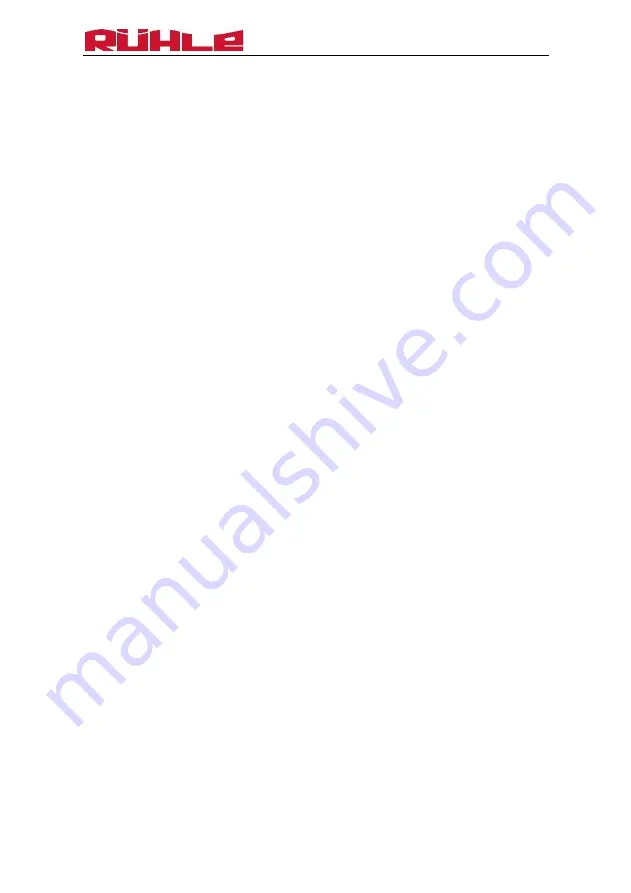
Cutting Centre SR 2 BiTurbo
21
Foundation load:
7,1 kN/m²
Emission sound pressure level: <70 dB(A) averaged, when idling
accuracy class 2, as per
DIN EN ISO 3744: 2010
Measuring instrument:
Brüel & Kjær Type 2240
Hydraulic oil tank:
8 litres (filling 5 litres)
Hydraulics oil:
Mobil SHC Cibus 32,
NSF H1 registered
The data on the type plate principally applies; it is located on the back
of the machine. In case of deviations, please contact the manufac-
turer for a written confirmation of the data!
If your country requires an RCD as protective measure, an RCD (type
B), AC/DC sensitive, must be used.
7.2
Electrical circuit diagram
The electrical circuit diagram of your machine is located in the electri-
cal control cabinet and must be supplied when reselling the machine!