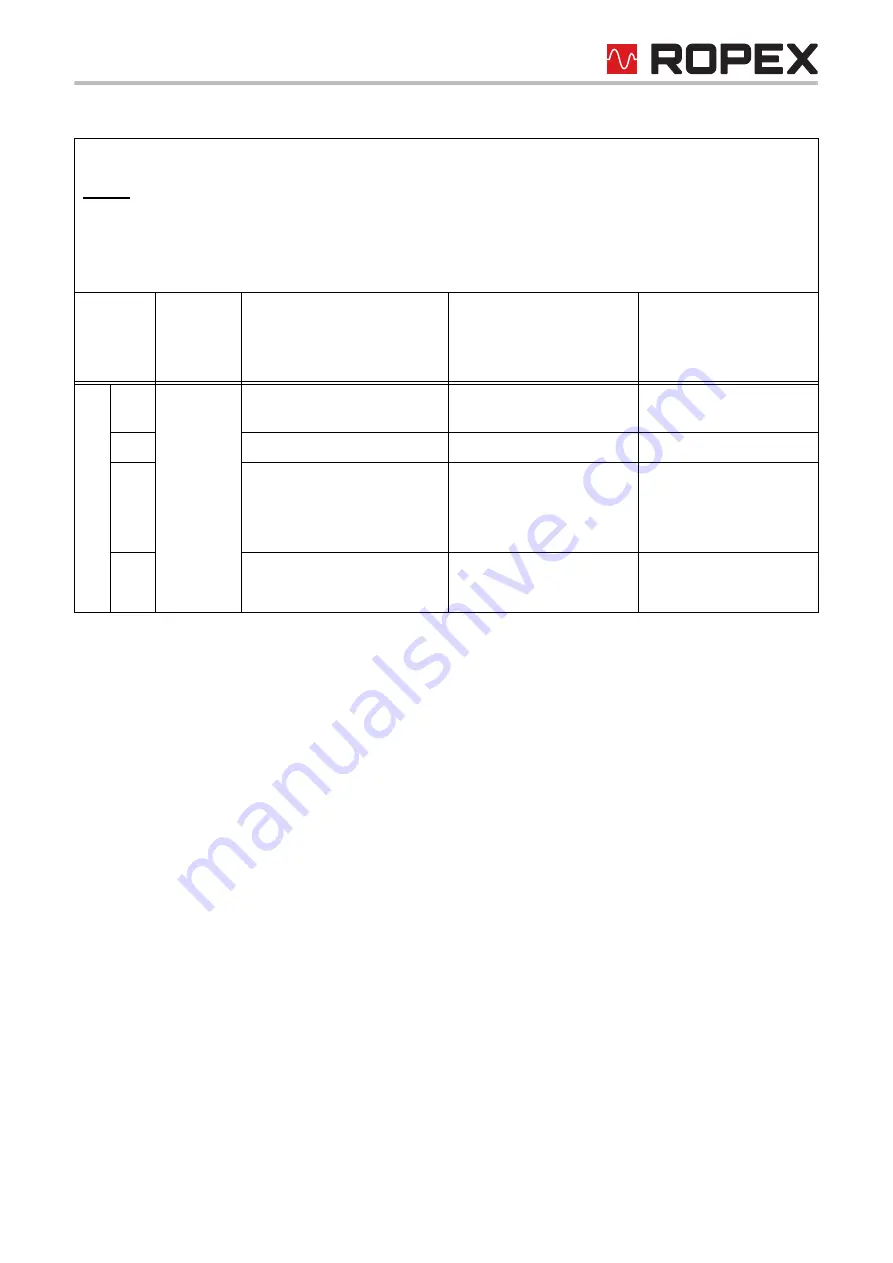
Device functions
Version 1
RES-5009
Page 51
7
901
4.66
Line voltage/synchronising
signal missing
Replace device
Replace device
913
Triac defective
Replace device
Replace device
914
Int. error, device defective
Replace device
Replace device
915
916
917
Incorrect slide switch for
alarm output
Check slide switch
Check slide switch
918
Part 1 of 3: Error messages (faults)
NOTE:
The specified error messages are output as faults:
• Actual value output displays constant error voltage
• Alarm LED lights up continuously
• Alarm relay is active
Error no.
Actual
value
outp.
Voltg. [V]
Cause
Measure during initial
startup
Measure during
machine operation,
heating element not
changed
Summary of Contents for RESISTRON RES-5009
Page 4: ...Page 4 RES 5009 Version 1 ...