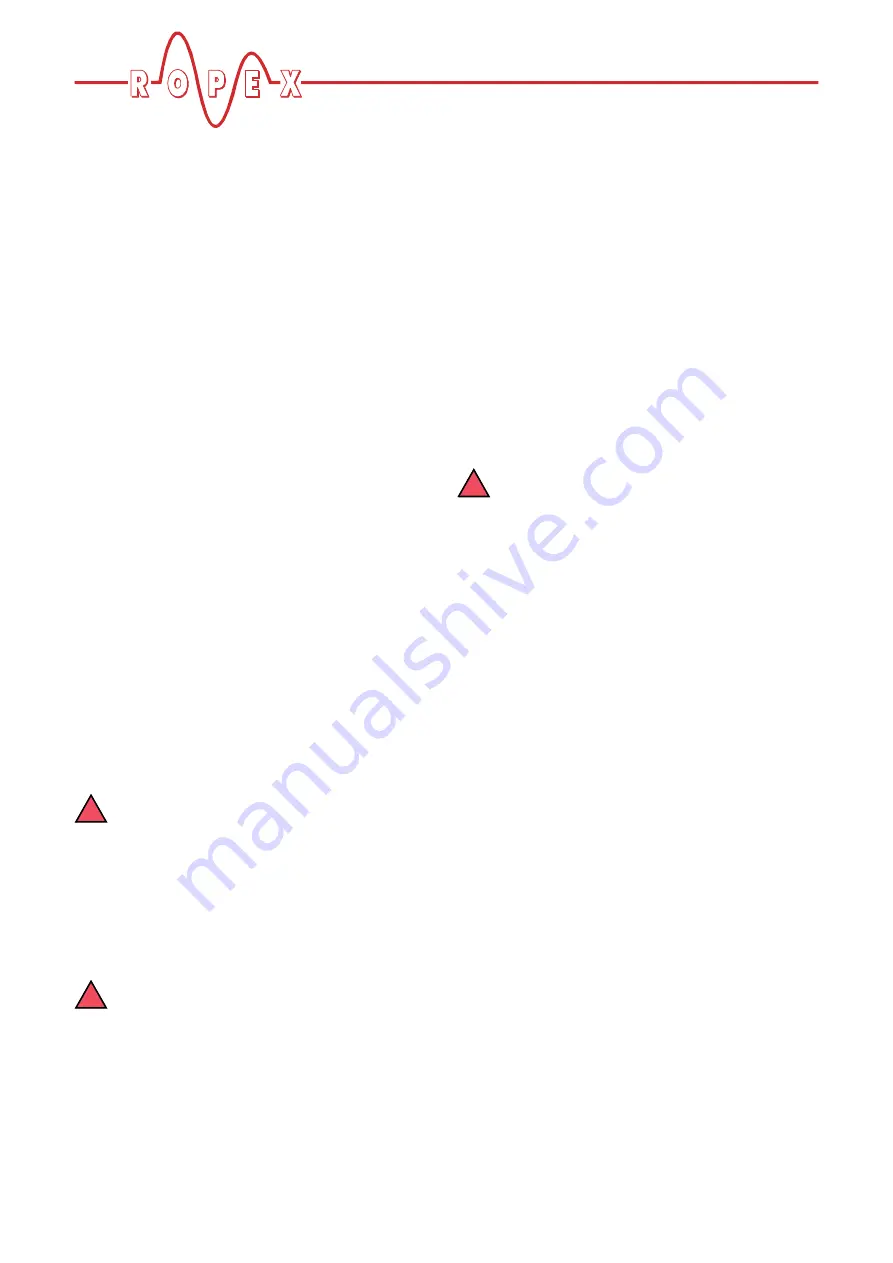
Startup and operation
Page 20
RESM-5
8.3
Heatsealing band
8.3.1
General
The heatsealing band is a key component in the control
loop because it is both a heating element and a sensor.
The geometry of the heatsealing band is too complex to
be discussed at length here. We shall therefore only
refer to a few of the most important physical and
electrical properties.
The measuring principle applied for this system
requires a heatsealing band alloy with a suitable
temperature coefficient TCR, i.e. one whose resistance
increases as the temperature rises.
Too low a TCR leads to oscillation or measurement
errors.
If a heatsealing band with a higher TCR is used, the
RESISTRON monitoring device must be calibrated for
this.
The first time the heatsealing band is heated to
approximately 200…250°C, the standard alloy
undergoes a once-only resistance change (burn-in
effect). The cold resistance of the heatsealing band is
reduced by approximately 2…3%. However, this at first
glance slight resistance change results in a zero point
error of 20…30°C. The zero point must therefore be
corrected after a few heating cycles (
"Replacing the heatsealing band" on page 20).
One very important design feature is the copper or
silver-plating of the heatsealing band ends. Cold ends
allow the temperature to be controlled accurately and
increase the life of the Teflon coating and the
heatsealing band.
An overheated or burned-out heatsealing
band must no longer be used because the
TCR has been irreversibly altered.
8.3.2
Replacing the heatsealing band
All power supply leads must be disconnected from the
RESISTRON monitoring device in order to replace the
heatsealing band.
The heatsealing band must be replaced in
accordance with the instructions provided by
the
manufacturer.
To
prevent
dangerous
situations, refer to the risk analysis for the machine
or plant.
Each time the heatsealing band is replaced, the zero
point must be calibrated with the AUTOCAL function
while the band is still cold in order to compensate
production-related resistance tolerances. The burn-in
procedure described above should be performed for all
new heatsealing bands.
8.4
Startup procedure
Please also refer to section 1 "Safety and warning
notes" on page 3 and section 2 "Application" on
page 4.
Installation and startup may only be
performed by technically trained, skilled
persons who are familiar with the associated risks
and warranty provisions.
8.4.1
Initial startup
Prerequisites: The unit must be correctly installed and
connected (
section 7 "Installation" on page 14).
All possible settings are described in detail in
section 8.2 "Unit configuration" on page 18 and
section 9 "Unit functions" on page 22.
The essential configurations of the RESISTRON
monitoring device are described below:
1. Switch off the line voltage and verify that the circuit
is de-energized.
2. The supply voltage specified on the nameplate of
the unit must be identical to the line voltage that is
present in the plant or machine. The line frequency
is automatically detected by the RESISTRON
monitoring device in the range from 47 to 63Hz.
3. Make sure no START signal on the temperature
controller is applied.
4. Switch on the line voltage.
5. A power-up message appears on the display for
approximately 2 seconds when you switch on the
monitoring unit to indicate that it is being powered
up correctly.
!
!
!