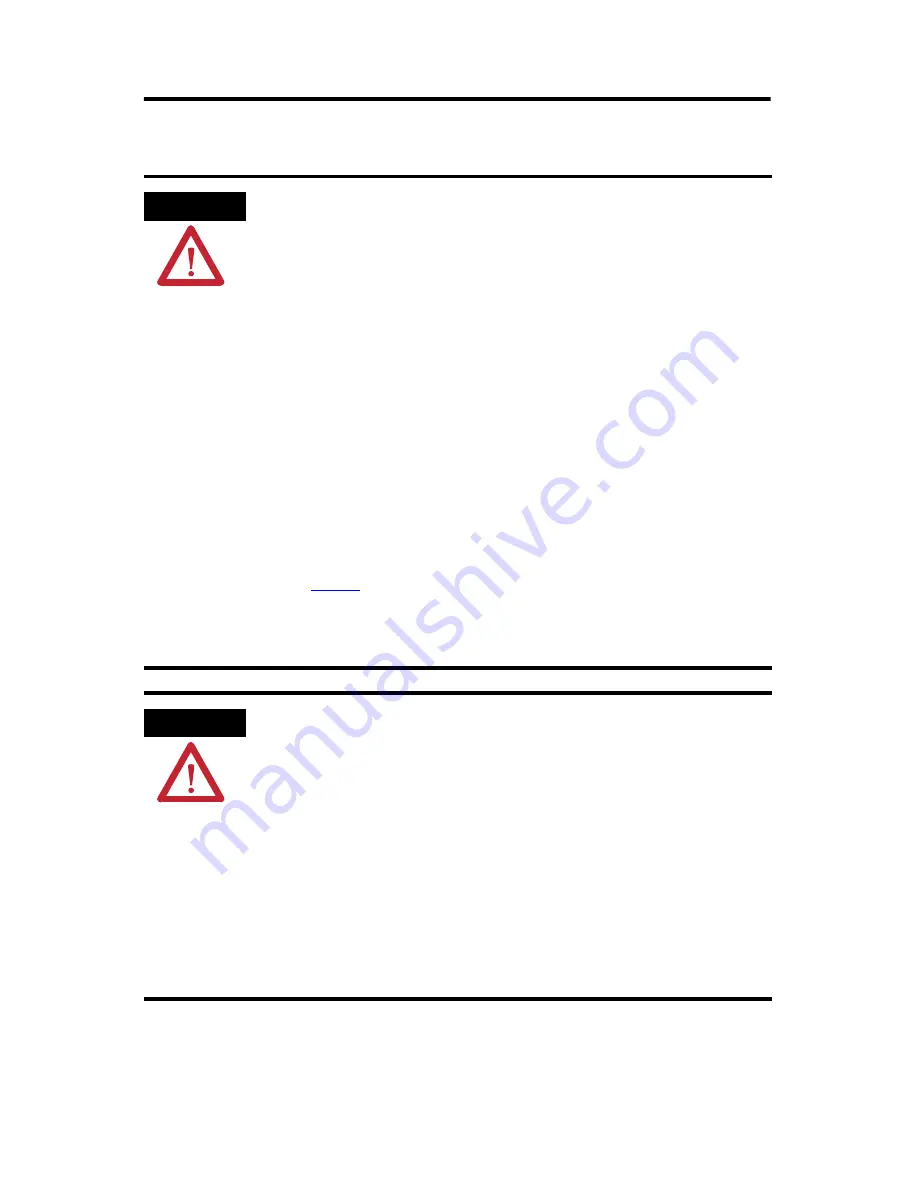
4
SmartGuard 600 Controllers
Publication 1752-IN001C-EN-P - January 2009
ATTENTION
Environment and Enclosure
This equipment is intended for use in Pollution Degree 2 Industrial environment, in
Overvoltage Category II applications (as defined in IEC publication 60664-1), at altitudes
up to 2000 m (6562 ft) without derating.
This equipment is considered Group 1, Class A industrial equipment according to
IEC/CISPR Publication 11. Without appropriate precautions, there may be potential
difficulties ensuring electromagnetic compatibility in other environments due to
conducted as well as radiated disturbance.
This equipment is supplied as open type equipment. It must be mounted within an
enclosure that is suitably designed for those specific environmental conditions that will
be present and appropriately designed to prevent personal injury resulting from
accessibility to live parts. The enclosure must have suitable flame-retardant properties to
prevent or minimize the spread of flame, complying with flame spread rating or 5VA, V2,
V1, V0 (or equivalent) if non-metallic. The interior of the enclosure must be accessible
only by the use of a tool. Subsequent sections of this publication may contain additional
information regarding specific enclosure type ratings that are required to comply with
certain product safety certifications.
In addition to this publication, see:
•
Industrial Automation Wiring and Grounding Guidelines, Allen-Bradley publication
1770-4.1
.
•
NEMA Standards publication 250 and IEC publication 60529, as applicable, for
explanations of the degrees of protection provided by different types of enclosure.
ATTENTION
Prevent Electrostatic Discharge
This equipment is sensitive to electrostatic discharge, which can cause internal damage
and affect normal operation. Follow these guidelines when you handle this equipment:
•
Touch a grounded object to discharge potential static.
•
Wear an approved wrist grounding strap.
•
Do not touch connectors or pins on component boards.
•
Do not touch circuit components inside the equipment.
•
Use a static-safe workstation, if available.
•
Store the equipment in appropriate static-safe packaging when not in use.