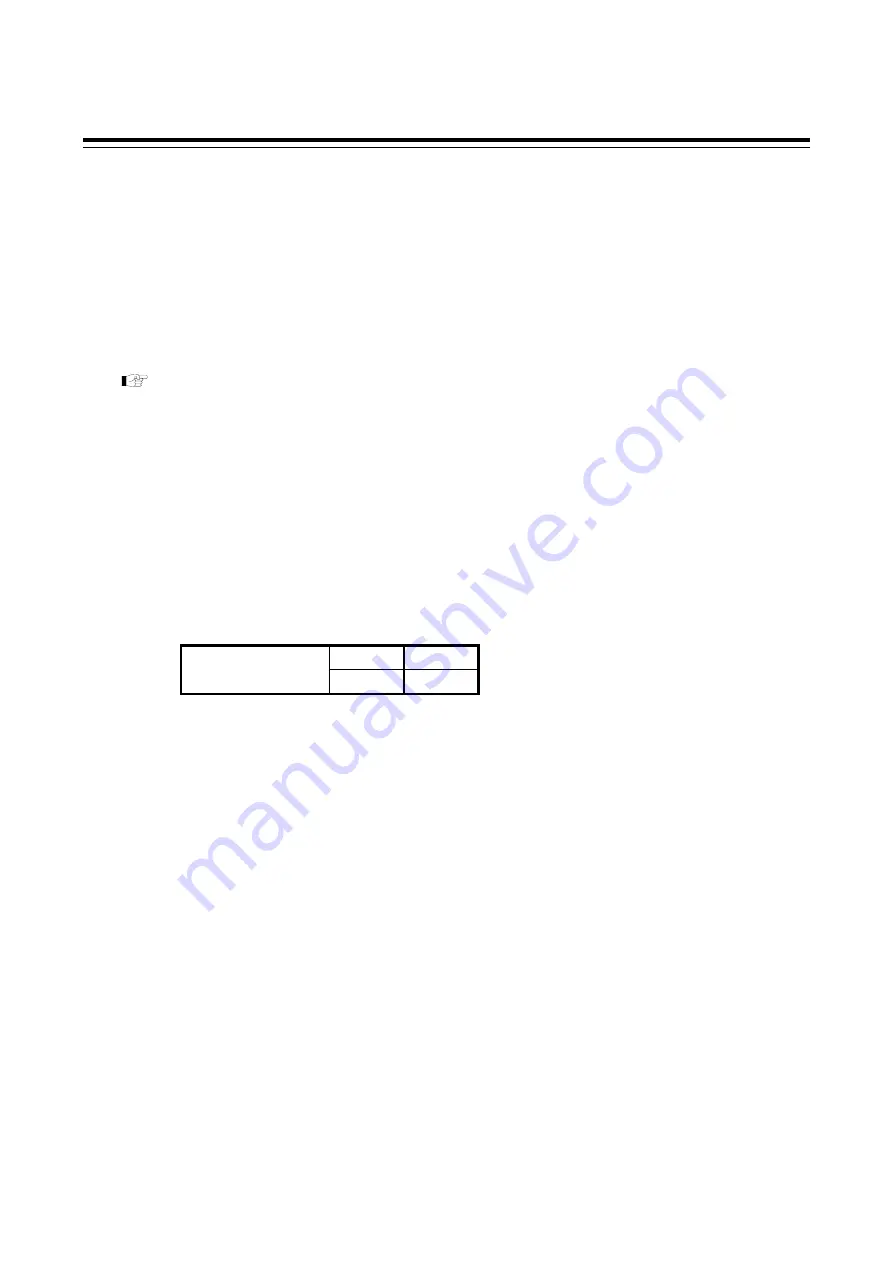
6. MODBUS COMMUNICATION PROTOCOL
IMR01J08-E1
40
Data whose decimal point’s presence and/or position depends on input range
The position of the decimal point changes depending on the input range type because the Modbus
protocol does not recognize data with decimal points during communication.
The following data can have one of three decimal point positions:
•
No decimal point
•
One decimal place
•
Two decimal place
For details, see
7. INPUT RANGE TABLES (P. 49)
.
Measured value (PV)
Analog output scale high
Peak hold value monitor
Analog output scale low
Bottom hold value monitor
Setting limiter [high]
Set value (SV)
Setting limiter [low]
Alarm 1 set value
Alarm 1 differential gap
Alarm 2 set value
Alarm 2 differential gap
PV bias
Limit action differential gap
Example: When the temperature set value is
−
20.0
°
C;
−
20.0 is processed as
−
200,
−
200 = 0000H
−
00C8H = FF38H
Set value (SV)
High
FFH
Low
38H
6.7.2 Data processing precautions
•
For 03H (read holding register), an error response message is returned when the start address is
larger than 1AH.
•
For 06H (preset single register), an error message is returned when the write address is larger than
1AH.
•
Read data of unused channel and undefined address is
0
.
•
Any attempt to write to an unused channel is not processed as an error. Data can not be written into
an unused channel.
•
If data range or address error occurs during data writing, the data written before error is in effect.