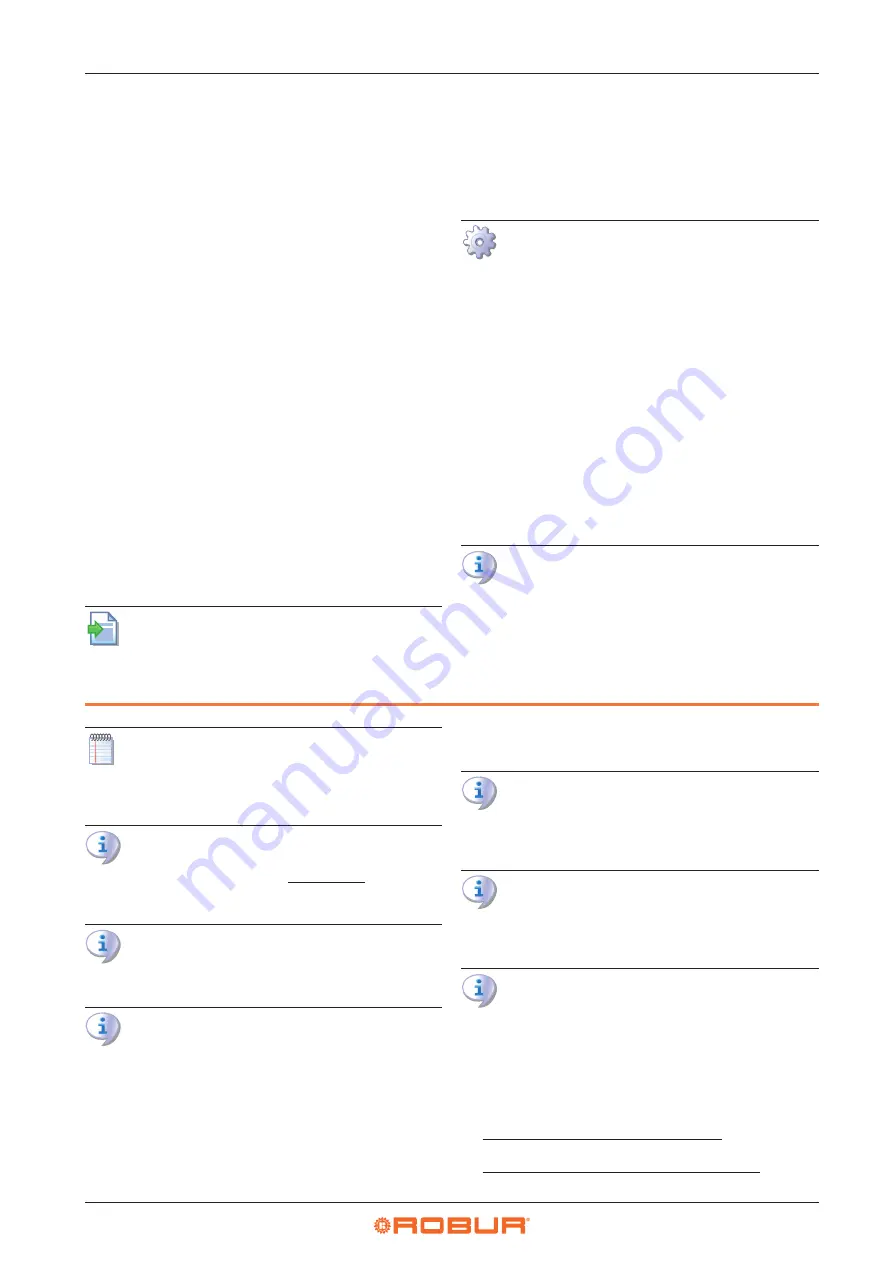
Normal operation
36
6
5. Turn the knob clockwise to scroll down and display the
other/subsequent menus; the menu numbers will be
displayed in order, "1.", "2.", ... , "6." ... or "E" (= exit).
6. Select the menu of interest (e.g. display "2.___" = menu
2) by pressing the knob; the first parameter code will be
displayed, in menu order (e.g. display "2._20" = parame-
ter 20 in menu 2).
7. Turn the knob clockwise to scroll down the other param-
eters in the menu; the codes will be displayed in order
(e.g. display "2._20", "2._21", ... "2._25" = parameters 20,
21, ... 25 in menu 2), or letter "E" (= exit) at the end of
the list.
8. Select the parameter of interest (e.g. with code 161 in
menu 3) by pressing the knob; the figure previously as-
signed to the parameter will be displayed, read only or to
be set (e.g. the figure "45" for parameter 161 in menu 3 =
water temperature set-point at 45 °C); if instead of a fig-
ure/setting it is a command, a flashing code is displayed
(e.g. "reS1" for the flame block reset command).
9. Press the knob to reconfirm the figure; or rotate the knob
to modify the figure, and press at the end to confirm or
set the new figure; if however, it is a matter of controlling
an appliance operation, press the knob to execute it.
10. To exit a parameter menu or the menu list and go back
to the higher level, turn the knob to display the letter "E"
for exit, then press the knob again.
11. Place the cover back on the electrical panel opening and
fit the appliance's front panel back on.
5.3
MODIFYING SETTINGS
Modify settings via the DDC
If the device is connected to the DDC control, refer to the
relevant manual to modify settings.
How to raise/lower the water temperature setpoint
The water temperature set-point establishes the outlet temper-
ature to the system (water output from the appliance), or inlet
from the system (water input in the appliance). The temperature
is pre-set by the TAC upon first start-up.
If the appliance is not connected to a DDC control, to
raise/lower the water temperature setpoint with the S61
or AY10 board, proceed as follows:
1. Access menu 3 under parameter "water temperature set-
point" (for heating parameter 161, for conditioning pa-
rameter 75) by rotating and pressing the knob; the dis-
play must show "3.161" or "3._75" (procedure Paragraph
p. 35).
2. Display the parameter value by pressing the knob; the
previously set value is displayed (from 10 to 65 °C for
parameter 161, from 4,5 to 25 °C for parameter 75); to
reconfirm the pre-existing value press the knob again,
otherwise go to step 3.
3. Turn the knob to modify the value, increasing or decreas-
ing it, and press it to set the new value.
4. Exit menu 3, and from the menu list, by selecting and
pressing letter "E" twice, and go back to the normal dis-
play of detected temperature data.
Do not modify complex settings
Specific technical and system knowledge is required for
complex settings. Contact a TAC.
6
NORMAL OPERATION
This section is for the end user.
6.1
WARNINGS
General warnings
Prior to using the appliance carefully read the warnings
in Chapter III.1
p. 4, providing important information
on regulations and on safety.
First startup by TAC
First start-up may exclusively be carried out by a Robur
TAC (Chapter 5
p. 34).
Never power the appliance off while it is running
NEVER power the appliance off while it is running (ex-
cept in the event of danger, Chapter III.1
p. 4), since
the appliance or system might be damaged.
6.2
SWITCH ON AND OFF
Routine switching on/off
The appliance may exclusively be switched on/off by
means of the suitably provided control device (DDC or
external enable).
Do not switch on/off with the power supply switch
Do not switch the appliance on/off with the power sup-
ply switch. This may be harmful and dangerous for the
appliance and for the system.
Checks before switching on
Before switching on the appliance, ensue that:
gas valve open
appliance electrical power supply (main switch (GS) ON)
DDC power supply (if any)
water circuit ready
How to switch on/off
▶
If the appliance is controlled by a DDC (system (1) see
Paragraph 1.6
p. 20), refer to the relevant manual.
▶
If the appliance is controlled by external enables (e.g. ther-
mostat, clock, button, ... with clean contact NO), (system (2)