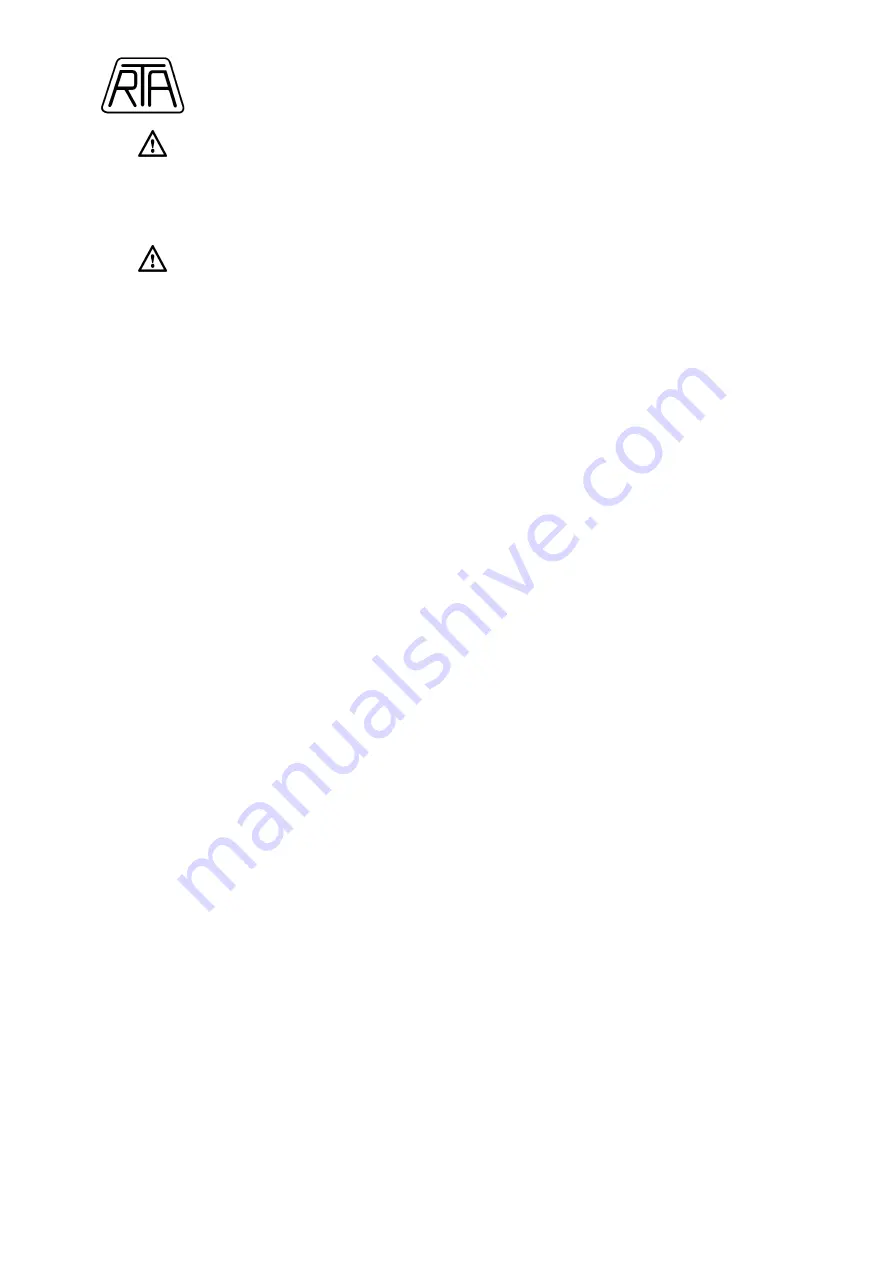
R.T.A. s.r.l. – XPETME05 – 11/20
25/29
12.5-
WARNING!
RISK ASSESSMENT
The drive meets the requirements safety standards above described.
However, before activating safety function, make sure to assess the risks associated with the overall
equipment to ensure complete safety.
12.6-
WARNING!
RESIDUAL RISK
Even if STO function is active, the following risks remain. Please ensure the installation safety is
maintained, even in case the below-indicated situations occur, through a correct risk assessment.
1. When STO function is activated while the motor is running, the current into the motor is shut
down. The motor continues to run due to inertia. Please make sure to ensure safety conditions of
the system to avoid any danger until the motor stops completely.
2. When the motor is used in vertical axes, it is possible that without holding torque, the axes rotate
due to gravity. In this case, it is necessary to provide external device (i.e. electromagnetic brake)
to stop the motor within requested range.
3. In case of short circuit or failure of power device transistor, the motor could make an uncontrolled
movement within a range up to 180 degrees in electrical angle (180 degrees in electrical
angle=1/50 of a turn) and then remain a stable position. It is necessary to verify that this limited
movement does not correspond to some risky conditions.
4. Be sure that SAFE TORQUE OFF function properly works before machine use, at first machine
start-up and at every drive replacement. If input / output signals are not used correctly, the STO
function doesn’t work properly and dangerous situation can occur.
5. When STO function is active, the drive power supply is not shut down. In case of maintenance or
check of the drive, please be sure to shut down power supply to avoid electric shock.
12.7-
CONNECTIONS
All input and output logic signals are optically insulated among them and from internal power circuits.
For each input signal correspondent terminals numbers of connector C3b are indicated:
51 :
IN+
STO2.
Input IN+ STO2.
52 :
IN- STO2.
Input IN- STO2.
53 :
Shield.
Shield connection for STO inputs cables.
54 :
IN+
STO1.
Input IN+ STO1.
55 :
IN- STO1.
Input IN- STO1.
The outputs are considered ON when they are closed as regards to common of outputs (24). For
each signal the correspondent terminals numbers of connector C2 are indicated:
21 (O2):
O2 OUTPUT.
Auxiliary output.
If it is set as
Driver FAULT OUTPUT
(see software manual), output is ON when drive is
active; output is OFF when drive is blocked by a protection.
22 (O1):
O1 OUTPUT.
Auxiliary output.
If it is set as
EDM, Error Detection Monitor
(see software manual),
output is ON if both
STO1 and STO2 inputs are OFF. In this case, the drive is in Safe Torque Off operation
mode and the current flowing in each motor winding is inhibited. The output is OFF if one
or both STO1 or STO2 inputs are ON.
23 (O0):
O0 OUTPUT.
Auxiliary output.
24:
COMMON OF OUTPUTS.
Note:
Depending on status of object 0x320A, user can set output values (see software manual).