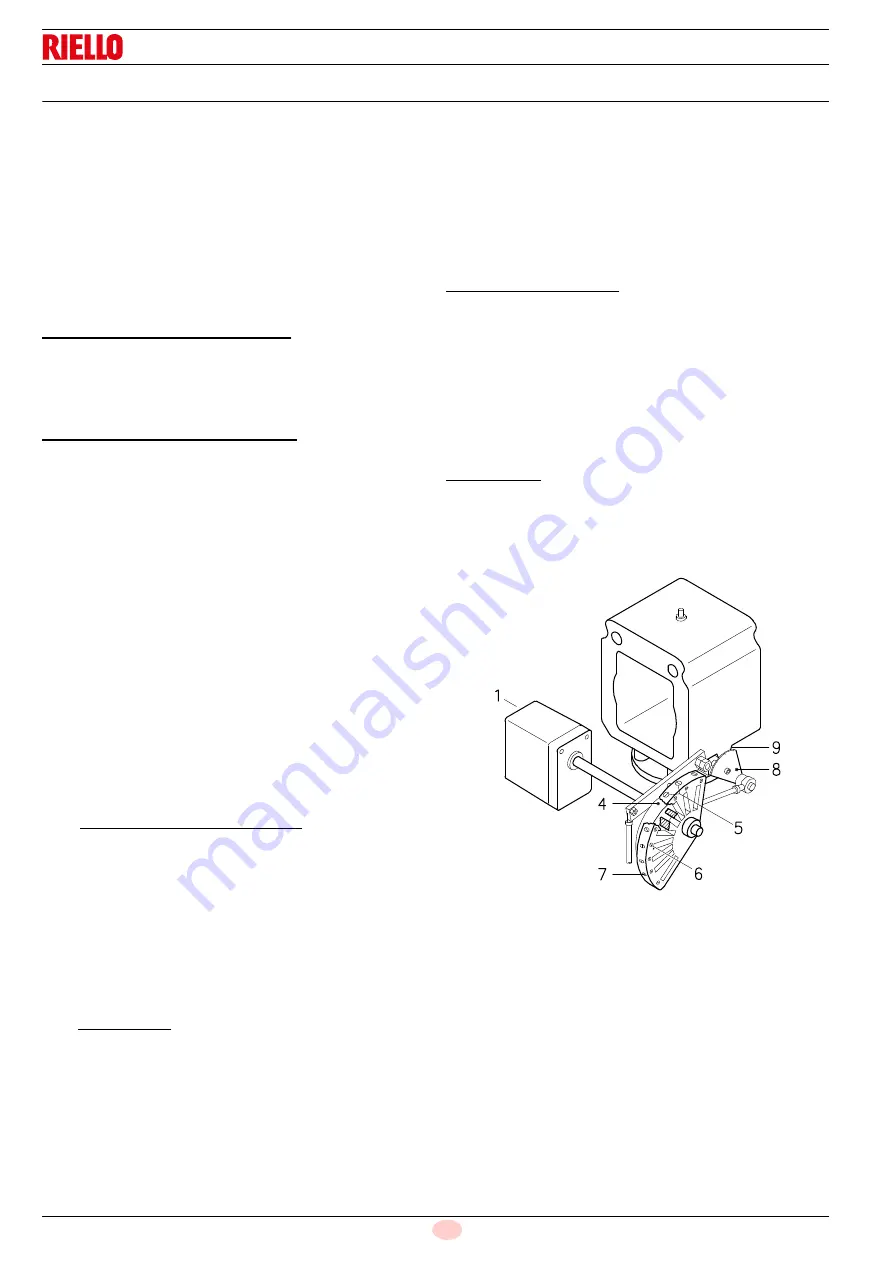
20191053
26
GB
Start-up, calibration and operation of the burner
5.6
Adjusting the burner
The optimum adjustment of the burner requires an analysis of
flue gases at the boiler outlet.
Adjust in sequence:
–
ignition output
–
output in 2nd stage
–
output in 1st stage
–
intermediate outputs
–
air pressure switch
–
minimum gas pressure switch
5.6.1
Output upon ignition
Burners with MAX output up to 120 kW
Ignition can occur at the maximum operation output level. Exam-
ple:
–
max. operation output:
120 kW
–
max. ignition output:
120 kW
Burners with MAX output above 120 kW
Ignition must occur at a lower output than the max. operation out-
put.
If ignition output does not exceed 120 kW, no calculations are re-
quired.
If ignition output exceeds 120 kW, the regulatory standard sets
that the value be defined according to the control box safety time
"ts": for "ts" = 3s, ignition output must be equal to or less than 1/
3 of the max. operation output.
Example:
MAX operation output of 450 kW.
The ignition output must be equal to or less than 150 kW with ts =
3s.
In order to measure the ignition output:
disconnect the plug-socket 1)Fig. 6 on page 12 on the ioni-
sation probe cable (the burner will fire and then go into lock-
out after the safety time has elapsed);
perform 10 consecutive ignitions with lockouts;
on the meter, read the quantity of gas burned:
this quantity must be equal to, or lower than, the quantity
given by the formula, for ts = 3s:
Vg:
volume supplied in ignitions carried out (Sm
3
)
Qa:
ignition delivery (Sm
3
/h)
n:
number of ignitions (10)
ts
:
safety time (sec)
Example
for gas G20
(9.45 kWh/Sm
3
):
ignition output 150 kW corresponding to 15.87 Sm
3
/h.
After 10 ignitions with lockout, the output read on the meter must
be equal to or less than:
5.6.2
Output in 2nd stage
MAX output must be selected within the firing rate range shown
on page 9.
In the above description, we left the burner running, operating in
1st stage.
Now turn switch 2)(Fig. 28) to the 2nd stage position: the servo-
motor will open the air damper and, at the same time, the gas but-
terfly valve at 90°.
Adjustment of gas delivery
Measure the gas delivery on the gas meter.
A rough indication can be obtained from Tab. F on page 16; just
read the gas pressure on the pressure gauge and follow the indi-
cations given on page 9.
If delivery needs to be reduced, diminish outlet gas pres-
sure; if it is already very low, slightly close the VR adjustment
valve.
If delivery needs to be increased, increase the adjuster out-
let gas pressure.
Air adjustment
Progressively adjust the end profile of cam 4)(Fig. 31) by turning
the screws 7).
–
Turn the screws clockwise to increase air delivery
–
Turn the screws anticlockwise to reduce air delivery
Key (Fig. 31)
1
Servomotor
4
Variable profile cam
5
Screws for adjusting the initial profile
6
Screws for fixing the adjustment
7
Screws for adjusting the end profile
8
Graduated sector for gas butterfly valve
9
Indicator for graduated sector 8)
Vg =
3600
Qa
(max. burner delivery)
x n x ts
Vg
=
3600
15.87 x 10 x 3
= 0.132 Sm
3
Fig. 31
D891