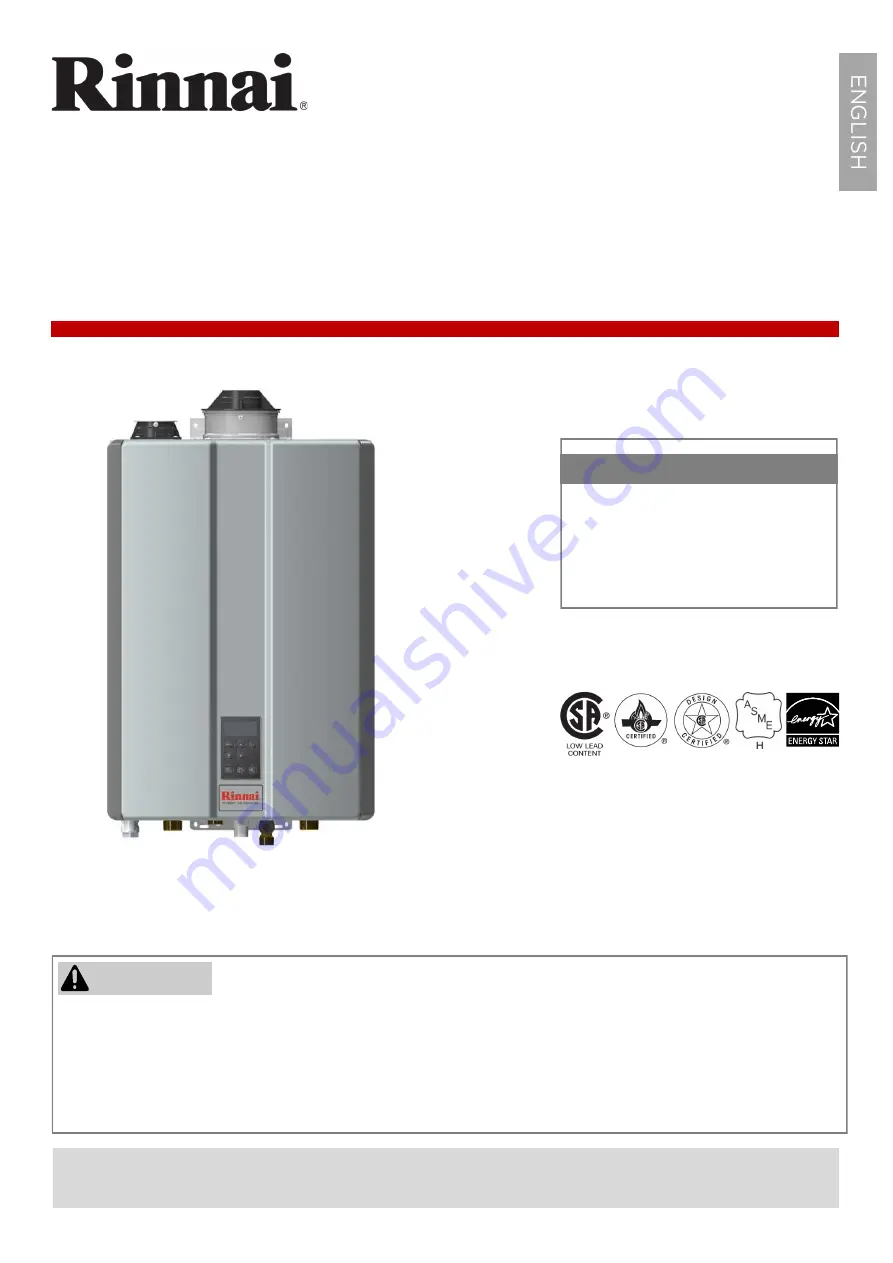
Rinnai I
-
Series Condensing Boiler Combi Manual
Central Heating and Domestic Hot Water
INSTALLATION AND OPERATION MANUAL
I
-
Series Condensing Boiler
Wall
-
Mounted, Gas
-
Fired Combi Boiler
Certified to ANSI Z21.13
and CSA 4.9
COMBI MODELS
i060C
(REB
-
A1847FF
-
US)
i090C
(REB
-
A2647FF
-
US)
i120C
(REB
-
A3558FF
-
US)
READ AND SAVE THIS MANUAL
If the information in these instructions are not followed exactly, a fire or explosion may
result causing property damage, personal injury, or loss of life.
•
Do not store or use gasoline or other flammable vapors and liquids in the vicinity of this or any other appliance.
•
WHAT TO DO IF YOU SMELL GAS
−
Do not try to light any appliance.
−
Do not touch any electrical switch; do not use any phone in your building.
−
Immediately call your gas supplier from a neighbor
’
s phone. Follow the gas supplier
’
s instructions.
−
If you cannot reach your gas supplier, call the fire department.
•
Installation and service must be performed by a qualified installer, service agency or the gas supplier.
WARNING
Summary of Contents for I Series
Page 124: ...124 Rinnai I Series Condensing Boiler Combi Manual ...
Page 125: ...Rinnai I Series Condensing Boiler Combi Manual 125 ...
Page 134: ...134 Rinnai I Series Condensing Boiler Combi Manual ...
Page 135: ...Rinnai I Series Condensing Boiler Combi Manual 135 ...
Page 136: ...136 Rinnai I Series Condensing Boiler Combi Manual 800000111 3 2019 ...