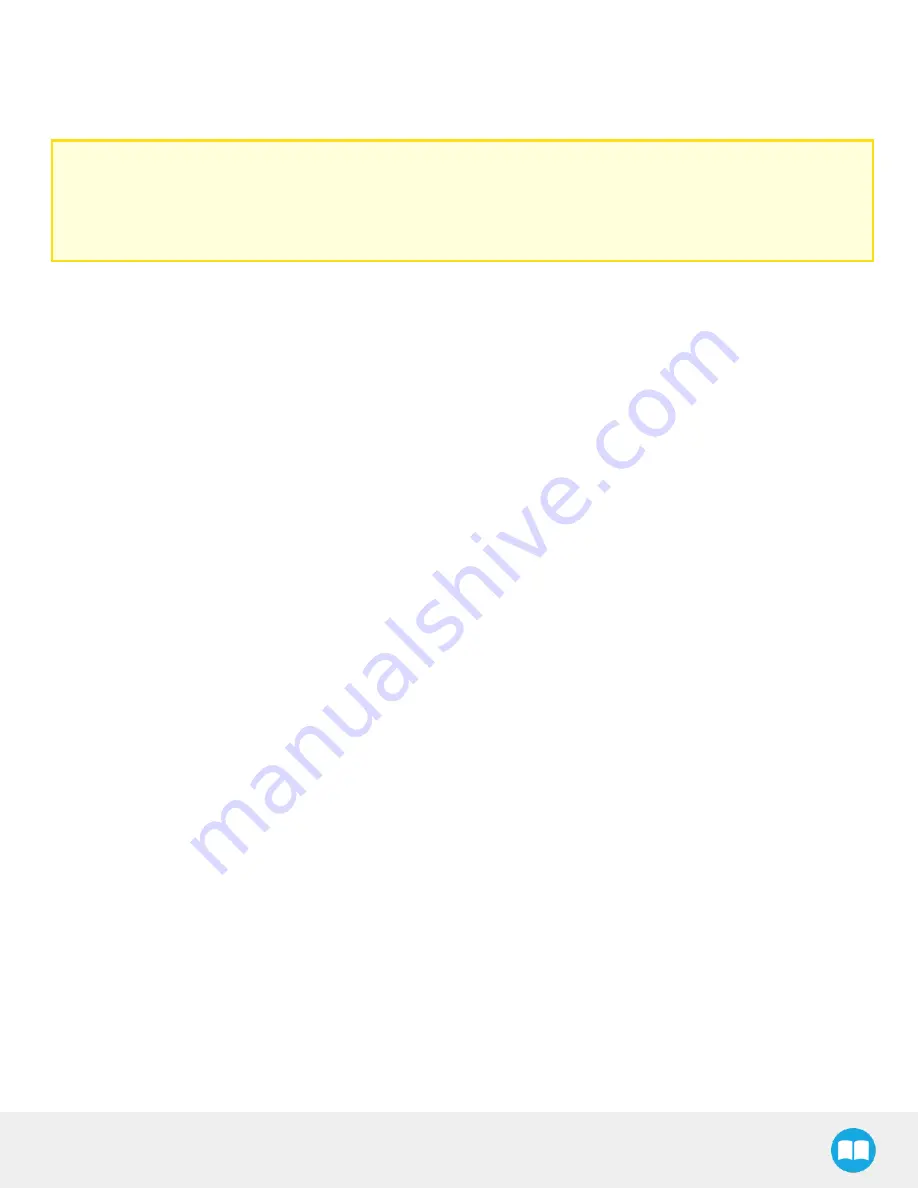
FT 300 Force Torque Sensor - Instruction Manual
62
Adapt to a User Application
In practice, the provided source code will be adapted to either: be incorporated with a custom application or to communicate with
one. At this point, the main.c file should be adapted according to the suggested comments inserted in the code.
Caution
Please note that Robotiq can only support our customers in making sure they can compile and test the provided code
as
is
.
No support can be provided for the integration of the provided source code into a custom application.