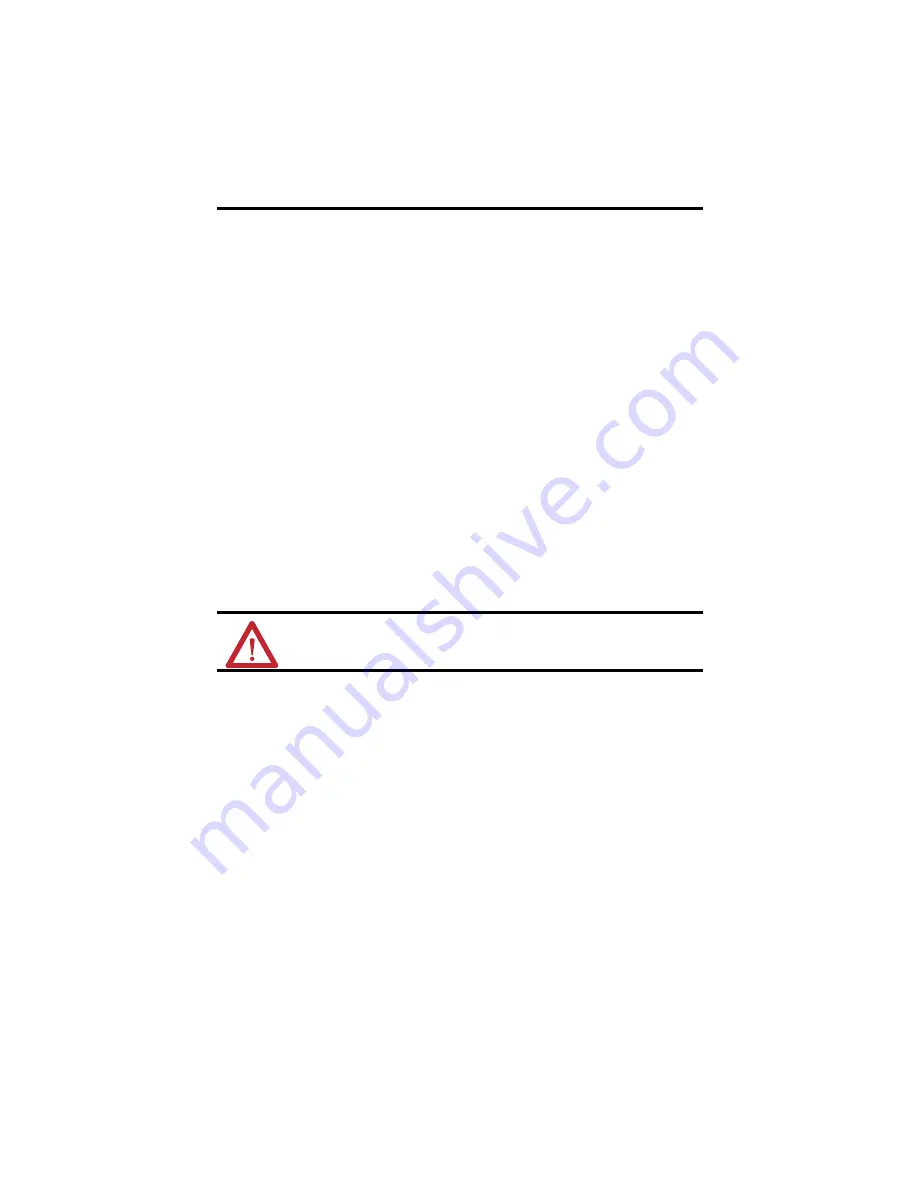
LDAT-Series Integrated Linear Thrusters
37
Rockwell Automation Publication LDAT-IN001B-EN-P - March 2020
Preventing Undetected and Repetitive High Energy Impacts
To prevent high energy impacts, take normal motion system precautions and make sure the
Position Error Tolerance is suitable for your application.
Normal motion system precautions include the following:
•
Interlocks for access
•
Range of motion hardware and software limits
In addition you should complete these tasks:
•
Determine limit positions based on maximum speed and load, and stopping distance at
peak capability of motor or drive. You can use Motion Analyzer to determine these
positions
•
Program the position error fault action to Disable Drive (default) or Stop.
•
Program the Limits tab in Axis Properties to reduce the Position Error Tolerance.
Typically, a value less than 10 mm (0.39 in.) is achievable without causing nuisance
Position Error (E19) faults.
•
In higher speed applications, implement 100% Velocity Feed-forward on the Axis
Properties Gains tab. This value reduces the Position Error during normal axis motion.
•
After performing an Auto-Tune, always set the Position Error Tolerance back to the
established reduced values.
When a closed-loop servo system is operating, changes in loads, obstructions, or equipment
dynamic response can cause motor capacity to be exceeded. Under these conditions, the Kinetix
6000 and Kinetix 2000 drives fold back the current to the motor to prevent thermal damage.
Typically, the fold back causes a closed-loop servo system to operate with reduced dynamic
control performance, particularly when accelerating and decelerating. If the reduced dynamic
control results in undesirable Position Error and the Position Error Tolerance is set to a relatively
large value, such as, the default value, the increase in Position Error may go undetected. If proper
precautions are not in place, this could lead to equipment damage and/or serious injury.
ATTENTION:
Motor capacity may be exceeded by load changes, obstructions or equipment
dynamic responses.