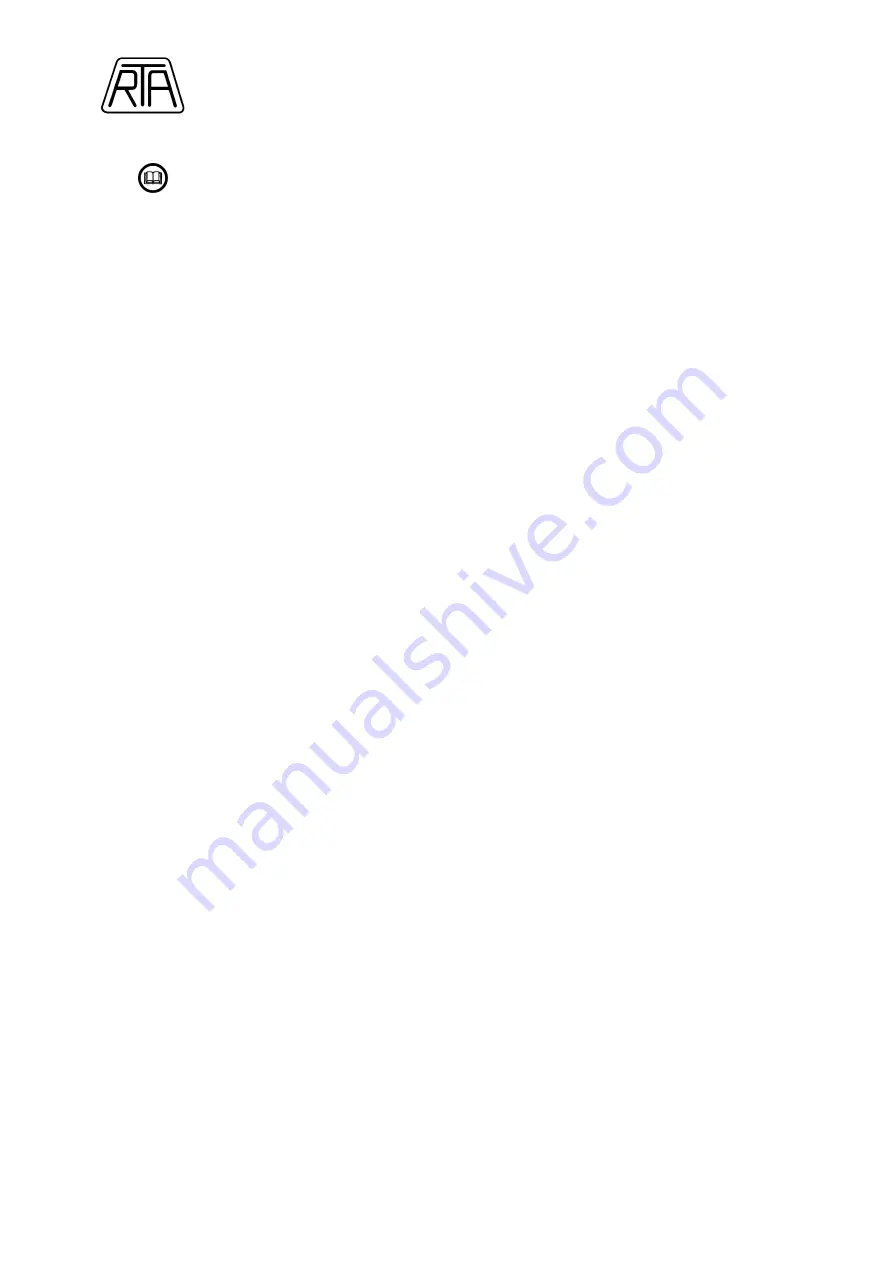
R.T.A. s.r.l. – XPETME05 – 11/20
20/29
11 - APPLICATION NOTES
11.1-
INFORMATION
.
Electromagnetic compatibility (directive 2014/30/CE). X-PLUS ET series drives are BDM (Basic
Drive Module), as defined in the EN 61800-3. Only a professional assembler, expert in the field of
motor drives and in their EMC aspects, can install and put in service this component. R.T.A. has the
responsibility to verify the products compatibility in some typical way of use in order to give correct
installation information. In any cases, it is responsibility of the professional assembler, who installs
this product, to verify the compatibility of the complete machine or system.
11.1.1- The set consisting of drive, motor, transformer and all related cablings are source of electromagnetic
interferences. The assembler of installation must consider these problems during the project of the
plant where the drive (or drives) will be installed in order to shield and/or reduce these interferences.
Tests performed by R.T.A. show that the most effective measures able to reduce these interferences
are the following:
•
Shielding of cables for the connection between motor and drive. The shield of this cable has to
be directly connected to X-PLUS ET series drive terminal 5. The shield of encoder cable, if it is
available, has to be directly connected to the earth screw of the drive. This shielding can be
avoided only in case of very small and compact machine where motor, drive and related
connections are located in the same enclosure, showing adequate shield performance.
•
It is suggested not to exceed the maximum length of 10 meters for the wiring between motor
and drive. In case of application requires the exceeding of this limit, please contact RTA.
•
Connect earth line to motor chassis. To reduce the radio-frequency emissions, the mechanical
connection of motor to machine chassis (by means of mounting flanges and screws), is typically
simple and effective solution. In this case, both screws and chassis must be of conductor
material and the chassis must be connected to earth. See Fig. 14.
•
Location of drive in a cabinet shielded from electromagnetic interferences.
•
Interpose an EMI filter in AC power input line (see Fig. 7) in order to reduce conducted
electromagnetic interferences. Filter characteristics in a specific installation depend on following
factors:
- Strictness degree of the specific standard regarding the machine on which drive is used.
- Power level of application (voltage and current setting of the drive).
- Presence of other filtering systems in the general electrical machine installation.
In any case, following filter type is recommended:
-
CORCOM SK series.
Different models inside these series differ for current rating; thereby choose the specific model
according to power level of your installation.
•
Consider that the position of the filter in the system is extremely important: no electromagnetic
coupling must take place between electromagnetic source and circuits (and lines). To this end,
filter and main must be kept as close as possible.
•
All earth connections mentioned above have to be realized with the less possible inductance.
11.1.2- To improve the drive logic input/output signals immunity from external noise the following well
known procedures, to manage the relatively fast signals treatment must be considered:
•
Use shielded cables.
•
Keep signal cables separate from power cables. In particular keep signal cables separate from
motor output cables.
•
Carefully verify logic level compatibility when interfacing drive with control system.