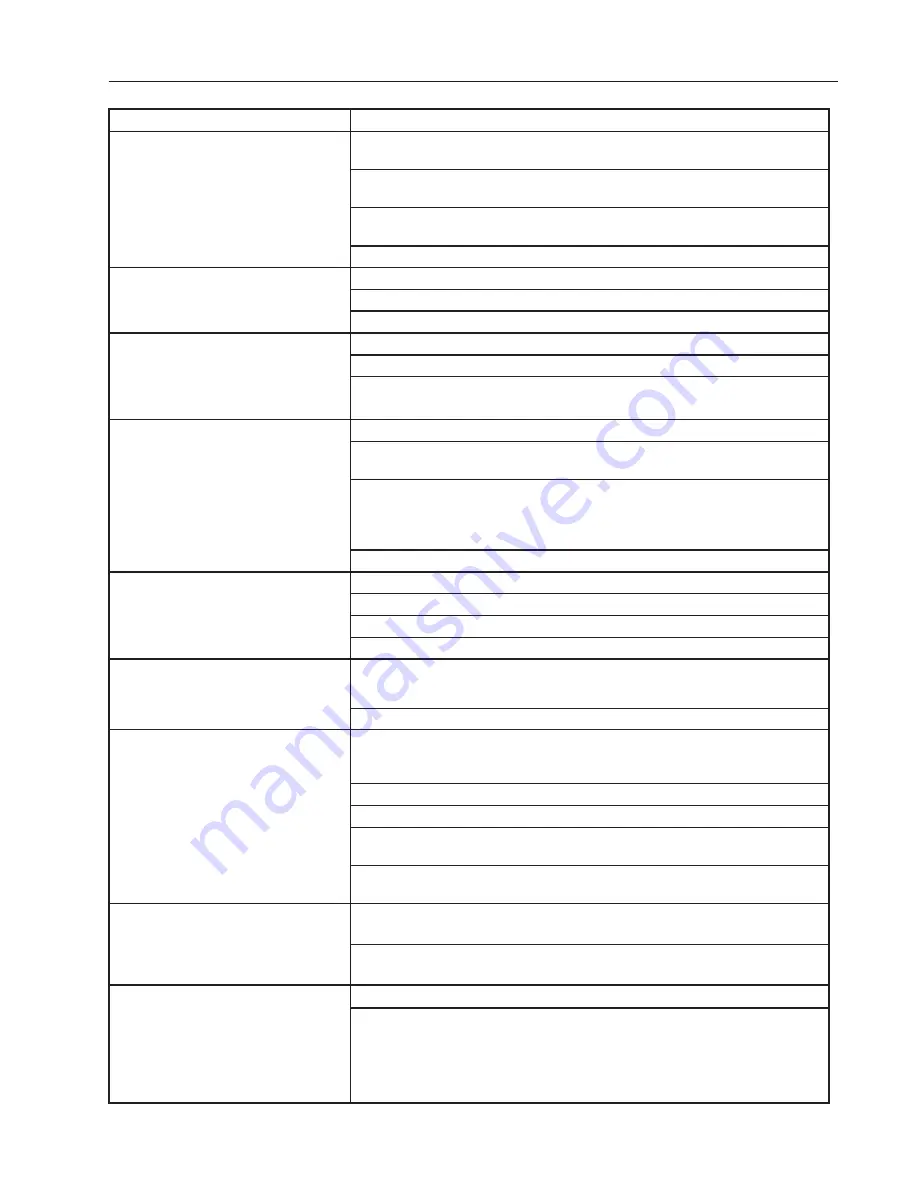
47
RVV Gen II KO Service and Parts Manual
SECTION 5: Troubleshooting
Error / Problem
Possible Cause / Corrective Action
Product cup does not find shelf,
does not pull product, or pulls out
product only half-way.
(continued
from previous page)
Check to make sure the X-magnet is located in the left-hand corner of the odd
numbered cell (behind the price label) that the product cup is not finding.
Check for condensation under the X-motor encoder cap. If condensation is
found, refer to “X-motor troubleshooting,” below.
Check to make sure the back wheels of the product cup are locked into the
back rail (closest to the glass) and are properly seated in the cup.
If all the above does not help, replace the product cup assembly.
Product cup moves left and right in 2”
(5 cm) increments and then up about
8” (20 cm), then back down.
Check the connections at the X-motor.
Check the connections at position P2 on the DMC board.
If all the above is good, replace the X-motor.
Product cup begins its homing
sequence but fails to move up or
down after finding home. Cup then
moves to the left of the door and the
display shows OUT OF SERVICE.
Check the connections at the Y-motor.
Check the connections at position P1 on the DMC board.
If all the above is good, replace the Y-motor.
Display shows OUT OF SERVICE
after the door is shut and the
product cup performs its homing
routine. Cup does find the home
position, then shows OUT OF
SERVICE. CUP SENSOR error
shown.
Make sure there is nothing blocking the optic sensors in the product cup.
Remove the product cup floor and check the connections from the emitter and
detector boards to the logic board in the cup (positions P6 and P7).
Remove the covers to the emitter and detector boards to make sure the two
boards are aligned properly and the lenses are seated properly (black lens on
the left and clear lens on the right). Check the connections at the emitter and
detector boards.
If all the above does not help, replace the product cup assembly.
Product cup goes to the correct
selections but fails to pick up a
product and the cup returns to the
home position. The display shows
PLEASE RE-SELECT.
Check calibration.
Use the cup test in the Diagnostics menu to test the plunger function.
Refer to error / problem “Product cup...half-way,” shown above.
If all the above is good, replace the product cup assembly.
Gantry will not stay level.
With the fuse removed, re-level the gantry arm. Drive the gantry arm up by pulling on
the port-side Y-belt. If you hear a clicking noise (the belt slipping), adjust the tension on
the Y-belts and re-test.
Check the top idler assembly and Y-motor for loose pulleys.
X-motor troubleshooting.
Carefully remove the rubber X-motor encoder cap and check for
condensation. If condensation is found, allow the encoder to dry, and search
for the cause of the condensation.
Check the connections at the X-motor and at position P2 on the DMC board.
Check the X-belt for proper tension and the X-motor pulley for slippage.
Use the motor / encoder test in the Diagnostics menu to check the function of
the X-motor.
If after replacing the X-motor the problems still persist, replace the X-motor
harness.
Cup is able to open delivery port
door, but the cup will not tilt to
deliver product.
Check calibration on PORT X. Refer to the service and parts manual
for calibration instructions.
While in X-port calibration, adjust the cup trim arm so that it catches
the trip bracket above the delivery port.
Cell attempts to multi-vend to the
cup.
For clear products, check the cup optic sensors and lenses.
For all other products:
a. Check the shelf for proper seating.
b. Check the Hall Effect sensor on the drive motor.
c. Check for 5 VDC on the red and black wires at position P5 on the
cup logic board.