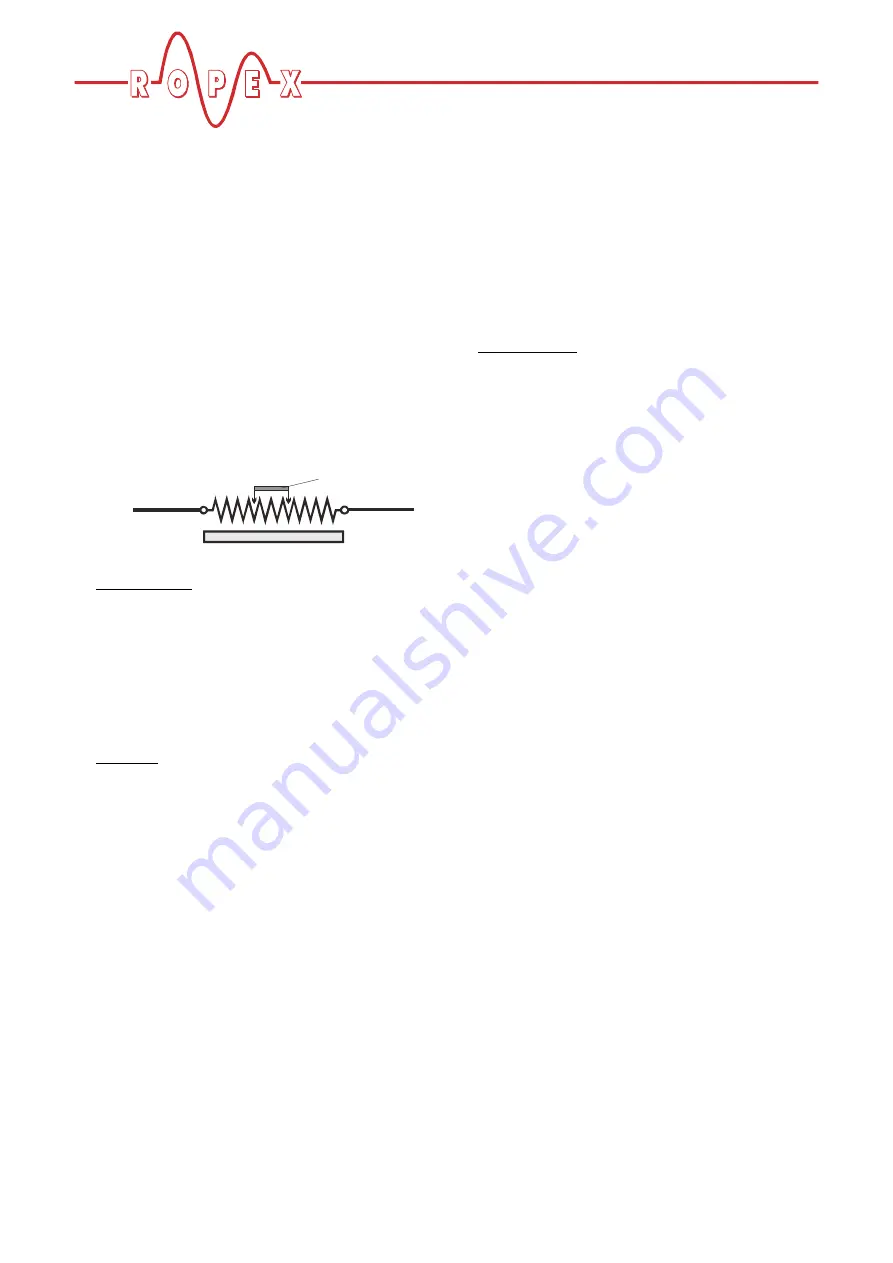
Basics of temperature control / measurement
Page 10
RESM-5
3.6
Residual risks
Even if the RESISTRON monitoring device RESM-5
(and the optional monitoring current transformer MSW)
are used, there are still a few operating states that can
cause undetected overheating of the heatsealing band.
Some of these fault causes have already been
described in detail above.
They are summarized again below:
• Non-coppered heatsealing band ends
• Heatsealing band with no TCR or a TCR that is too
low
• Conductive, ungrounded part which partially short
circuits the heatsealing band during the heating
phase
Consequence: The controller measures a lower
resistance and continues heating to a higher
temperature.
• Reduction in the resistance measured by the
controller (between the two connection points on the
voltage measurement cable U
R
) during the heating
phase (similar effect to that described above but a
different cause)
Example:
The clamp for the heatsealing band connection
makes poor contact (loose contact)
→
contact
resistance.
The sealing tool is open, the heatsealing band is
cold, and the controller is calibrated using the
AUTOCAL function.
The tool closes and the controller heats up.
The contact with the heatsealing band improves
under the closing pressure, the resistance is
reduced, and the controller heats to a higher
temperature.
In other words:
The zero point is calibrated when the circuit has high
impedance.
The circuit has lower impedance during the heating
phase.
Consequence: Overheating
• Physical damage to the heatsealing band
(contraction, cracking etc.) leading to a narrower
cross section
The heatsealing band overheats at this point
(HOT SPOT). It can glow red-hot as a result.
• The resistance increase which occurs here is so
small in relation to the total resistance that it cannot
be detected by the controller in practice.
• Incorrect operation
Example: AUTOCAL is run when the heatsealing
band is hot
• Design error regarding the installation and wiring of
the control and monitoring system.
Remedy: Check regularly that the monitoring
system is working correctly by deliberately inducing
short circuits, breaks etc. (checklist).
Partial short-circuit