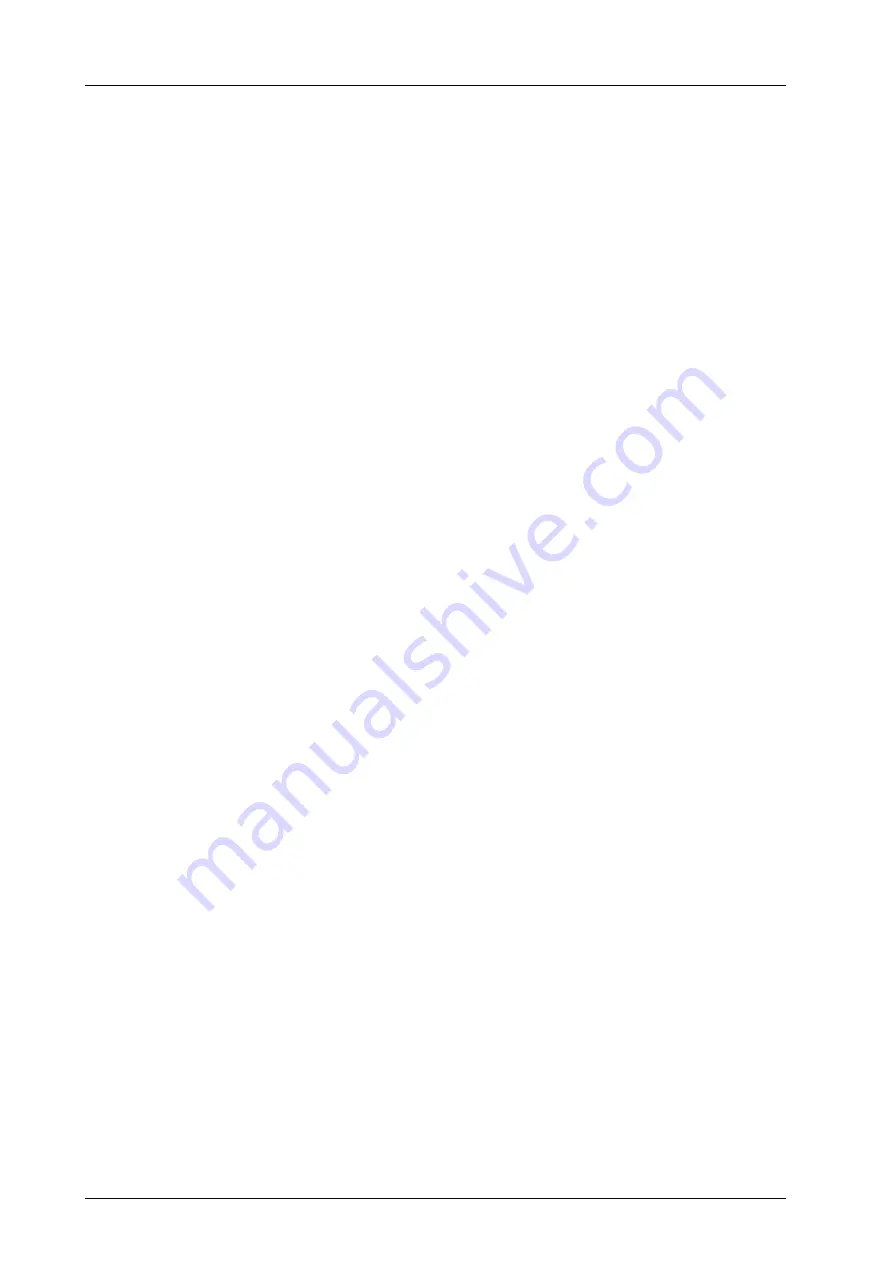
Interfaces to the Monitoring System CMC III / CMC
TC.............................
Connection of external alarm device...........................................................
Manual call point connection.......................................................................
Connection for networking..........................................................................
................................................................................................
...........................................................................................
Operating conditions and installation requirements....................................
Installation and commissioning...................................................................
Installation steps and function test..............................................................
Language setting for display and operation................................................
Checking the failure and alarm function......................................................
Installation and commissioning of additional electrical devices..................
Monitoring System CMC III / CMC
TC........................................................
Combination of systems..............................................................................
.....................................................................................
Table of contents
Operating Instructions / DET-AC III Slave / 916007 / 05-2016 / en_US
4