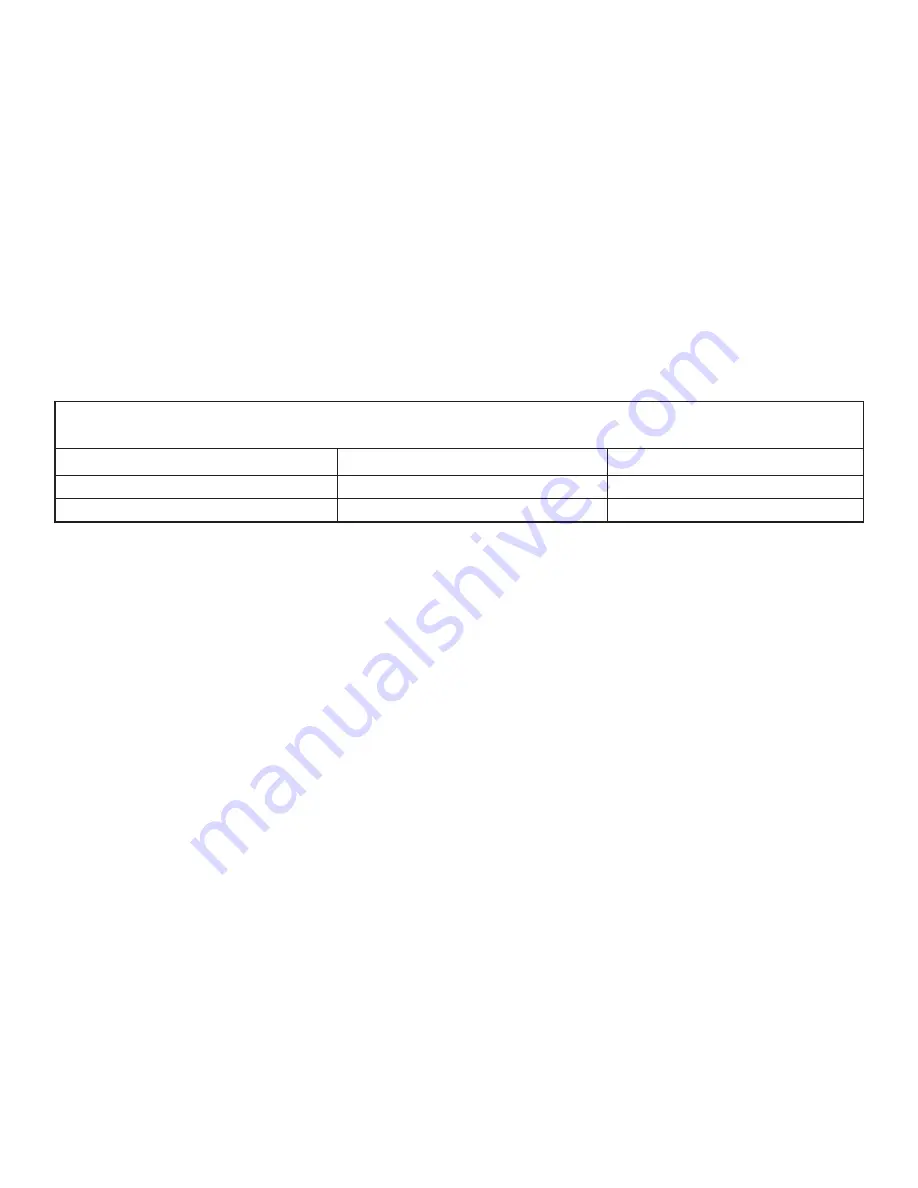
TABLE 5
7071 SERIES SHAFT RUNOUT TOLERANCES
SLEEVE FIT
COUPLING FIT
WITH SLEEVE
.002
.001
WITHOUT SLEEVE
.001
.001
25
4. Inspect the shaft (9) and sleeve (16) for
grooves or pitting, replace if any are found.
Ensure the shaft bearing fits are within the
tolerances in Table 4. Also, check that shaft
runout does not exceed the values in Table
5.
5. Inspect the bearing frame (13) and pedestal
(14) for cracks. Remove all loose foreign ma-
terial from inside the frame. Ensure that all
lubrication passages are clear.
6. Inspect stem plate (23) for pitting or wear
greater than 1/8” deep, and make sure that
the gasket surface is clean.
7. Inspect the bearing housing (6) for cracks
and pitting. Check that the bore is within the
tolerances. Replace bearing housing if bore
exceeds these tolerances.
8. Inspect the bearings (5 & 10) for contami-
nation or damage. If bearing damage is not
from normal wear, correct the problem be-
fore using pump. Do not reuse bearings.