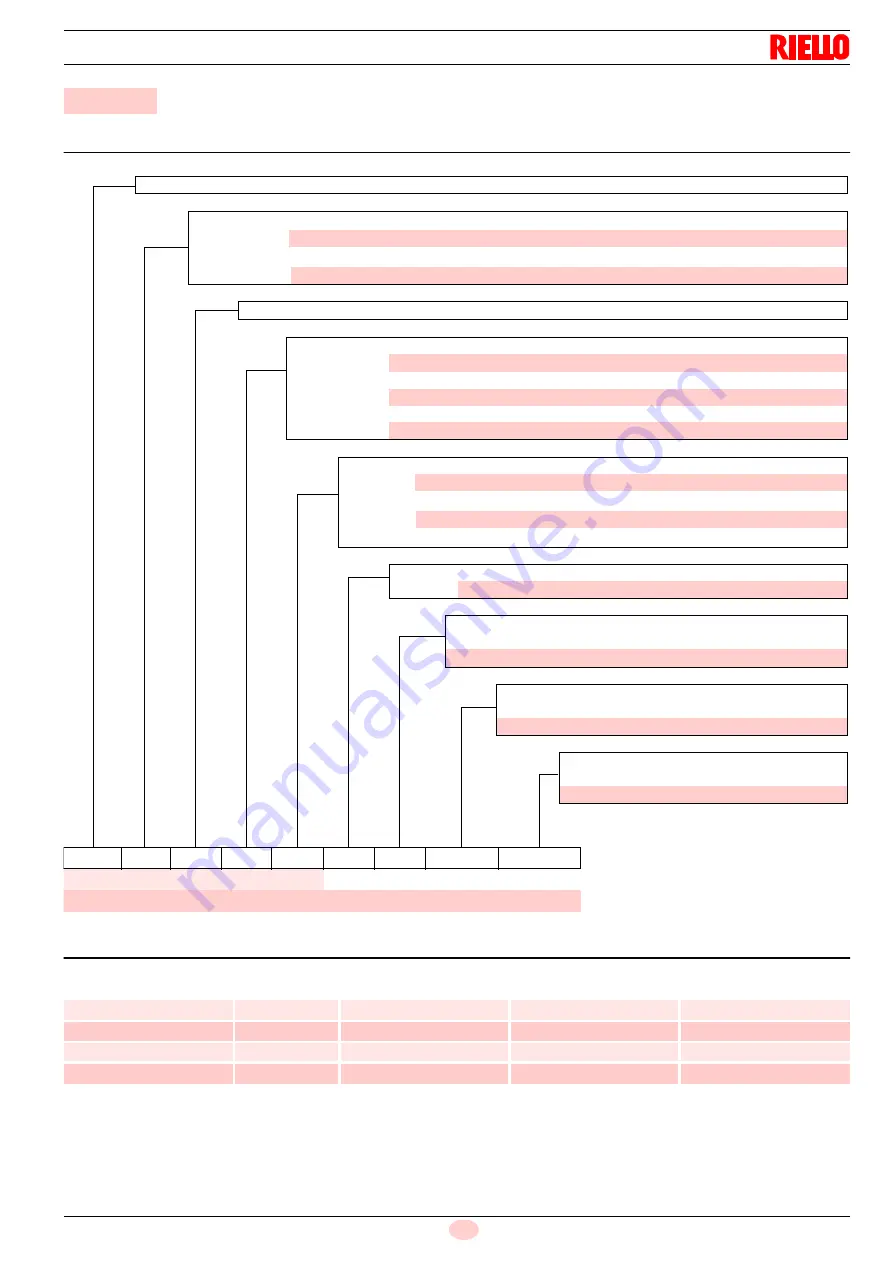
7
20121213
GB
Technical description of the burner
4.1
Burner designation
4.2
Models available
Tab. A
4
Technical description of the burner
Designation
Voltage
Start-up
Code
RLS 68/EVi MX FS1
TC
3/400/50
Inverter
20070471
RLS 68/EVi MX FS1
TL
3/400/50
Inverter
20070472
RLS 120/EVi MX FS1
TC
3/400/50
Inverter
20070476
RLS 120/EVi MX FS1
TL
3/400/50
Inverter
20070477
Class 2 EN267 - Class 3 EN676
Range:
R
Size
Fuel:
Natural gas
Light oil
Light oil / Methane
Adjustment:
Flame control system:
FS1
FS2
Standard (1 stop every 24 h)
Continuous operation (1 stop every 72 h)
Electrical supply of the system:
3/400/50
3/230/50
Voltage of auxiliaries:
230/50/60
110/50/60
R
LS
120
EVi
TC
Emission:
C11 or...
Class 1 EN267 - EN676
C22 or MZ
Class 2 EN267 - EN676
C33 or BLU
Class 3 EN267 - EN676
FS1
3/400/50
230/50/60
BASIC DESIGNATION
EXTENDED DESIGNATION
MX
3N / 400V / 50Hz
3 / 230V / 50Hz
230V / 50-60Hz
110V / 50-60Hz
Heavy oil
E
Electronic cam
SV
Electronic cam with variable speed (with Inverter)
P
Proportional air/gas valve
BP
Two stage (light oil) / Proportional valve (gas)
M
Mechanical cam
S
L
LS
N
Head:
TC
Standard head
TL
Long head
C23 or MX
C13
Class 1 EN267 - Class 3 EN676
EVi
Electronic cam with integrated Inverter
Summary of Contents for RLS 120/EVi MX FS1
Page 2: ...Translation of the original instructions ...
Page 83: ......