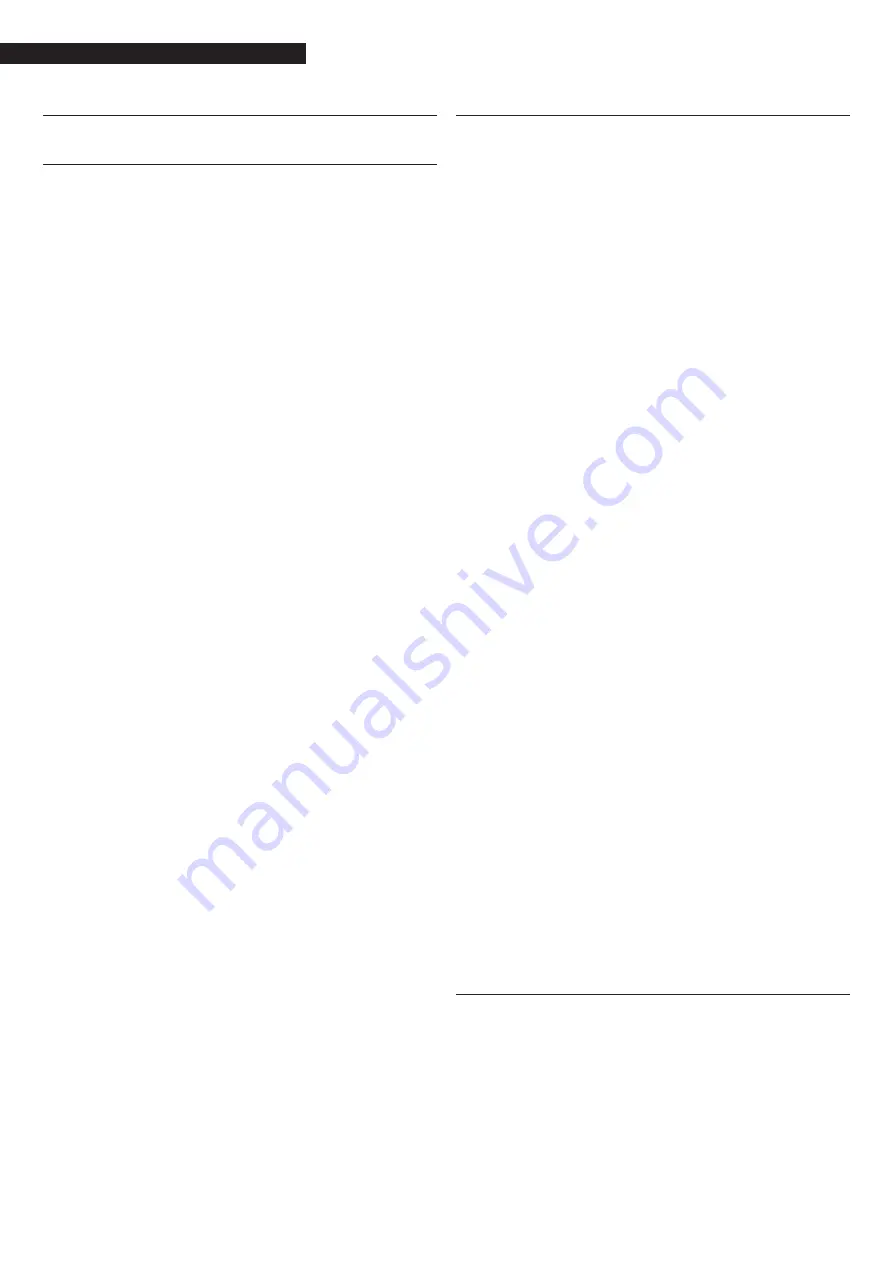
4
GENERAL INFORMATION
1
GENERAL INFORMATION
1.1
General Safety Information
9
After removing the packaging, check the condition and
completeness of the supply. If there are any problems, con-
tact the company
R
that sold the equipment.
9
This product must be installed by a legally qualified heat-
ing engineer. On completion of the installation, the install-
er must issue the owner with a declaration of conformity
confirming that the installation has been completed to the
highest standards in compliance with the instructions pro-
vided by
R
in this instruction manual, and that it con-
forms to all applicable laws and standards.
9
This product must only be used for the purpose for which it
is designed and made, as specified by
R
.
R
declines
all responsibility, contractual or other, for damage to prop-
erty or injury to persons or animals caused by improper in-
stallation, adjustment, maintenance or use.
9
The room where the boiler is installed must be proper-
ly ventilated to ensure a sufficient supply of air for correct
combustion.
9
In case of water leaks disconnect the equipment from the
power mains, close the water supply and promptly alert
Technical Assistance Service
R
or professionally qualified
personnel.
9
Regularly check that the condensate drain is free from ob-
struction.
9
The boiler must be serviced at least once a year. The failure
to perform annual maintenance work will void the warranty
of the equipment.
9
Periodically check that pressure in the central heating cir-
cuit, when cold, is approximately 1.5 bar and below the
maximum limit specified for the boiler. If this is not the
case, contact the Technical Assistance Service
R
or pro-
fessionally qualified personnel.
9
If the boiler is not going to be used for an extended peri-
od of time, perform the operations described later in this
manual.
9
This manual is an integral part of the equipment and there-
fore must be stored carefully and must ALWAYS accompany
the boiler even if it is sold to another Owner or User or trans-
ferred to another plant. If it is damaged or lost, request an-
other copy from your local Technical Assistance Service
R
.
9
This manual must be read carefully so as to ensure the cor-
rect and safe installation, operation and maintenance of
the appliance. The Owner must be adequately informed
and trained on how to operate the appliance. Make sure
that he/she is familiar with all the information required for
safe system operation.
1.2
Precautions
The operation of any appliance that uses fuel, electrical power
and water demands that a number of fundamental safety pre-
cautions be respected:
0
Do not allow children or infirm persons to operate the sys-
tem unsupervised.
0
It is forbidden to use electrical devices or equipment, such
as switches, appliances, etc. if there is a smell of gas or un-
burnt products. If so:
− Ventilate the room, opening doors and windows
− Close the fuel shut-off cock
− Ask for the prompt intervention of the Technical Assis-
tance Service
0
Do not touch the boiler while barefoot or wet.
0
Any technical or cleaning operation is forbidden before:
− removing the power supply by setting the main switch of
the equipment to (I) and the main switch of the system
to (OFF)
− closing the water and fuel shut-off valves
0
Do not tamper with or adjust the safety or control devices
without prior authorisation and instructions from the man-
ufacturer.
0
Do not plug or block the condensate drain outlet.
0
Never pull, disconnect, or twist the electrical cables coming
from the appliance even if it is disconnected from the mains
electricity supply.
0
Do not obstruct or restrict the vents in the room where the
boiler is installed. Adequate ventilation is essential for cor-
rect combustion.
0
Do not expose the boiler to the elements. It is not designed
for use outdoors.
0
Do not switch off the appliance if the outdoor temperature
may drop to below ZERO (frost hazard).
0
It is prohibited to leave inflammable substances and con-
tainers in the room where the boiler is installed.
0
Do not dispose of packaging material into the environment,
or leave it within the reach of children, since it can become
a potential hazard. Dispose of packaging material in com-
pliance with applicable legislation.
0
It is forbidden to operate the boiler without water.
0
The equipment casing must not be removed by people
without specific qualification and expertise.
1.3
Description of the appliance
The light oil condensing thermal unit
INSIEME EVO COND B/130
LN
is a hot water generator for the heating of environments and
production of domestic hot water (DHW) by means of a vitrified
heater. It can function at low temperature and is oil fuelled. The
low NOx burner features a single-stage operation and a vertical
steel combustion chamber. The boiler unit is effectively and ac-
curately insulated with a high-density glass wool mat. The con-
trol panel includes a user interface with display and an elec-
tronic board for the thermal unit adjustment and control, which
allows to manage the control and safety devices in compliance
with the regulations in force.