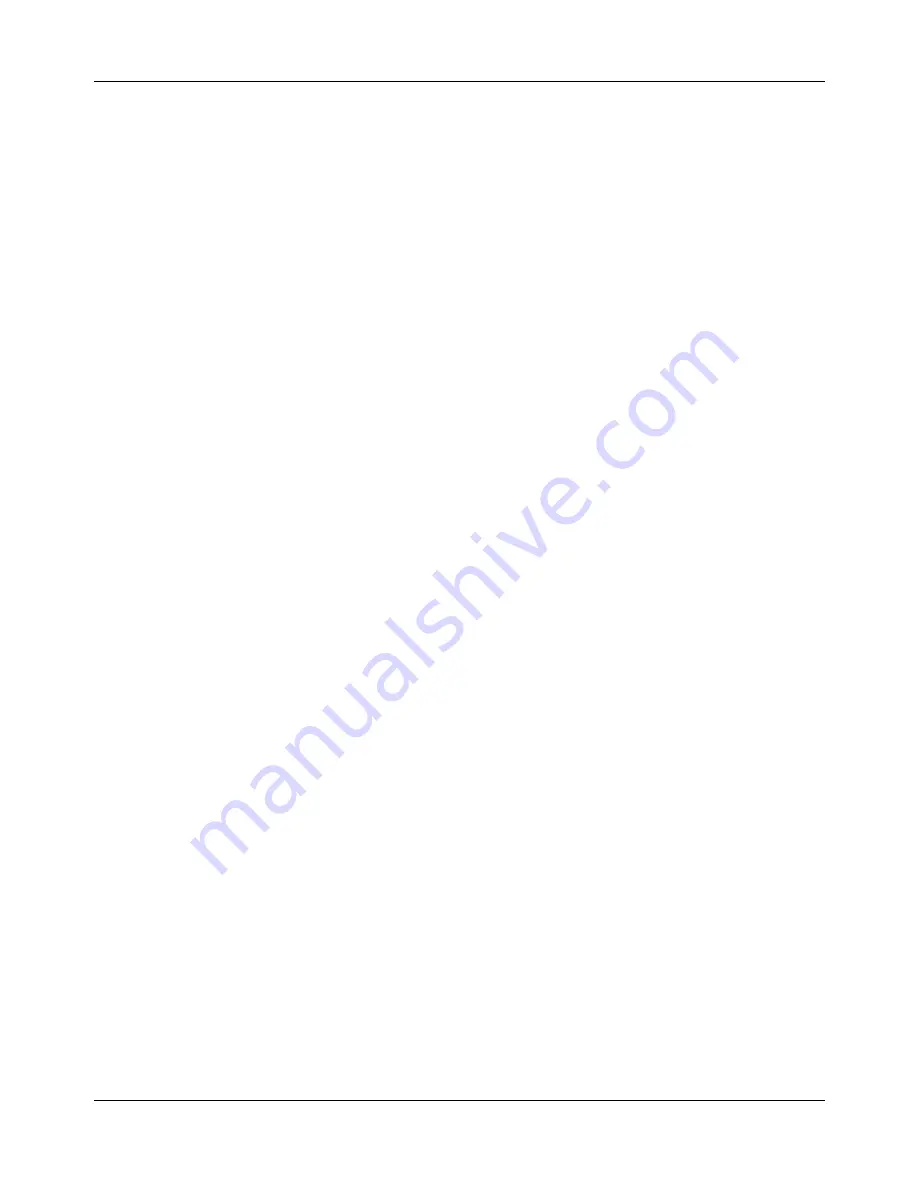
Operation
Theory of Operation
244
MagneMotion
Rockwell Automation Publication MMI-UM007F-EN-P - September 2020
Protocol User Manual
). This fault self-clears when the internal propulsion bus
voltage rises above +270V DC.
If the internal propulsion bus voltage drops below +250V DC during operation, the motor
reports an undervoltage fault through the HLC to the host controller. When this fault is
reported, vehicle motion over the motor is suspended. Normal operation resumes once the
internal propulsion bus rises back up to +270V DC.
This fault is likely due to exc300–400V DC power cable and +300–400V DC return
cable resistance from the power source to the motor.
Overvoltage Fault
When the internal propulsion bus in the motor rises above +430V DC, the motor reports an
overvoltage fault to the HLC. The HLC reports this fault to the host controller as an overvolt-
age fault (see either the
Host Controller TCP/IP Communication Protocol User Manual
,
, or the
Host Controller EtherNet/IP Communication Protocol User Manual
,
).
When this fault is reported, all inverters within the motor are disabled, and any vehicles in
motion over the motor are no longer under active control and as such their motion is unde-
fined. This fault self-clears and normal operation resumes once the internal propulsion bus
voltage falls below +420V DC. To avoid issuing an overvoltage fault to the host controller due
to spurious noise, the internal propulsion bus that is used to trigger this event is filtered.
Based on the specific system wiring and vehicle activity, it is possible for regenerated power
resulting from vehicle decelerations to cause the internal propulsion bus voltage to rise to
excessive levels. To help protect against this, protective features guard against operating con-
ditions that could damage the motor. Since the source of such a condition is due to regenera-
tion effects associated with active braking or deceleration of a vehicle (loaded or unloaded), a
means (among others) of mitigating such regenerated power is to shut down the inverters in
the motor.
Hardware Overcurrent Warning
When any phase current or the propulsion power input current exceeds ±25 A, the motor
reports an overcurrent warning. The HLC reports this warning to the host controller as a Hard-
ware Overcurrent Warning (see either the
Host Controller TCP/IP Communication Protocol
User Manual
,
Host Controller EtherNet/IP Communication Protocol
User Manual
,
When this warning is reported, the inverter clears the fault and retries 10 ms after the fault has
occurred. If the fault is still active, or another fault happens within 5 seconds, the inverter
latches off. Once the inverter latches off, the HLC reports a Hardware Overcurrent Fault to the
host controller. If 5 seconds pass and another fault has NOT happened, the inverter is allowed
to retry if a subsequent overcurrent fault occurs.