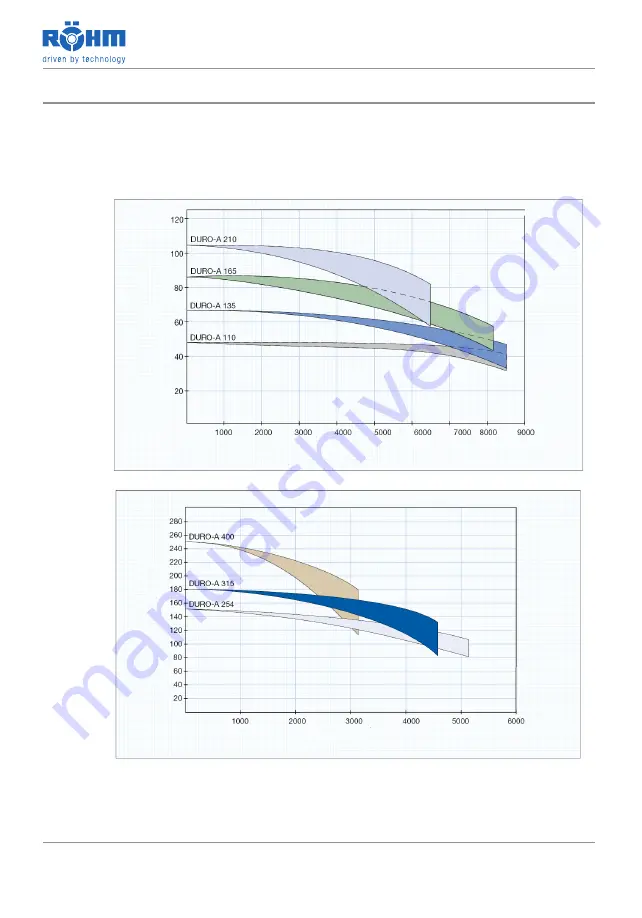
Product Description | 3
Power Chuck DURO-A
21 / 52
3.2.3
Clamping Force-Speed Diagram
The reduction in clamping force is experimentally determined with the jaws
assigned to the power chuck. It is largely independent of the initial clamping
force at a speed = 0.
Total clamping force kN – speed
rpm
Speed rpm
Total clamping force kN
Total clamping force kN
Speed rpm
Summary of Contents for DURO-A
Page 2: ......