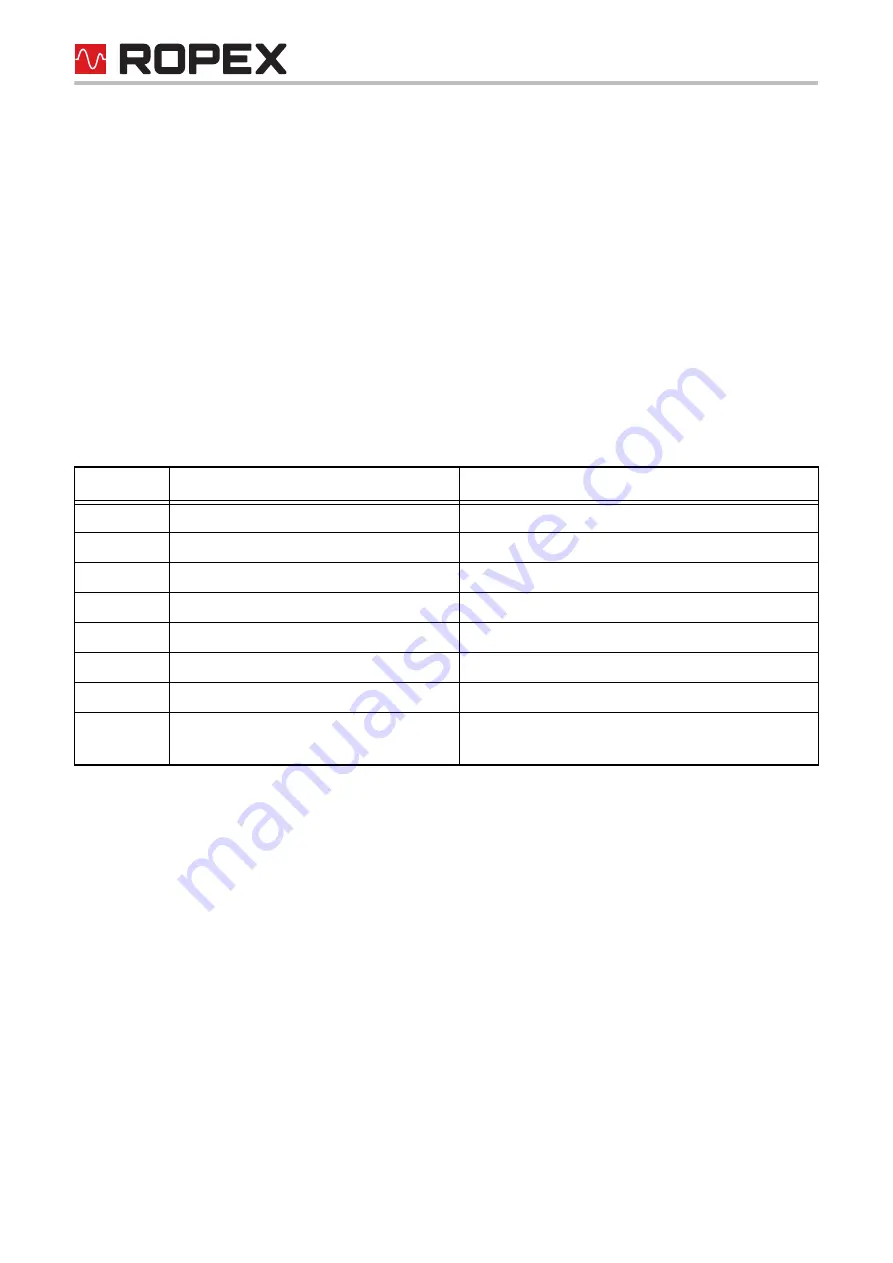
CANopen
Page 72
RES-5009
Version 1
10.13 Master AUTOCAL (MA)
Setting the master AUTOCAL request (MA bit) starts the calibration process as in section 9.2.1 "AUTOCAL (AC)
automatic zero calibration" on page 30. But in addition, after successful performance of the Master AUTOCAL
function, the heating element resistance determined by the controller is stored as a reference value, e. g. after a
heating element replacement.
This reference value is used as the basis for calculating the calibration value deviation in subsequent calibration
processes (started by AUTOCAL request). The calibration value deviation can be used to evaluate the ageing of
the heating element.
10.14 Temperature range and alloy
Parameter object 4000h can be used to select both the temperature range and the heating element alloy. By
changing the standard value (10), the setting of the rotary coding switch (
section 8.2.2 "Configuration of the
rotary coding switch for temperature range and alloy" on page 22) can be overwritten.
With setting 11, the value stored under CANopen object 400B
h
is applied for the temperature range. For the alloy,
the value stored under CANopen object 400A
h
for the active channel is applied.
After changing the parameters “Temperature range/alloy”, “Temperature range” or “Temperature coefficient”, the
AUTOCAL function must be executed.
10.15 TCR calculator
The TCR calculator can be used to determine the temperature coefficient (TCR) of the heating element used. The
real temperature coefficient of the heating element often deviates from the standard value. The material compo-
sition and the processing influence the properties of the heating element. This causes the temperature display of
the controller to deviate from the real temperature of the heating element. The use of the TCR calculator allows a
simple correction of the TCR value and thus a better match between the temperature display of the controller and
the real temperature of the heating element.
1. Measuring the real temperature: To calculate the TCR value, the temperature at the heating element is meas-
ured in control mode (ST bit = 1) using an external temperature sensor (e. g. a thermocouple).
2. Sending the measured temperature to the temperature controller: The measured temperature is transmitted to
the temperature controller in CANopen object 0x430A/01.
3. On the basis of these data, the temperature controller calculates a temperature coefficient.
Value
Temperature range
Alloy
0
300 °C
TCR = 1100 ppm/K,e.g. Alloy 20
1
300 °C
TCR = 780 ppm/K,e.g. Alloy L
4
500 °C
TCR = 1100 ppm/K,e.g. Alloy 20
5
500 °C
TCR = 780 ppm/K,e.g. Alloy L
8
300 °C
TCR = 3500 ppm/K, e. g. NOREX
9
Setting over PC visualisation
Setting over PC visualisation
10
Setting of the rotary coding switch
Setting of the rotary coding switch
11
Variable: Value from CANopen object
400B
h
is used.
Variable: Value from CANopen object 400A
h
is
used.
Summary of Contents for RESISTRON RES-5009
Page 4: ...Page 4 RES 5009 Version 1 ...