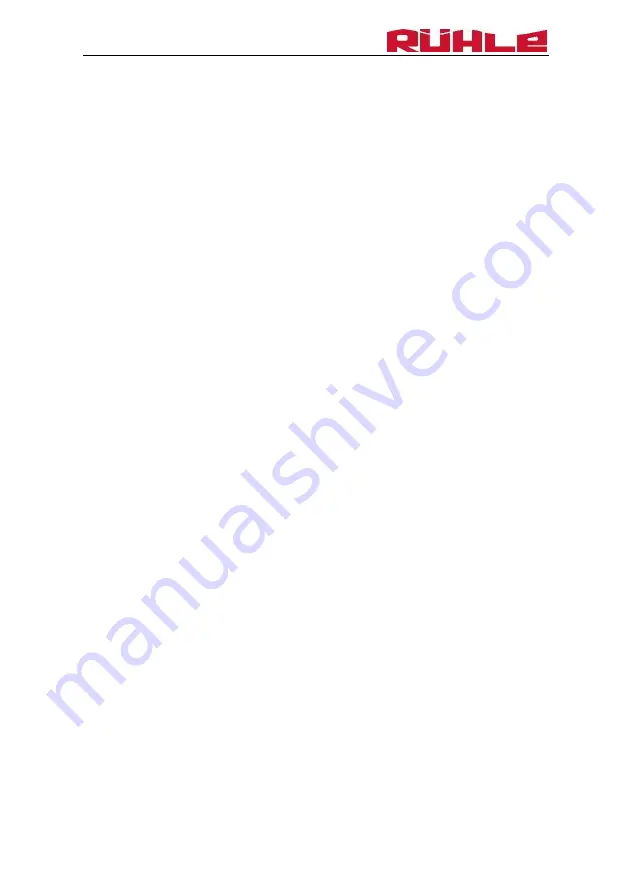
Cutting machine SR 1 / SR 1 Turbo
16
6
Disposal
1.
The following components contain oil:
Main drive for cutting
Dispose of the oil properly!
2.
The following components contain lubricating grease:
DC drive for the pre-pressing function
Free-wheeling rollers
Dispose of the lubricating grease properly!
3.
The following components contain lubricating oil:
All chains and their gear
Dispose of the lubricating grease properly!
4.
All other materials must be sorted and disposed of at a
recycling facility!
7
Technical documentation
7.1
Technical data
Connection voltage:
400 V 50/60 Hz 3-phase AC / N / PE
Power consumption:
2.1 kW
Full-load current:
4.4 A
Back-up fuse max.:
16 A
Protection class:
IP54
Ambient temperature:
+2 °C to + 40 °C
Cut product temperature:
-5 °C to + 80 °C
Dimensions, W × H × D:
2080 × 1078 × 1390 mm
Funnel size:
100 × 100
×
350 mm
Cut-off length:
1 – 32 mm
Cutting speed
SR 1:
80 sections/min
SR 1 Turbo:
160 sections/min
Cutting output max.
SR 1:
900 kg/h
SR 1 Turbo:
1500 kg/h